Welding fuses base metals by melting them; brazing joins metals using a filler metal above 840°F (450°C) without melting the base; soldering is similar to brazing but uses a filler metal below 840°F (450°C). Welding provides stronger joints, while brazing and soldering are suited for delicate or dissimilar materials.
Whether you are a seasoned professional, an HVAC technician, or simply curious about a different kind of metal joining technologies, you should find this article helpful.
The more popular metal joining processes come to the forefront when considering the category of metal joining in its broader sense – welding, brazing, and soldering.
When studying each of these three processes, questions begin to form around how the different processes compare and contrast with each other.
Table of Contents
What is Welding?
The material joining process known as welding has multiple variations. Each with its own attributes. Variations of unique welding processes
- Shielded metal arc
- Gas tungsten arc
- Gas metal arc
- Resistance
- Flux core welding
For the many variations of welding, the fundamental definition of welding is that two similar metals become joined together while melting the base materials. This is accomplished by using high heat and typically using a filler material.
What does the Welding process looks like?
- Welding is typically achieved using an electrical arc between the electrode and the workpiece(s). This electrical arc can reach the high temperatures required to melt even the thickest base metals.
- The electrical arc interaction between the electrode and the base material, known as polarity, can be such that the electrode is positive and the base material is negative. Or, the electrode can be negative and the base material positive. Thirdly, the polarity can rapidly alternate as in alternating current (AC).
- The electrical arc creates a puddle of molten material. The operator skillfully moves the puddle along the weld joint and typically adds filler material.
- This weld puddle of molten metal requires shielding from the natural atmosphere to prevent impurities in the resulting weld bead. Weld shielding depends on the process chosen. But, can consist of either a shielding gas or a flux which gets melted and surrounds the puddle to protect it.
- The resulting weld in any processing variations becomes stronger than the workpiece material.
NOTE: Welding is an extremely durable and permanent way of joining metals together.
What is Brazing?
Brazing is the process in which two metals, which can be dissimilar, are joined together by melting a filler material into the joint between the base materials.
The metal joining process called brazing is not as well-known as welding or soldering. Nonetheless, it is a commonly used process due to its flexibility in various applications.
The filler material needs to melt above 842 degrees Fahrenheit. This temperature is standardized by the American Welding Society (AWS).
- The brazing process can be applied to joints through a torch, induction, or oven to get the filler material hot enough to melt. Thus, properly filling the gaps in the joint.
- When the filler material fills the gaps in the joint it is called a capillary action. As with welding, the filler material must be protected from the natural atmosphere when it becomes molten. Again, this is achieved through the use of flux materials.
- The filler rod is like a piece of flexible wire. The rod, or wire, is shaped to match the braze joint. It is then set directly on top of the joint.
- Flux for brazing applications typically comes in a paste. The paste is brushed on the joint before the brazing operation. The production advantage with brazing is that the brazing operator can cut a “braze ring” consisting of a length of filler material.
- After the operator has laid these braze rings on the joints of the workpieces, he applies flux to the joints. They are then placed into a high-temperature oven. The heat is set to the temperature capable of melting the filler.
The brazing filler material typically melts at approximately 1,150 degrees Fahrenheit.
NOTE: It is important to know that the temperature necessary to melt the braze filler material does not actually melt the base materials. Despite that, it can affect the hardness of the base materials.
The brazing process results in a high-strength joint that can be relied upon for many production applications. The exception is structural applications.

What is Soldering?
Soldering is joining two dissimilar metals together by melting a low-temperature filler material between the base materials.
The last process in these three metal joining processes is soldering. This is possibly the most widely and commonly used of the three processes.
The temperature that the American Welding Society (AWS) defines the threshold between brazing and welding is 842 degrees Fahrenheit.
This means that all soldering operations occur under this temperature limit.
The technique of soldering is quite user-friendly. And, due to the low-temperature properties of the process, soldering can be achieved without the setup required for the more involved, hotter, metal joining processes.
- Soldering operations can use a torch, a soldering “iron,” or an oven to melt the filler material properly.
- Like welding and brazing, soldering requires a shielding material to protect the molten filler material from the natural atmosphere.
- The gases in the atmosphere can contaminate the solder joint and cause failure. The shielding material used in soldering operations is typically a flux paste.
- The paste is typically brushed over the joint but can come as a rosin. In electronics applications, rosin can be in the core of the filler material wire itself.
- Soldering filler materials typically melt at around 400 degrees Fahrenheit. W
hich is acceptable for joining delicate electronics components together.

Differences between Welding, Brazing, and Soldering?
Now that we have become somewhat familiar with the metal joining processes of welding, brazing, and soldering, we can now explore main differences in depth.
As previously mentioned, we will look at four categories when comparing these three processes.
The four categories are the:
- Type of materials being joined
- Types of filler materials used
- Application and process tolerances
- Amount of heat applied to the base materials.
Type of Materials Being Joined
The types of materials joined in these three processes are unique to each welding, brazing, and soldering process.
Welding
The welding process can permanently join almost any metal in a durable joint.
Welding technicians very regularly weld together carbon steels, stainless steels, aluminum, as well as specialty alloys such as coppers and high nickel content alloys.
Not as commonly welded together are castings, forgings, and extrusions. But there are welding techniques to achieve these types of joints.
The welding process is so highly durable that it is used to join super-thick structural steel plates. The process is so versatile that it can join together materials as thin as an aluminum soda can.
Brazing
The types of materials which the process of brazing can join together are numerous.
The brazing process can join together the same metals as welding. Metals such as steel, stainless steel, aluminum, and exotic alloys. Albeit with less strength.
But the main advantage which the brazing process has over the welding process is the ability to join dissimilar metals together.
As hard as you may try, you cannot weld together dissimilar metals such as steel and an aluminum tube. The materials won’t melt together and form a joint.
Certain filler materials are determined to be best for different material combinations. The brazing operator will look up these specifications as called out by an engineer.
The brazing process can join together thick and thin materials. But it does not have the penetration qualities which the welding process has in order to permanently join thick pieces of material together.
Soldering
The types of materials that the soldering process can join are limited to the low-temperature qualities of the process.
Process engineers save soldering operations for smaller workpieces such as joining together wires and thin pieces of material.
The soldering process regularly joins copper, aluminum, and steel materials. However, it is limited by the workpiece thickness. Like the brazing process, the soldering process can join dissimilar metals.
This is due to the metals not actually melting together to become joined as in welding. Instead, the filler material acts as a kind of “metal glue” so to speak.
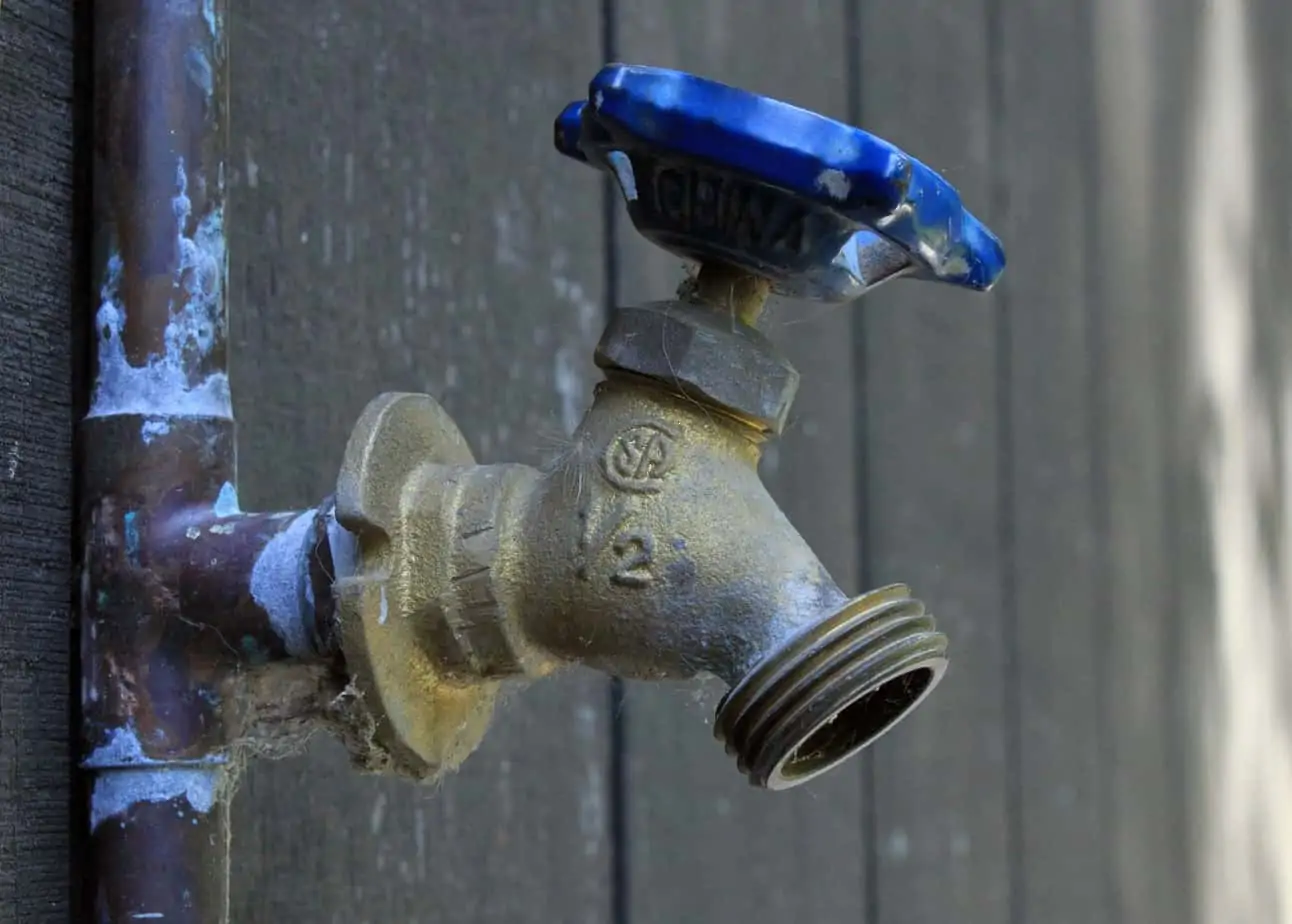
Types of Filler Materials Used
The types of filler materials used in each of the three processes we are exploring, welding, brazing, and soldering are unique to each of their respective processes.
The main reason why the filler materials are unique to their processes is mainly due to their chemical composition. Their composition is directly related to the filler material melting points.
6 Tips to choose correct filler material:
- Shielded Metal Arc Welding (Stick) and Gas Metal Arc Welding (MIG) are unique because the filler material is the actual electrode.
- All other
metal joining processes (with the exception of TIG fusion welding) use a filler material to add to the joint. - Welding processes require the filler material to be very similar to the workpiece material being joined together.
- There is an allowance in welding processes for the filler material to be of a slightly different alloy than the workpiece, but generally, steel requires steel filler, and aluminum requires aluminum filler.
- In contrast, the brazing and soldering processes break this rule and use dissimilar filler materials from the workpiece. In fact, brazing and soldering need to use dissimilar metals to the workpiece. Since, for example, the heat required to melt copper exceeds the brazing and soldering temperature limit, by definition.
- Brazing and soldering processes use lower temperature melting filler alloys, typically alloys of tin.
NOTE: Brazing and soldering processes previously employed lead-based filler materials due to the low melting temperature and ease of use. But filler material manufacturers have changed to lead-free alternatives due to governmental regulations on the usage of lead.
Application and Process Tolerances
Applications of welding, brazing and soldering processes can seemingly be infinite. But for this article, we will focus on finite examples to help illustrate the differences between these three processes.
Popular welding applications include joining structural, automotive, marine, and aerospace parts. The welding process is called for when joining together of metals needs to be permanent and safe.
Welding together airplane components, for example, requires extreme process tolerances. These include the weld’s size, the weld, the quality of the weld, and the weld materials themselves.
This is so that the resulting weld can be certified safe for flight critical applications. Welds that are utilized in these critical applications are required to be scrutinized by welding inspectors.
Inspection Tools
Inspectors will use inspection tools such as:
- Magnetic particle inspection
- Fluorescent penetrant inspection
- X-ray inspection
- Destructive testing
These tools and others qualify the weld as falling within specification. Which ultimately ensures a safe part is being installed on the airplane.
In contrast, brazing and soldering processes can also carry strict process tolerances. Just not usually in the same structural flight critical applications.
Brazing applications can be found in the aerospace, marine, medical, and oil industries. This, in part, is due to the ability for the process to be tightly controlled. Even tighter than in welding.
Since brazing does not include melting the base materials, there is less risk of part warpage, part contamination, and dimensional issues. Brazed assemblies can achieve tighter tolerances because of these facts.
Soldering is most commonly found in the plumbing, electronics, and HVAC industries. The most common soldering joints are the lap joint. These are found in almost every house.
Examples of soldered lap joints in your home are between copper pipes, and the joint between wires and circuit boards – literally used in every electronic device on the planet.
Soldering applications are found in so many consumer and industrial products that soldering processes are the most used between welding, brazing, and soldering.
Amount of Heat Applied to the Base Materials
The last area we will explore in the study of the differences between welding, brazing, and soldering is the amount of heat applied to the base materials in each process.
The amount of heat required to achieve a weld joint is variable. The welding process is defined as melting the base materials to form the weld joint. For some metals
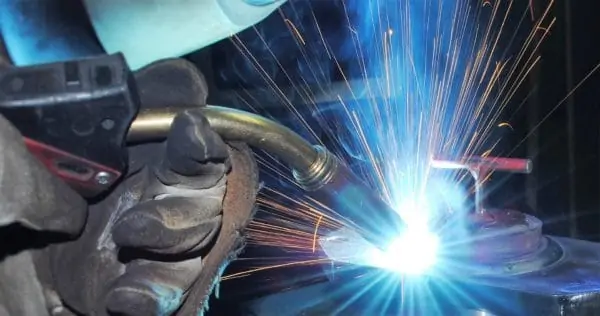
For instance, the arc in the arc welding process can be up to 20,000 degrees Fahrenheit. The workpiece itself can regularly reach over 1,000 degrees Fahrenheit.
Obviously, these high temperatures can be very dangerous to be around. The welding operator must diligently use all personal protective equipment the OSHA standards call for.
Different metals act differently during welding operations. Stainless steels weld “like butter” with a constant weld puddle which is relatively easy to work with.
In contrast, aluminum materials have a much higher melting temperature and require special welding machinery.
Once the extra-high melting point of the aluminum is reached and the weld puddle is formed, the welding operator must work very quickly. If he fails to work quickly enough the entire aluminum workpiece can melt, distort, and become problematic.
Brazing and soldering processes do not have to reach the high temperatures that welding does. The only requirement in the process is to melt the filler material to obtain the joint.
Remember, brazing operations reach higher temperatures than soldering. Brazing temperatures are defined as being above 842 degrees Fahrenheit. Soldering is defined as being under 842 degrees Fahrenheit.
Low melting temperature solder filler materials can have special alloys in them which can lower the typical melting point of 430 degrees down to approximately 290 degrees Fahrenheit.
These ultra-low melting temperature solders can be used in the most delicate electronics applications since the objective is to prevent damage to the sensitive electronic components.
Conclusion
By exploring the unique qualities of each process, we have found the many differences between welding, brazing, and soldering.
These differences were summed up in the categories:
- Type of materials being joined
- Types of filler materials used
- Application and process tolerances
- Amount of heat applied to the base materials
As we have found, each of the welding, brazing and soldering processes have their own unique purposes and applications. And each one is very important to the industries which utilize them.
Welded, brazed, and soldered parts can be found everywhere in our world today – look around in the room you are in and you are likely to find a dozen examples.
If you would like to learn more about any of these three processes, please use the resources at your disposal, which are quite easily found either online, at your local library, or our favorite, from seasoned welding, brazing, or soldering technician. That one is willing to share some of his or her experience with you.