Flux and shield gas in welding protect the molten weld pool from atmospheric contamination, preventing oxidation and porosity. Flux creates a slag layer, while shielding gas displaces reactive gases like oxygen, nitrogen, and hydrogen. Both methods ensure stronger, cleaner welds with better appearance and structural integrity.
It’s not unreasonable for the beginner to want to know more about flux and shield gas. It could be that a few seasoned welders are not 100% satisfied with their knowledge of what flux and shield gases actually do. Some of the processes that take place are very complex and not easily explained, especially within the scope of a reasonably sized blog post like this one.
Since they are such an important part of creating good welds, as welders, we should at least know some basic information about what they do and how they do it.
How is flux and shield gas applied?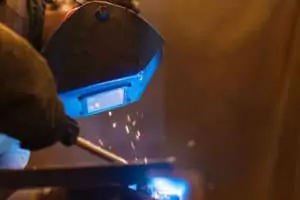
First of all, we’ll describe flux as a solid. The coating on the outside of a steel electrode or rod is known as flux. Fluxes also facilitate the bonding processes in soldering, brazing and oxy/acetylene welding. However, for this article, we’ll attempt to stay within the arc welding processes.
Shield gas is, of course, just as it sounds, a gas blown down on top of the weld pool, creating an artificial atmosphere immediately surrounding it. Its primary function is to shield the natural atmospheric gases from contacting the molten pool.
Continuous feed wire welders can utilise two types of wire: solid and hollow core. The solid wire will need shield gas to create optimum welds. Hollow core wire can be purchased with two different types of flux inside.
One type of flux contains the full spectrum of ingredients to create the best welds and is considered self-shielded. The other type of hollow core flux only does part of the job. Consequently, it requires shield gas to provide the additional protections to create optimum welds.
The American Welding Society
The American Welding Society (AWS) classifies all flux filled, hollow-cored wire as “Flux-Cored wire.” Therefore, the process of using flux-cored wire is called Flux Cored Arc Welding (FCAW).
Since two different types of FCAW wire are available, one needing shield gas, the other not, the defining acronym FCAW, can be additionally sub-categorized into FCAW-S and FCAW-G. The S and G added at the end stand for self-shielded and gas shielded, respectively.
When was the first flux coated electrode used?
At approximately the turn of the 20th century in Great Britain, a gentleman named Strohmenger coated a metal electrode with a thin coating of clay or lime. It was discovered that this thin coating did result in producing a more stable arc.
Around 1907, Oscar Kjellberg (pronounced ‘Shellberg’) of Sweden invented a covered or coated electrode along with the ESAB company. These bare iron electrodes were produced by dipping short pieces of the rod in heavy mixtures of carbonates and silicates. Kjellberg’s goal was to find a coating to protect the molten metal from atmospheric oxygen and nitrogen.
Also in 1907, Lincoln Electric produced the first portable, adjustable current arc welding machine.
Oscar Kjellberg was awarded a German patent in 1908 for the coated welding electrode. Over the next two decades, Kjellberg’s work opened the doors to developing and refining flux coated electrodes into a more usable product. It wasn’t until the 1930’s that the coated electrode found widespread use.
How exactly do flux and shield gases help the welding process?
At the instant the arc is formed and throughout the welding process, both the solid flux and shield gas act to keep atmospheric gases away from the molten pool. Solid flux does this by creating CO2 gas the instant it is burned. This gas acts in the same manner as shield gas, performing the same function: keeping oxygen, nitrogen, and moisture away from the molten weld pool. Without it, oxidation will make the metal in the weld more brittle and contain more porosity.
Before shielding was introduced and improved, arc welding was seen as inferior to other methods of constructing steel ships and buildings due to the brittleness of the welds at the time.
Other abilities of shield gases include:
- The stabilization of the arc. A more stabilized arc will weld more consistently with less spatter.
- Controlling the bead profile. For instance, high CO2 mixtures will typically create a more convex or raised bead profile, whereas Argon will help control the profile to the point it is typically flatter.
- The ability to affect penetration rates. Pure CO2 puts more energy into the weld pool, helping create deeper penetration rates. Pure Argon and a high Argon to CO2 blend reduce the energy in the pool, allowing the welding of thinner metals with less burn-through.
In addition, flux has the ability to:
- Form a layer of protective slag which also shapes the weld
- Infuse alloys into the weld to increase mechanical properties
- Reduce the surface tension of the molten pool
- Clean the metal surfaces and lift the impurities to the surface
- Help the filler metal deposition rates and the joining of the filler metal to the base metals

In Conclusion
Welding would never have developed without the discovery, development, and implementation of flux and its partner, shield gas.
The shipbuilding industry was transformed by the developments in welding leading up to WWII. Previously, ships built with plates secured by rivets might weigh as much as an additional 300 tons. The additional 300 tons was due to the combined weight of the rivets alone. Ships could be built much lighter and faster by simply welding the plates together. The improvement in steel composition leading up to and during WWII also increased the strength and effectiveness of ships built with the welding process.
The high-rise building industry was transformed once welding became the normal form of construction. The strength at each joint was increased from 50-70% of the base steel’s strength to 100% when welded together instead of riveting. In addition, the total weight of the structure would end up weighing at least a third less. Buildings could go up faster, and be built larger and cheaper per square foot.
Additionally, welding applications transformed the process of building passenger elevators, major pipelines, boilers, tanks, and many other types of structural equipment.
So now, the next time you look at the coating on your electrodes or at that bottle of Argon on your MIG welder, you may have a much greater level of respect for them.