For welding rusty metal, choose a rod high in silicon or manganese to produce thick slag, effectively removing contaminants. The versatile and popular 7018 electrode is ideal, boasting superior slag formation and delivering strong, clean welds even on oxidized surfaces.
This rod is a high-strength, low-hydrogen electrode known for its high penetration capabilities, smooth arc, and easy control. These characteristics make it ideal for heavy-duty welding and welding in overhead and vertical-down positions.
Stick welding is a popular method for welding various metal types and thicknesses. However, selecting the right welding rod is important to ensure a strong and durable weld when working with rusty metal.
In this article, I will discuss the best stick welding rods for rusty metal and provide a buyer’s guide to help you make an informed purchase.
- All position welding
- Low hydrogen rod for general purpose
- Excellent for tack welds and out of position welding
- All Position Welding Rod
- Deep Penetration
- 14-inch Length
- 1/8-inch Diameter
- 10 Pound Box
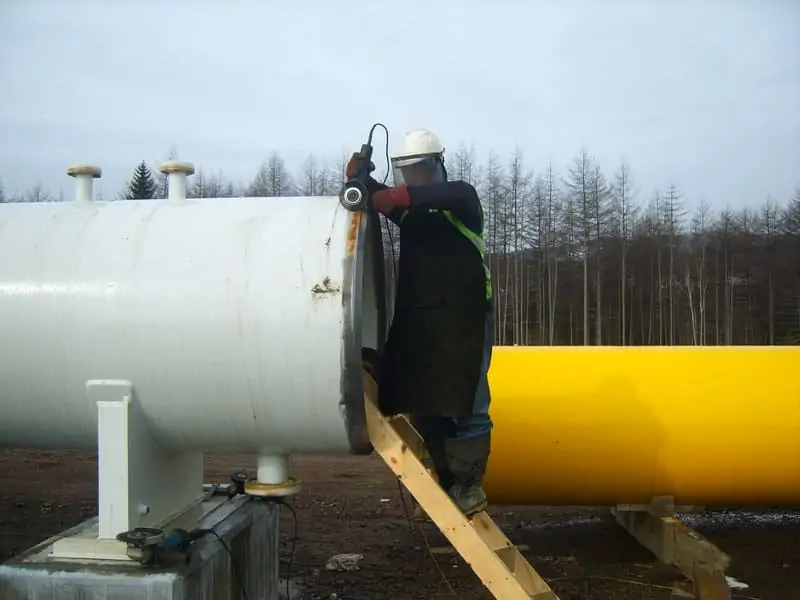
Table of Contents
Why is Rust Important in Welding
When welding on rusted metal, the rust acts as a barrier between the metal and the rod, preventing proper adhesion of the weld. This leads to weaker welds, more prone to cracking and failure.
Rust can also cause porosity in the weld, which is small holes in the weld that can weaken its strength.
Additionally, welding on rusty metal can produce a lot of smoke and fumes that harm the welder. As the rust is burned off, releasing harmful particles into the air.
Rod | Type | Characteristics |
---|---|---|
7018 | High-Strength, Low-Hydrogen | High penetration, smooth arc, easy to control, heavy-duty welding, overhead and vertical-down welding |
6010 | Low-Hydrogen, Iron Powder | Heavy-duty welding, easy slag removal, vertical-up and overhead welding |
6011 | Low-Hydrogen, Iron Powder | Heavy-duty welding, easy slag removal, vertical-up and overhead welding, out-of-position welding, low spatter. |
E7018 Welding Rod for High Strength
The first type of welding rod to consider for rusty metal is the E7018. This rod is known for its deep penetration and high strength, making it ideal for welding thick and dirty metal. The Lincoln Electric Excalibur 7018 MR, Hy-Weld 7018 Electrodes, US Forge E7018 Rods, and Forney 30681 E7018 Welding Rod are all great options.
E6010 Welding Rod for Tight Spaces
Another popular welding rod for rusty metal is the E6010. This rod is known for penetrating through rust and other contaminants on the metal surface, making it a great choice for dirty and rusty metal. The Hy-Weld 6010 Electrodes, Forney 31610 E6010 Welding Rod, Blue Demon 6010 Electrodes, and Lincoln Electric 6010 Electrode are all reliable options.
E6011 Welding Rod for Heavy Rust
The E6011 rod is also a good choice for welding rusty metal. It is a fast-freeze rod known for its strong and smooth welds. The Lincoln Electric Fleetweld 180 (6011) is a great option for welding rusty metal. The Forney 31205 E6011 Welding Rod and Hy-Weld 6011 Electrodes are also solid alternatives.
Welding Rod Characteristics to Consider
When purchasing a welding rod for rusty metal, there are a few important factors to consider. Penetration is important, as it determines how deep the rod will penetrate into the metal.
Avoid a fast-freeze rod, as it may not be the best choice for welding rusty metal.
Fast-freeze rods, also known as “fast-fill” or “fast-deposit” rods, are stick welding rods with a high deposition rate typically used for welding in tight spaces or making quick repairs. However, when welding rusty metal, it is important to avoid using fast-freeze rods for several reasons:
- Poor penetration: Fast-freeze rods have a high deposition rate, so they quickly deposit a large amount of filler metal. However, this can result in poor penetration into the base metal, weakening the weld and making it more susceptible to cracking or breaking.
- Inadequate cleaning: Fast-freeze rods are not designed for heavy cleaning, so they may not effectively remove rust or other contaminants from the base metal before welding. This can result in a weak weld that is more prone to breaking or cracking.
- Slag: Fast-freeze rods produce more slag than other types of welding rods, which can make it difficult to see the weld and can also make it more difficult to clean the weld after it has cooled.
- Poor weld quality: Because fast-freeze rods deposit a large amount of filler metal quickly, they can result in a weld that is not as smooth or as strong as one made with a slower-depositing rod.
The slag type is also important, as it determines how easy or difficult it is to remove the slag from the weld. The package size is also a consideration, as it determines how much rod is available for your project.
High penetration capabilities:
A welding rod with high penetration capabilities can reach deep into the metal, which is important when welding on rusty metal as it can break through the rust barrier and make a strong weld.
Smooth arc:
A smooth arc allows for easy control and a consistent weld, which is important when welding on rusty metal as it can be challenging to maintain a consistent weld due to the uneven surface of the rust.
Easy slag removal:
Welding rods with easy slag removal are good for welding in overhead and vertical-down positions. The slag, a layer of solidified flux that covers the weld, can be easily removed with a chipping hammer or wire brush.
Low-hydrogen:
Welding rods that are considered as low-hydrogen electrode, meaning less prone to cracking, are important when welding on rusty metal as it can contain moisture which can cause hydrogen cracking in the weld.
High-strength:
A high-strength welding rod can withstand heavy-duty welding and provide a strong weld, which is important when welding on rusty metal as it may be more prone to breaking or bending.
FAQ
How do you prepare rusty metal for welding?
Preparing rusty metal for welding involves several steps to ensure that the weld is strong and durable.
Clean the metal:
Use a wire brush or grinder to remove as much rust as possible from the metal. This will ensure that the weld is made on clean metal and not rust, which can weaken the weld.
Remove any loose rust:
Use a wire brush or scraper to remove loose rust flaking or peeling off the metal. This will prevent the rust from getting into the weld and weakening it.
Clean the metal with a degreaser:
Use a degreaser to remove any oil or grease from the metal. This will help to ensure that the metal is clean and free of any contaminants that may weaken the weld.
Dry the metal:
Make sure the metal is completely dry before welding. Any moisture on the metal can cause hydrogen cracking in the weld, which can weaken the weld.
Apply a rust inhibitor:
Apply a rust inhibitor to the metal to help prevent rust from forming on the metal after welding. This will help ensure that the weld will last a long time.
Preheat the metal:
Preheating the metal before welding can help to reduce the risk of hydrogen cracking in the weld. This can be done by using a torch or an electric heating element.
What Happens if You Weld Rusty Metal with the Wrong Welding Electrode?
Welding rusty metal with the wrong welding rod can have several negative consequences, including:
Porosity:
If the welding rod is not specifically designed for welding rusty metal, it can create small holes or pores in the weld known as porosity, which weakens the strength of the weld.
Lack of penetration:
The wrong welding rod may not be able to properly penetrate through the rust layer and create a strong bond between the base metal and the filler metal.
Inadequate cleaning:
If the rust is not properly cleaned before welding, the welding rod may not be able to properly penetrate through the rust layer and create a strong bond between the base metal and the filler metal.
Inadequate slag removal:
The wrong welding rod may not produce the right type of slag, making it harder to remove, which can lead to weak spots in the weld.
Inadequate strength:
The wrong welding rod may not produce a strong weld, which can lead to the failure of the welded structure.
Poor corrosion resistance:
Welds made with the wrong welding rod may be less corrosion-resistant and not last as long as they should.
Overall, welding rusty metal with the wrong welding rod can result in a weaker, less durable and less corrosion-resistant weld, and can potentially lead to failure of the structure.
Conclusion
In conclusion, selecting the right welding rod for rusty metal is crucial for achieving strong and durable welds. The E7018, E6010, and E6011 rods are all great options for welding rusty metal. Consider factors such as penetration, slag type, and package size when purchasing a welding rod to ensure you make the best choice for your project.