For TIG welding, pure argon is the most commonly used shielding gas due to its excellent arc stability and compatibility with various metals. However, argon-helium mixes or pure helium may be used for specific applications like welding thick aluminum or copper alloys, requiring increased heat input.
Argon and helium can be used in pure form or a mixture. Hydrogen can’t be used alone because it will harm your metal, but it has some benefits when mixed with argon or helium.
Before understanding why we use those particular gasses and sometimes mix them, you need to know briefly about the TIG welding process.
Table of Contents
TIG Welding: A Quick Overview
TIG welding utilizes a non-consumable electrode. The word (non-consumable) comes from that electrode’s extremely high melting point.
In other words, the resulting heat will melt and weld the base metal, not the electrode itself.
For this process to start, there must be an electric circuit like a battery. The electrode is usually the negative pole while the metal you’re welding is the positive pole.
The point of contact between both poles is where the welding process occurs. An (arc) is created at this point, producing the high temperature. The molten metal in the welding area may react with the water vapor and the oxygen in the atmosphere, resulting in undesirable impurities.
This is when shielding gases like argon, helium, and hydrogen come into play. Being inert, these gases will cover the welding area and prevent the molten metal from reacting with any air elements.
Now let’s understand the characteristics that made us use those particular gases.
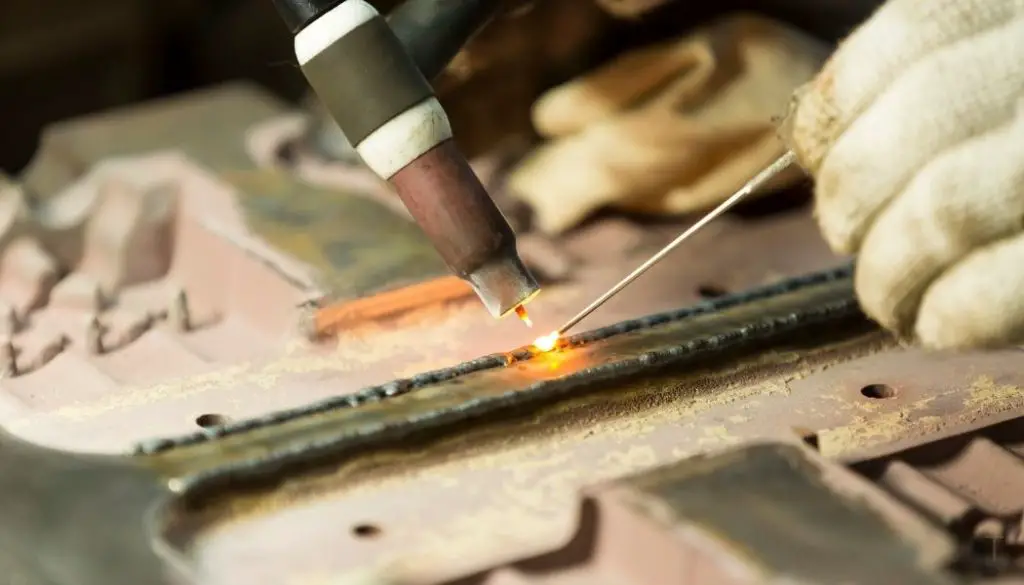
TIG Welding With Argon
The most common technique is using 100% pure argon as a shielding gas. Argon is cheap and widely available which makes it highly popular.
Argon also has a lower ionization potential, resulting in better arc starts and consistency than other inert gasses.
The arc starts when the electrode comes in contact or close to the base metal. Argon provides a smoother arc creation whether you use scratch start, lift start, or high-frequency start.
Since argon is a heavy gas, you should only restrict it to flat horizontal surfaces. The gravity will help keep the argon gas in place, shielding the welding process.
Pure argon often gets the job done without mixing with other gases. It’s a good choice for welding aluminum, mild and austenitic stainless steel, and magnesium.
TIG Welding With Helium
We use 100% percent pure helium when we require higher temperatures. Helium has a higher thermal conductivity than argon, so it produces higher heat outputs.
The higher temperature allows you to weld faster and more efficiently. The heat also penetrates deeper into the metal, ideal for welding thicker materials.
However, helium has higher ionization potential, which results in inconsistent arc starts, especially if your welding machine only allows you to scratch start.
This is why 100% helium is usually restricted to automated TIG weldings. Using pure helium in manual welding will yield challenges in starting the arc and maintaining it.
Helium is also more expensive than argon and much lighter, making it more suitable for overhead welding as the gas will travel upwards.
However, if you’re using the flat welding position, you’ll have to use twice the amount of helium (due to its lightweight) to stabilise the shielding, resulting in even more cost.
TIG Welding With Hydrogen
We don’t use 100% pure hydrogen in TIG welding unlike argon and helium. It’s highly combustible and causes stress on the base metal, eventually leading to hydrogen-induced cracking.
Instead, hydrogen is mixed with argon to increase the arc voltage, resulting in a higher temperature and depth-to-width ratio. This makes hydrogen a useful gas if you are welding single layers.
Mixing hydrogen and argon also provides surface oxide cleaning, making the mix highly desirable for welding austenitic stainless steel.
TIG Welding Gas Blends
Here are two of the most common TIG welding gas blends:
Argon and Helium
Argon and helium mixture is the most common during welding. The usual percentages are 75% helium and 25% argon.
You may reduce the helium percentage to provide better arc start and stability but lose some temperature and penetration depths.
On the other hand, increasing the helium percentage will provide a better and faster ability to weld thicker metals.
Argon and Hydrogen
Hydrogen can be added to hydrogen by up to 5%. This allows for higher voltage, heat, and penetration which helps with thicker metals.
The mix also allows for better arc stabilization, resulting in increased welding speeds.
How to Choose the Right Gas for Your Job
Here’s a small list for better functional suitability:
1. When to Use Argon
Without repeating all the characteristics mentioned above, it’s safe to say that with enough time and persistence, argon will get the job done in 90% of the cases.
Whether it’s mild steel, stainless steel, or aluminum, argon is your jack of all trades.
2. When to Use Helium
If your material has a low gauge (high thickness), you might want to add helium up to 75%. Keep in mind that helium will reduce arc stability. So, unless you’re welding an exceptionally thick metal, you don’t need to amp up the percentage of argon to 75%
Additionally, the location of your metal-to-be-welded is detrimental. The more horizontally flat your metal surface is, the less desirable helium will be, and vice versa.
3. When to Use Hydrogen
Like helium, hydrogen isn’t necessary unless you need extra heat and penetration. However, welding stainless steel may be more desirable because it cleanses oxidation from the metal surface.
However, be careful not to increase the percentage in the mix above 5% to avoid surface cracking.
In Conclusion
Argon is the best and most common gas for manual and automated TIG welding processes. It’s reliable, cheap, readily available, and produces a stable arc.
If you have an inclined surface or a thicker material, you may want to add some hydrogen or helium to the mix. This will provide you with better heat, penetration, and efficiency.