Selecting the polarity and amperage depends on the type of welding process, the base metal, and the welding electrode. This controls the amount of electricity flowing per second and determines the level of penetration and the quality of the welding bead.
Understanding all of the dials and digital readouts on the welding machine can be intimidating. The few controls on a stick welding machine are going to be simpler than on a TIG machine. A top end TIG machine could have as many as 20 control knobs for various settings.
Stick welders, MIG welders, and TIG welders all have various controls on the front of the machine. These are to adjust the level of current needed for a weld.
But how do you know what welding amperage or voltage setting to set the machine to?
Setting the amperage on a welding machine, whether Stick (SMAW), MIG (GMAW)(*typically uses voltage setting), or TIG (GTAW), depends on some key variables such as application and base material, welding process, and electrode.
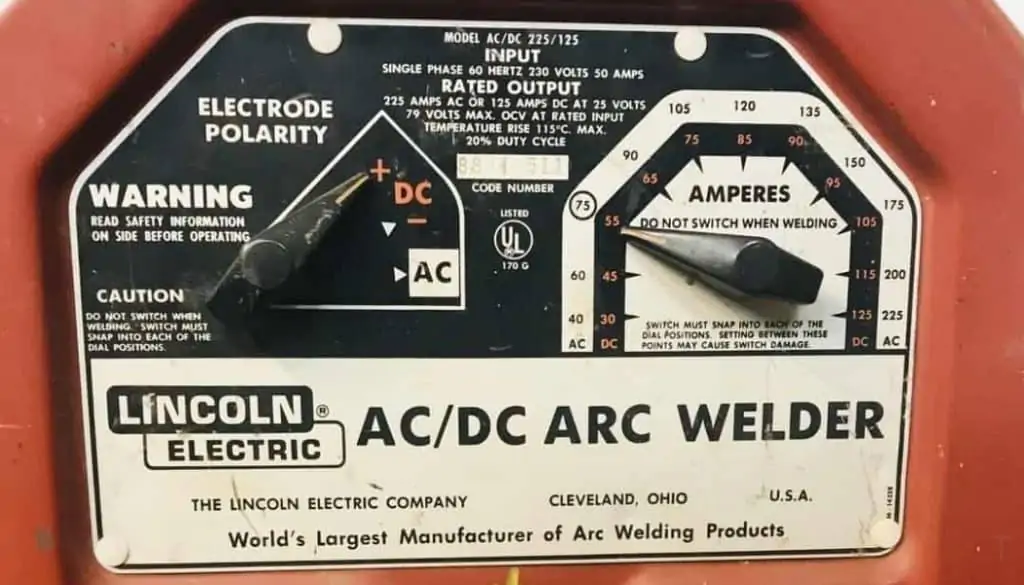
Once you determine these three main variables, you can set your welding machine and start laying a weld bead. In this article, we will discuss these three variables in depth, and also provide some “pro tips” along the way!
Table of Contents
Welding Application and Base Material
In this section, we will discuss the welding application, the base material, and specifically how this applies to the amperage selection on a welding machine.
Welding Application
Welding application has a direct correlation with the amperage used in a weld.
Micro TIG welding and laser beam welding have similar applications where in the case of TIG welding the amperage is quite low. However, in the case of laser welding, there is no amperage at all since there is no electrical current flow within the workpiece. In contrast, MIG welding and Stick welding (and sometimes TIG welding) can use very high amperage settings in order to achieve optimal penetration into the workpiece.
For example; A highly technical TIG weld on a helicopter exhaust manifold will have a drastically different amperage needed than for say, an oil pipeline. The difference will be between welding thinner exotic metals and welding a three-foot diameter pipe to the next pipe in sequence.
In some applications, amperage is selected for convenience. For example, you might want to MIG weld a sheet of metal to another sheet of metal in your workshop, so you might be inclined to turn up your amperage to get the weld bead laid down as quickly as possible.
This is not to say rushing through a weld is a good practice but speeding up a weld bead in a non-critical application is very common.
PRO TIP: If you are interested in seeing all sorts of welding applications in one place, you should either get a tour at a shipyard, a fabrication shop, or your local technical or vocational school. Chances are, you might see a specific welding application which interests you and you might want to explore that application further in a career-oriented sense.
Base Material
The category of base material is quite broad. Therefore, we will focus on two main areas in the category of base material. And those are Type, and Thickness.
Both of these areas have a very strong correlation with what amperage setting needs to be used on the welding machine.
How type of material can affect amperage selection?
The type of material used in different welding applications can vary widely from weld to weld, jobsite to jobsite, or even from welding technology to welding technology.
Before even thinking of what amperage to set your welding machine to, you should ask yourself what type of metal you will be welding.
The main material types which standard welding methodologies can weld together are carbon steel, stainless steel, and aluminum. All three of these material types require different amperage selections on their respective welding machines. The most notable difference is between the ferrous and the non-ferrous materials, i.e. steel versus aluminum.
Certain materials require higher or lower amperage settings based on the raw material melting point. This is very apparent when looking at aluminum materials. Primarily since
Amperage selection when welding Aluminium
When welding aluminum materials together, the current usually has to be switched from DC (direct current) over to AC (alternating current). In addition, the amperage must be turned up to compensate for the higher melting temperature of aluminum.
TIG welding aluminum is unique in that the current utilized is AC due to its cleaning characteristics. This is achieved due to the weld current alternating from one direction to the other.
Once the arc is struck in an aluminum TIG weld bead and the weld puddle is formed, the operator must move the bead relatively quickly. This is due to the aluminum base material tending “soaking up” the high amperage heat and potentially warping the base metals.
Stick Welding amperage for different steel thicknesses
The adjustments to Stick welding amperage to compensate for steel material thickness are similar to the processes necessary to compensate for material thickness with a MIG welder.
Stick welders have a simple control knob on the front of the machine which adjusts the amperage level with the twist of your wrist. In the same way, MIG welders have that same
PRO TIP: If you are not sure what amperage to use with a certain piece of material, whether thick or thin, aluminum or steel, it is always a good idea to practice a weld bead on a scrap piece of material similar to the final metal workpiece you intend to weld. This small amount of time practicing will save your hours of time grinding out your weld after you find out that your weld does not have a correct amount of penetration for the thickness of material you are welding.
Stick Welding: Switching from a thin workpiece to a thick workpiece
The welding technology which has the most noticeable changeovers when switching from a thin workpiece to a thick workpiece is stick welding.
Stick welding is different from MIG and TIG welding in that the welding operator must select a different electrode that best suits the workpiece thickness. The same electrode which works well for a thin piece of steel would not be as useful when welding a thicker piece of steel. This is because a thicker piece of steel requires more penetration and a wider root to the weld.
A thinner electrode would not be up to the task – it would simply be consumed too fast.
Welding Process and Amperage Selection
The welding processes which we will explore in the context of amperage selection are these three main processes: TIG (Gas Tungsten Arc Welding, or GTAW), MIG (Gas Metal Arc Welding, or GMAW), and Stick (Shielded Metal Arc Welding, or SMAW).
There are other welding technologies which can be discussed in the context of amperage selection. But these three welding technologies are the most commonly used for beginners.
TIG Welding
TIG welding in general is reserved for those welders who have the greatest hand eye coordination because most TIG welders require hand, eye, and foot coordination – almost like driving a car!
The unique characteristic of TIG welding when it comes to amperage is that the foot pedal on the TIG welding machine controls the amperage needed in the weld per the user’s input.
The foot pedal starts at 0 amps in the resting state and gradually increases in amperage as the welding operator pushes the foot pedal down to a certain limit. The limit of the amperage control on the foot pedal is limited by the TIG welding machine’s amperage capabilities and/or the setting on the machine.
Some TIG welding machines have this “Peak Amperage” feature on the control panel which should be set to approximately 40-50% above your desired amperage range to be used in the weld.
Some TIG welders have other amperage control features such as background amperage or fine adjustments to the amperage when using AC current. But those adjustments are outside of the scope of this article.
Metal Thickness (inches) | Electrode Size (inches) | Amperage Range |
---|---|---|
0.020 | 1/16 | 20-50 |
0.040 | 1/16 | 30-75 |
0.060 | 1/16 | 50-100 |
0.090 | 3/32 | 80-130 |
0.125 | 3/32 | 100-160 |
0.1875 | 1/8 | 140-220 |
0.250 | 1/8 | 180-280 |
0.3125 | 5/32 | 220-340 |
0.375 | 5/32 | 250-400 |
0.500 | 3/16 | 330-500 |
MIG Welding
For the purposes of this article, we will use the variable voltage settings in lieu of the amperage settings which other welding technologies use more commonly.

The voltage settings on a standard MIG welder determine the power used during the MIG welding operation. There is always a necessary balance between voltage and wire feed speed. Especially since the wire feed speed needs to increase as the voltage also increases or else the weld puddle will not be adequately fed with filler material.
For thin
PRO TIP: All MIG welders are different, and all welding applications are different. Once you find your optimal weld setting for your MIG welder (for your specific application, write this down on a paper and attach it to the side of your welder. This will save you from the headache which happens when another operator uses your machine, or the machine gets bumped and your settings are lost.
Metal Thickness (inches) | Wire Size (inches) | Amperage Range |
---|---|---|
0.030 | 0.023 | 30-90 |
0.060 | 0.023 | 50-120 |
0.090 | 0.023 | 90-160 |
0.125 | 0.030 | 120-200 |
0.1875 | 0.030 | 150-250 |
0.250 | 0.035 | 200-300 |
0.3125 | 0.035 | 250-350 |
0.375 | 0.045 | 300-400 |
0.500 | 0.045 | 350-450 |
Stick Welding
Stick welding, as mentioned earlier, has the most significant correlation between weld application and weld amperage.
A stick welding operator could use one amperage setting one day while he or she is welding a plate of steel for a structure, then use a different setting another day while he or she is surface welding a backhoe bucket.
The good news about stick welding is that there are charts that can be easily found online that are usually very good at predicting the amperage needed for a certain welding thickness and accompanying stick welding electrode.
If you follow the amperage levels shown on one of these charts, you should be in good shape. If you need to make minute adjustments to the heat of the weld while “under the hood” during your stick weld, the easiest way to achieve this is to pull the welding rod away from the weld puddle to “long-arc” slightly. This will achieve a wider and hotter puddle.
This table gives you a starting point of the correct stick welding parameters for your electrode type and size:
Electrode Diameter (inch) | 6010/6011 | 6012 | 6013 | 6020 | 6027 | 7014 | 7015/7016 | 7018 | 7024/7028 |
1/16 | – | 20-40 | 20-40 | – | – | – | – | – | – |
5/64 | – | 25-60 | 25-60 | – | – | – | – | – | – |
3/32 | 40-80 | 35-80 | 45-90 | – | – | 80-125 | 65-110 | 70-100 | 100-145 |
1/8 | 75-125 | 80-140 | 80-130 | 100-150 | 125-185 | 110-160 | 100-150 | 115-165 | 140-190 |
5/32 | 110-170 | 1109-190 | 105-180 | 130-190 | 160-240 | 150-210 | 140-220 | 150-220 | 180-250 |
3/16 | 140-215 | 140-240 | 150-230 | 175-250 | 210-300 | 200-275 | 180-255 | 200-275 | 230-305 |
7/32 | 170-250 | 200-320 | 210-300 | 225-310 | 250-350 | 260-340 | 240-320 | 260-340 | 275-365 |
1/4 | 210-320 | 250-400 | 250-350 | 275-375 | 300-420 | 330-415 | 300-390 | 315-400 | 335-430 |
5/16 | 275-425 | 300-500 | 320-430 | 340-450 | 375-475 | 390-500 | 375-475 | 375-475 | 400-525 |
PRO TIP: A good rule of thumb for setting your stick welder (SMAW) to the approximate right setting to start off with is the amperage setting should be about the same as the decimal equivalent of the rod diameter. For example, 3/32” rod diameter would be (.094) 90 amps, 1/8” rod diameter would be (.125) 125 amps, 5/32” rod diameter would be (.157) 155 amps. This rule of thumb works for most electrode sizes, and once you get your arc started and your first weld bead on your part, you can adjust the settings from there.
The Electrode
The only welding process that significantly correlates electrode and amperage is Stick welding or SMAW. This type of stick welding and amperage are so dependent on each other in this category, which is why this topic made it into the top three amperage selection factors.
TIG welding and MIG welding processes do use electrodes by definition, but TIG uses a semi-consumable tungsten rod and MIG welding uses a highly consumable wire, both of which have little significance when talking about amperage selection.
There are many types of electrodes available for stick welding, and each has their specific use. For example, electrodes differ due to the
They also differ due to horizontal, vertical, or overhead positions. These different properties are captured in the four to the six-digit number printed on every stick electrode for easy reference.
These numbers tell the user which power supply, weld position, tensile strength, and penetration that electrode was designed for.
The most common electrodes on the market are 6010, 6013, and 7018. These three electrodes are very common in the industry due to their incredible flexibility in applications.
How to choose the correct Electrode and Amperage?
The 6010 electrode is designed to penetrate deeply into the workpiece, whereas the 6013 electrode is designed to penetrate less. For the best appearance of a weld, a welding operator should select a 7018 weld electrode.
Once you have selected your stick welding electrode, you should read the side of the electrode container to see what the electrode manufacturer recommends for the welding amperage. The specific amperage to be used depends primarily on the diameter of the electrode.
For example, an eighth in diameter electrode welds great between 75 and 125 amps. Whereas a 5/32 diameter electrode can weld optimally at up to 220 amps.
The best way to know what the optimal amperage you should use is to test the welding electrode on a scrap piece of metal and observe the resulting weld. If it has an acceptable appearance and penetration rate, then run with it.
An important consideration when adjusting the amperage on your stick welding machine is the welding machine manufacturer’s recommended duty cycle for the machine.
Duty cycle is defined as the length of time the welding machine can be welding during a 10-minute period of time. Some machines are more heavy duty than others.
For example, a machine used at a construction site will most likely have heavier duty components and a longer duty cycle than a hobby welder in someone’s garage.
Duty cycle is inversely proportional to welding amperage. That is, as the amperage increases, the duty cycle length in minutes, decreases.
PRO TIP: Looking for a solution to resolve the scenario when you have an electrode with a bunch of the flux chipped off for whatever reason? If you are welding on the job where the weld needs to conform to certain requirements, using a chipped electrode is out of the question. Once way which experienced welders salvage chipped electrodes is by having a 6” x 6” steel plate nearby where they can quickly lay down a bead of weld, using up the area of electrode which is problematic, then resume their actual weld bead once the electrode is back to a section with good flux.
Conclusion
Amperage selection is not as confusing and intimidating as you might think.
There are certain key variables which determine the amperage which should be used in a certain welding application, such as Application and Base Material, Welding Process, and Electrode.
With these main variables in mind, finding the correct amperage necessary for your weld should be no problem. As always, if you are still unsure, there are numerous resources at your disposal, whether online, at a library or my favorite, in your local welding store.