4043 and 5356 are the best welding rods for aluminum. These filler rods are made of aluminum alloy and have low melting points, which makes them suitable for welding aluminum.
The choice between 4043 and 5356 welding rods will depend on the specific application and the desired outcome.
4043 is commonly used for welding aluminum alloys with a high silicon content, while 5356 is often used for welding marine-grade aluminum. 4047 can also be used for aluminum with a low silicon content.
- Aluminum with High Silicon Content (6xxx series)
- Used in automotive, shipbuilding, and general fabrication
- Marine Grade Aluminum (5xxx series)
- Used where aluminum will be exposed to salt water or other harsh environments
- Aluminum with Low Silicon Content
- Used in applications where high strength is required
Table of Contents
Can You Weld Aluminum?
Yes, aluminum can be TIG welded using a specific welding rod and process. However, welding aluminum requires special techniques and equipment to prevent cracking and ensure proper weld quality. It is also essential to clean and prepare the aluminum surface before welding to prevent contamination.
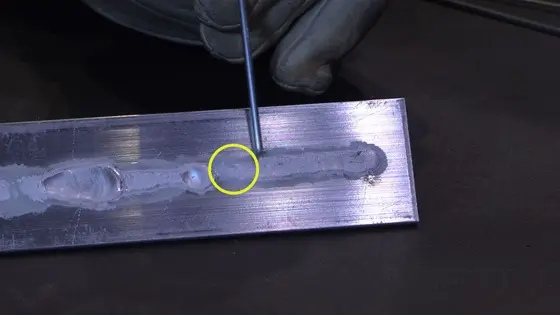
E4043
The numbers in a welding rod, such as 4043, represent the filler metal classification system. The filler metal classification system provides information about the composition and properties of the welding rod.
In the case of 4043 welding rod, the first two digits (40) indicate the minimum aluminum content of the welding rod, which is 40%. The last two digits (43) indicate the specific composition of the welding rod, which includes elements such as aluminum, silicon, and magnesium.
This classification system is commonly used for welding aluminum and other materials, and is governed by international standards such as AWS (American Welding Society) and ISO (International Organization for Standardization).
- Tensile Strength: 250-400 MPa
- Melting Point: 1065 – 1175°F
- Conductivity: 42% IACS (-O)
- Density: .097 lbs/cu.in
- Primary Alloying Materials: Silicon
This filler rod is not be suitable for welding aluminum alloys with high magnesium content.

E5356
E5356 filler rod has good corrosion resistance, which is important for preventing rust and other forms of corrosion in marine environments, where exposure to salt water and other corrosive substances is common.
I suggest using 80-150 volts, depending on the diameter of the rod.
- Tensile Strength: 340-480 MPa
- Melting Point: 1060 – 1175°F
- Conductivity: 29% IACS (-O)
- Density: .096 lbs/cu.in
- Primary Alloying Materials: Magnesium, Manganese, Chromium, Titanium
E5356 filler rod is well-suited for marine aluminum because of its low melting point, good corrosion resistance, adequate strength, and good welding characteristics, which make it well-suited for use in a challenging marine environment.
This filler rod is not be suitable for welding aluminum alloys with high silicon content.
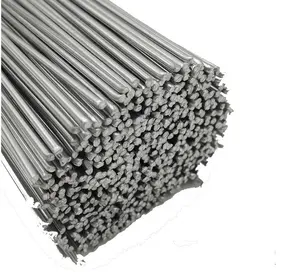
Welding Rod Characteristics to Consider
The following are some of the characteristics of a welding rod that impact its ability to weld aluminum:
Composition:
The composition of the welding rod, including its elements and proportions, affects its ability to weld aluminum. Aluminum welding rods typically contain aluminum alloy and are designed to have low melting points, good welding characteristics, and adequate strength.
Some filler rods contain high amounts of magnesium or silicon, which can improve the strength and hardness of the weld.
The composition of a filler rod can also affect the appearance of the weld. Some filler rods contain alloys designed to improve the color and finish of the weld, which is important for applications where the appearance of the weld is a critical factor.
Melting Point:
The melting point of the welding rod is important because it affects the ability of the rod to flow and bond with the aluminum being welded. Welding rods with low melting points are typically better suited for welding aluminum, as they are less likely to crack or cause other issues during the welding process.
Typically, welding rods with melting points between 1100-1300°F are suitable for welding aluminum
The melting point of a filler rod can impact its ability to weld aluminum in several ways:
- Weld Pool Formation: If the melting point of the filler rod is too low, it can result in a weld pool that is too fluid, making it difficult to control and resulting in a weak or porous weld. If the melting point is too high, the filler rod may not melt and mix with the base metal, resulting in an incomplete weld.
- Weld Pool Stability: If the filler rod has a high melting point, it can help to maintain a stable weld pool and prevent the filler rod from burning away or boiling.
- Weld Quality: A filler rod with a lower melting point may result in a weld with a lower tensile strength or a lower corrosion resistance, while a filler rod with a higher melting point may result in a harder and more brittle weld.
- Weld Cooling Time: The melting point of a filler rod can also affect the cooling time of the weld, which can impact the properties of the weld and the final finished product.
Strength:
The strength of the welding rod is also an important factor in its ability to weld aluminum, as a weak rod may not provide adequate support for the welded joint.
A filler rod with high strength is important for applications where the welded joint will be subject to high stress levels, such as in structural applications or in the construction of heavy equipment. In these cases, a filler rod with a low strength may not be able to withstand the stress and pressure of the application, which can result in a weak or brittle weld that is prone to failure.
In contrast, for applications where the strength of the weld is not a critical factor, a filler rod with lower strength may be sufficient. For example, in artistic or decorative applications, a filler rod with a lower strength may be suitable as long as it provides a smooth and attractive finish.
Diameter:
The diameter of the welding rod affects the size of the weld and the amount of filler material required. A larger rod will generally produce a larger weld, while a smaller rod may be more maneuverable in tight spaces.
Corrosion Resistance:
The corrosion resistance of the welding rod is important if the aluminum being welded will be exposed to corrosive environments, such as salt water. This is generally dictated by the composition.
How Do You Clean Aluminum Before Welding?
Cleaning aluminum before welding is important to ensure a strong and quality weld. The following steps can be taken before welding:
- Remove any dirt, oil, or grease from the surface of the aluminum using a degreaser and a clean cloth.
- Use a sandpaper or grinder to remove any oxidation or corrosion from the surface.
- Clean the aluminium surface with a solution of equal parts water and vinegar, or with a specialized aluminum cleaner.
- Rinse the surface thoroughly with water to remove any residue from the cleaning solution.
- Dry the surface with a clean cloth or allow it to air dry completely before welding.
It is important to avoid using any steel brushes or other tools that can leave behind metal contaminants, as these can weaken the weld. It is also important to avoid touching the aluminum with bare hands, as oils and salts from the skin can also contaminate the aluminum.
Conclusion
Choosing the right filler rod for welding aluminum is essential for achieving a strong and durable weld. E4043 and E5356 are two popular filler rods for welding aluminum, each with unique characteristics and specifications. E4043 is a versatile filler rod well-suited for many aluminum welding applications. At the same time, E5356 is a filler rod that is particularly well-suited for marine aluminum due to its high magnesium content.
The specifications of these filler rods, including their melting point, chemical composition, tensile strength, and welding current, are important factors to consider when choosing the right filler rod for a specific application.