Common brazing problems include insufficient joint penetration, joint gaps too wide or narrow, overheating, lack of proper cleaning, incorrect filler metal, flux issues, and porosity. Proper joint preparation, using the right filler and flux, maintaining optimal temperature, and good brazing technique can help avoid these issues.
Brazing is another form of joining metal together. It is frequently suggested as an alternative to welding because it is simpler and requires less equipment. Brazing works by heating a filler metal until it melts, acting as a glue between two metal pieces. It requires a lower melting point and is often easier than welding while being just as sturdy.
However, that doesn’t mean brazing is free from problems. Here are some common problems you may encounter while brazing and how to troubleshoot them.
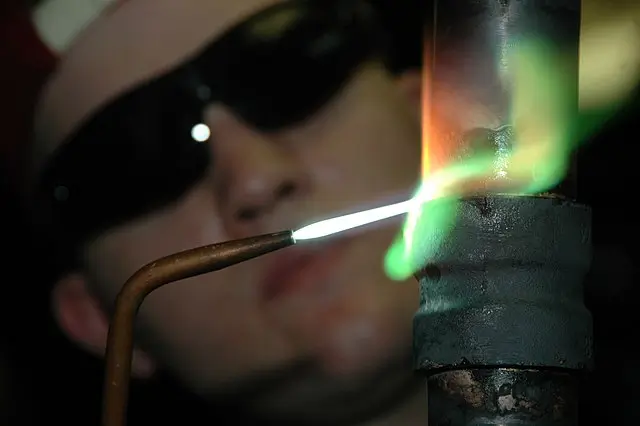
Table of Contents
The Condition of the Tips
To braze metal, the main equipment you need is a brazing torch. This equipment uses a tip to precisely apply heat to your joint. However, if the tip is in poor condition, the quality of your braze will also be poor. For some applications, you need to clean and apply a special coating to the tip. If you don’t do this properly, the tip will not perform, and you will have problems with your base material.
Another common problem with the tip that beginners often run into is breaking or falling.
To prevent problems with your tip, make sure you are cleaning the brazing torch tip thoroughly. This will prevent oxidation and damage to your equipment. Also, make sure you are working with the right materials for your project. Using the right alloy or tip is very important for brazing.
Improper Plate Cleaning
When you’re brazing, cleaning your materials thoroughly is very important. If debris is caught on the edges, the bond will be corrupted. Brazing will trap impurities on the surface. Improper cleaning can also lead to oxidation, which you always want to avoid when working with metals.
Here are some tips for cleaning your plates properly when brazing:
- Go over the edges with a wire brush
- Sand down any rough patches to make them smooth
- Try chamfering or cutting the edges at a sloped angle
Using the Wrong Braze Alloy
One of the most important decisions you can make when brazing lies in choosing the right alloy, or filler metal. This is the metal you melt and use as an adhesive to stick together two plates.
Using the wrong alloy will result in a weak bond if it does not interact well with the metals you try to join. Sometimes, compounds in the metal can interact poorly with compounds in the alloy. For example, a metal that contains sulfides will interact poorly with a phosphorous-based alloy. Finally, if the alloy doesn’t melt at the right temperature, you won’t be able to create the adhesive.
Here are some questions you should ask yourself when choosing your braze alloy:
- How do the elements in the alloy interact with the elements in my metals?
- How strong of a bond do I need?
- What is the alloy’s melting point, and is it lower than the base metal?
- How wide is the gap between the two pieces?
- Do I need any other special qualities, such as electrical conductivity?
Carefully considering all of these questions and being even more careful when choosing your brazing alloy will prevent many problems.
Improper Fluxing
Besides a filler metal and braze torch for brazing, you will also need a flux material. Flux is a chemical that you have to apply to metals before brazing. It prevents oxidation, which is common when you heat metals. Oxidation prevents your braze from bonding properly, which is why flux is so important.
However, trying to cut corners during fluxing can lead to problems down the line. Make sure you use the right flux material and heat for the materials you are working with. Also, ensure that your flux’s quality is top-notch and you are not using a watery or dried-out material. When in doubt, it’s better to open a new can than to use old flux that’s been lying open for a while.
Improper Joint Thickness
When you’re joining two metals together, the joint should have the right thickness to hold up to wear and tear. A joint that is too thin will not be stable. A joint that is too thick will look ugly and also will be unstable.
Make sure the joint is the same thickness throughout. Otherwise, it looks bad and creates more opportunities for gas to get trapped in the joint.
Gas Entrapment
Gas entrapment is a serious problem during brazing. Your braze torch uses gas to provide heat. If the gas gets trapped in the joint or in the metal, it undermines the stability of your joint. It could cause bubbles or cavities in the metals you work with.
Luckily, there are a few ways to prevent gas entrapment. One important way is to flux properly, as improper fluxing is often why gas gets entrapped.
Overheated Tungsten Carbide
Tungsten carbide is one of the strongest metal compounds out there. However, it requires delicacy when you are working with it. If it overheats while you are brazing, it will not join properly. Experts recommend bringing all materials up to temperature together and heating the tungsten carbide slightly longer. This is called a slow draw. Since tungsten carbide is such an expensive material, you want to make sure you are working with it properly.
Final Thoughts
There are many advantages to using brazing. It provides a very secure joint, just as strong as welding. It is a strong welding alternative that requires less equipment. However, brazing is also an important skill to master. Making a mistake during the process could make the joint less stable, causing headaches in the future.
These are some of the most common brazing problems you should prepare for. A little preparation and knowing the materials you are working with go a long way to preventing most of these issues. It’s also important to clean the materials, including the plate and tip.