Brazing joins metals using a filler metal above 840°F (450°C) without melting the base metals, while welding fuses base metals by melting them. Welding typically provides stronger joints, whereas brazing is suited for delicate or dissimilar materials and complex assemblies, with lower heat and distortion risks.
So, in which situation is one or the other better? And what equipment do we need to use these two different techniques? Fortunately for you, you won’t have to do all the thinking, as in this article, I’ll share all that you need to learn about brazing vs. welding.
Table of Contents
What Is Brazing?
In brazing, you only melt the filler metal instead of also melting the base metal. The liquified filler is applied in a joint between the pieces, forming a bond. It accomplishes this by a principle known as ‘capillary action.’
There are a few methods of brazing, including:
- Torch
- Vacuum
- Furnace
- Induction
The filler metal is heated above its melting point in a brazing operation. It’s protected by flux materials to prevent it from reacting with the atmosphere. Without it, the joint that’s produced may have unwanted impurities.
The filler’s always a metal that melts at a temperature over 842°F, but it’s never above that of the base materials.
The base materials are preheated for the filler to fuse. However, it’s never heated anywhere near the melting point.
The liquified filler is then applied between the base materials, fusing the pieces. Once it cools down and solidifies, it forms a joint.
Brazing is most commonly used to weld:

What Is Welding?
Welding works by melting the base materials and then joining them. It may or may not involve shielding gasses or filler metals.
There are different kinds of welding processes, which include:
- Friction
- Electron Beam
- Arc
- Laser
- Resistance
Out of these methods, arc welding is the most commonly used.
In a welding operation, a portion of the base material is heated above the melting point. The methods used in welding can melt even metals with the highest melting points.
The resulting points of molten metal are then joined with a filler material. These need to be protected from the atmosphere to prevent any impurities. For that, we can either use flux material or shielding gas.
Brazing vs Welding
These two different metal-fusion processes have different advantages and disadvantages. It all boils down to your preferences and purposes.
Advantages of Brazing
- Joints made using brazing come with very little stressing and thermal distortion compared to welding.
- Brazing uses far less energy than wielding, as it requires less heat to operate. As such, it’s far cheaper to use.
- Because it only melts the filler metals, brazing can join two different base materials.
- Brazing doesn’t require heat treatment after processing.
- As the base materials are never melted, they can keep most of their physical properties.
- It’s easier to learn to braze than to weld. The latter requires precision in the application of heat and deposition of the filler; the former relies on the principle of capillary action.
- Suitable for extremely thin metals, as extreme temperatures could damage these.
Advantages of Welding:
- A joint made by welding is typically stronger than the base materials it was made from. Welding is the better process of making strong, permanent joints.
- Due to the intensity of heat used in welding, it’s more localized. This makes it practical to join metal pieces at one point instead of a broad area.
- Welding is well suited to joining larger pieces of metal.
Disadvantages of Brazing:
- Brazing forms joints with less strength than those produced by welding.
- Brazen joints can’t be used in higher-temperature environments, unlike welds.
Disadvantages of Welding:
- Welds may require a post-processing heat treatment to fix stresses in the joint.
- Usually, welding can only fuse similar base materials.
- The intensity of heat in welding can result in distortion, warping, and cracking of your weld.
Equipment Required
As brazing and welding are different processes, the equipment they need is sometimes different.
Brazing Equipment
- Filler material and flux solution. The most commonly used filler metals are fluorides, alkalis, chlorides, and fluoroborates.
- Either furnace, induction, chemical bath heater, or torch for heating the filler.
- Protective gear, including safety glasses, hearing protection, welding boots, auto-darkening welding helmet, welding gloves, and a fire-resistant coat.
- A secure electrical supply.
Welding Equipment
- Welding torch
- Electricity source
- Filler material
- Shielding gas, such as helium, argon, or a mixture of both.
- Fuel cylinder
- Oxygen cylinder
- Protective gear
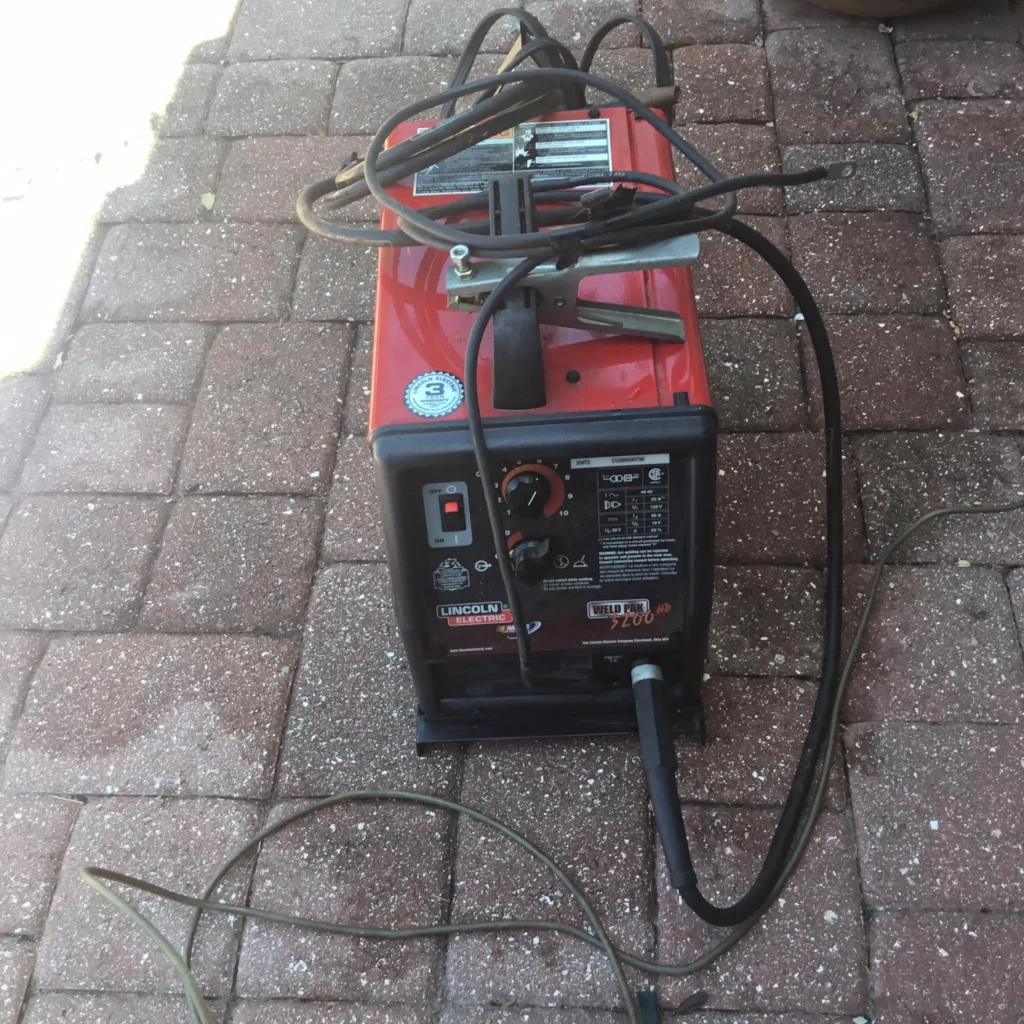
When to Use Each?
Brazing is ideal for manufacturing parts with different metals and complex designs. It’s also suitable for mass production as it’s easier and uses less heat.
On the other hand, welding excels on larger components that require more durability, such as vehicle frames.
In Conclusion
In brazing, only the filler metal is melted, while welding melts both base and filler materials. It also requires less heat than welding.
Finally, brazing is suitable for mass production and complex designs, while welding is better for parts that require durability.