MIG Welding is better for beginners because it is simpler and easier than TIG welding, which requires using both hands and feet to operate properly.
We’re going to talk about the similarities and differences of mig welding vs tig welding. I will do my best to compare the two processes from different angles, including speed, quality history and equipment cost.
This way you can get a pretty good idea which is the best option for your particular needs.
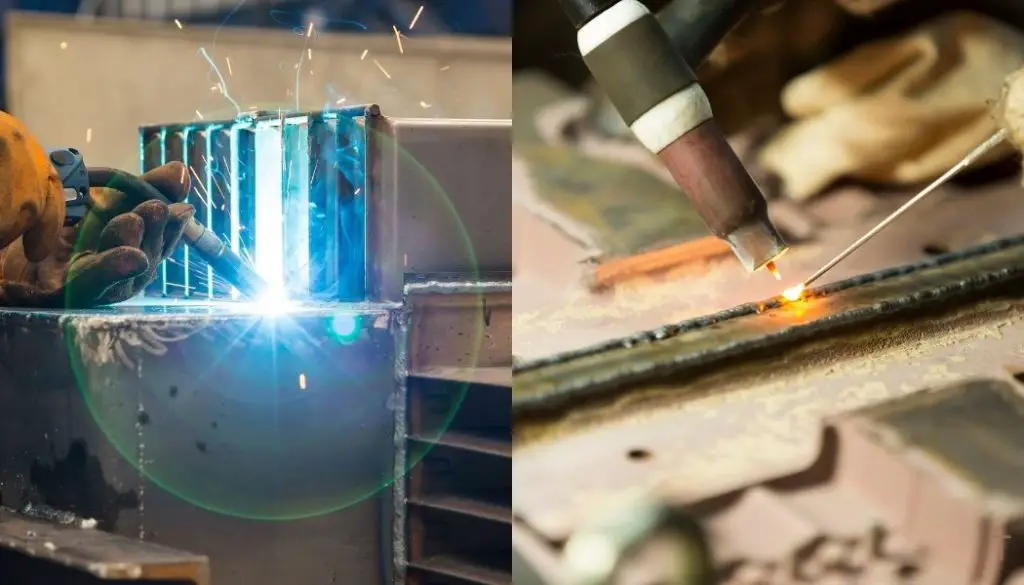
Table of Contents
MIG vs TIG Welding – The Basics
Seeing a near-perfect TIG weld on a finished product is always striking. It looks like a stack of dimes. The evenness and accuracy of the weld bead is an indicator of the skill level of the welder. Nevertheless, a near-perfect MIG weld on a consumer product such as a truck frame shows the efficiency and strength which can be achieved with MIG welding.
MIG and TIG welding are two of the most common types of welding across many industries. The use of both Metal Inert Gas (MIG) and Tungsten Inert Gas (TIG), can be found in industries including the automotive, marine, nuclear, aerospace, and oil industries.
It is helpful to understand the basics of both MIG and TIG welding. The more you grasp the better you can choose the technology which best suits your application. The first step in understanding their definitions, similarities, differences, and histories.
What is MIG Welding?
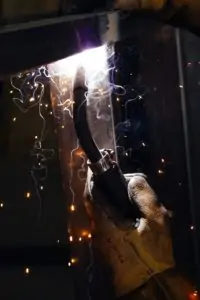
Mig Welding is a type of welding process in which the welding arc occurs between a consumable wire and the workpiece. The welding arc melts the consumable wire, which is continually fed through the handle controlled with a trigger.
The consumable wire is fed into the weld pool and can build up the weld to the required specification based on the machine setting and the user’s technique.
NOTE: Use a shielding gas in order to achieve a clean weld. The most common shielding gas for MIG welding are argon and carbon dioxide.
What is TIG Welding?
TIG welding is a type of welding process in which the welding arc occurs between a tungsten electrode and the workpiece. The tungsten electrode is held in a collet inside of the welding torch. You need to hold the tungsten electrode about an eighth of an inch away from the workpiece. This will keep the arc constantly forming the weld puddle. You can weld with or without a consumable filler rod manually dipped into the weld puddle.
Because the procedure is manually regulated, skill and technique are essential for a visually acceptable TIG weld bead. Fusion TIG welding, on the other hand, does not require any filler and is simply a method of waving the torch back and forth over the workpieces to be welded.
Filler rod welding requires pulsing the foot pedal while dipping the filler rod into the weld puddle with one hand while holding the flame with the other. The operator’s foot, hands, and eyes must perfectly sync for this technique to work.
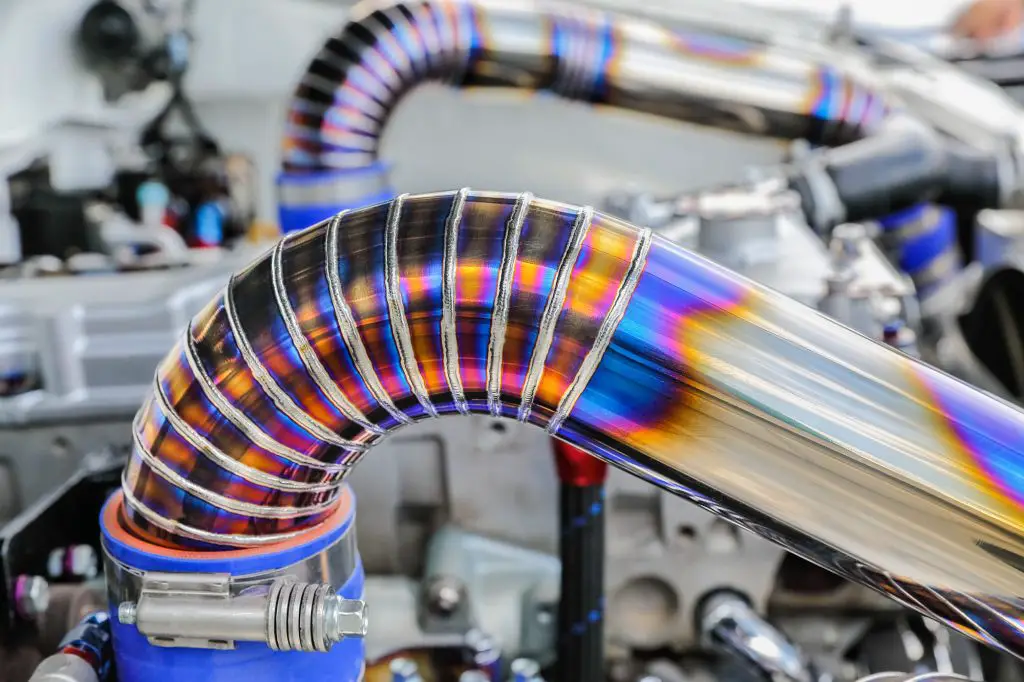
MIG and TIG Similarities
There are many similarities between the MIG and TIG welding processes. A few of the main similarities are welding current, welding material deposition, heat-affected zone, and applications.
1. Current
The electrical current used for both MIG and TIG welding can both be DC current, electrode negative. TIG can use AC current in order to achieve an optimal weld puddle in aluminum.
With MIG welding, the current passes through the welding wire and arcs between the wire and the workpiece. Similarly, with TIG welding, the electrical current passes through the tungsten electrode and arcs from the electrode to the workpiece.
2. Welding Material Deposition
The foundations of MIG and TIG welding are the same as in conventional welding. That is, the formation of an electrical arc that generates a great deal of heat. As a result, a controlled puddle of liquid metal is formed, which is then utilized to link metals together.
Both MIG and TIG welding may utilize a filler material in order to build up the weld bead. The filler improves the strength of a joint.
Filler material is used in MIG welding by automatically feeding the consumable wire into the weld puddle. In TIG welding you use filler rod to help build up the weld.
3. The Heat Affected Zone
This is defined as the region of the workpiece which is affected by the high-temperature welding process. The heat affected zone can be similar between the MIG and TIG processes. Advanced TIG techniques such as micro welding are the exceptions.
Design engineers may call for a specific heat affected zone in order to minimize material fatigue in critical applications. The way a welding operator controls the heat affected zone during the MIG process is by pulsing the MIG handle. This effectively starts and stops the weld bead. This pulsing technique is commonly used in the automotive repair industry to stitch weld sheet metal panels on vehicles.
Since the TIG welding process is much more controllable, it is more suited to controlling the heat affected zone. The operator simply adjusts the intensity of the arc through the foot pedal connected to the welder.
Some of the common applications which MIG and TIG welding share include automotive sheet metal repair, automotive racing components, pipe fitting, and some structural work.
MIG and TIG Differences
While MIG and TIG welding share many similarities, there are also some important differences. These include shielding gasses, the speed of welding application, automation, and precision.
1. Shielding Gas
Shielding gasses are needed for MIG and TIG welding, but the types of gas used vary. The shielding gas protects the weld puddle from the natural atmosphere. The air around us can contaminate the weld due to the air’s oxygen, hydrogen, and nitrogen.
Sometimes shielding gasses are so important for weld purity that the weld is performed inside of an enclosed inert gas atmosphere. When welding titanium this is highly recommended.
What Shielding Gas should you use for MIG Welding?
Standard MIG welding applications call for CO2 gas. And since the gas occurs in abundance, it is the most economical and common choice for MIG welding. Shielding gasses less commonly used in MIG welding are helium, argon, and oxygen. These are reserved for specialty metals and aluminum.
What Shielding Gas should you use for TIG Welding?
TIG welding almost always uses 100 percent argon gas to shield the weld puddle. A helium and argon mixture is used in some cases, such as when welding high nickel content metals. This is the origin of the old-school term, heli-arc welding. Less commonly used are mixtures of argon and hydrogen or nitrogen. These are reserved for TIG welding certain stainless steels.
2. High Quality or High Speed?
Another difference between MIG and TIG welding is the speed at which the weld can be applied. Where TIG welding requires a continual manual application of welding rod, a MIG welder can lay down a weld bead at a rapid speed.
A highly skilled TIG welder can create a weld bead at a fast pace. But rarely can a TIG welder beat the faster MIG welding application. Due mainly to the manual nature of the TIG welding process.
Since the MIG process can create a weld quickly and consistently, the process is commonly used in automated welding processes. The automation of the MIG welding process sits in contrast to the high precision, manual, TIG welding process.
NOTE: TIG welding can be advantageous in highly critical applications where precision is required. Such as in a helicopter engine or in a space shuttle exhaust.
History of the Technologies
MIG welding technology advancements resulted from the demand for goods during the Post-War era. Factories were able to produce the high quantities of automobiles, ships, and buildings, which were called for after World War II. Thanks in part to the advancement of the MIG welding technology. The development of using CO2 as a shielding gas in the 1950’s made MIG welding the preferred welding process.
In the late 1950’s flux core welding was introduced into the market as an alternative to the increasingly popular MIG welding technology. Flux core welding uses a tubular welding wire with a flux material inside of the wire. This comes in handy when shielding gas is not readily available. Since flux core welding does not produce as clean of a weld it is not as favorable as MIG.
TIG welding officially became a welding process in the 1940’s. It was originally named “Heli-arc” due to the shielding gas used for the process at the time, helium. Originally, the process was DC Electrode Positive. However, subsequent technological advances reversed the current so that DC Electrode Negative (DCEN) was possible.
Although DCEN produced cleaner welds in ferrous materials, non-ferrous materials were quite challenging to weld. That is until the advent of TIG welding with AC current emerged. The final significant advancement came in the form of the high-frequency arc starter.
NOTE: Now the operator does not need to strike the tungsten electrode against the workpiece to start the arc. This would frequently contaminate the weld or damage the electrode.
Applications and Equipment for MIG and TIG Welding
MIG and TIG welders are commonly available for both households and for industrial applications. There are some unique differences between the welding applications in a household versus an industrial job site.
Some examples of a household application would be related to fixing items such as a backyard fence, a broken lawn care tool, or perhaps a broken truck bumper mount.
In contrast to the household applications, industrial applications can span between shipyards, aviation or automobile factories, aviation or automobile repair shops, mine sites, nuclear facilities, building structures, or oil fields.
All of these industrial applications demand much more from a welder than a household application could ever demand. Whereas a household application demands economy and ease of use from a welder, industrial applications demand durability, long duty cycles, and a final weld bead which can be inspected under scrutiny. This is understandable since human lives could literally depend on the weld quality.

Household MIG and TIG Welding Equipment
The household user and the hobbyist welder generally require different welding features than an industrial worker would require for their welding application.
As household user you will typically be interested in features on a welder such as an easy to use user interface and Having the capability to use household electrical current.
A commonly purchased welder for the household user or hobbyist is a MIG welder with a bottle of CO2 shielding gas such as Lincoln MIG Pro 180.
This type of welder can achieve good, clean welds in various light duty applications. And, they can be purchased at an economical price point.
TIP: Check my review of the MIG Pro 180 by Lincoln Electric.
Industrial Applications and Equipment
Industrial applications can require MIG or TIG welders in various configurations. Heavy-duty MIG welders have features such as oversized MIG filler wire spools, longer duty cycle capabilities, heavy-duty components, and sometimes even a built-in generator to power itself. Industrial-grade welding equipment must withstand repeated use in harsh environments.
MIG Welders
MIG welders can be found in mining, pipe fitting, and steel erecting job sites. Mainly where conditions are not optimal and welders are used continually. In the instance of an earth moving job site, a welding outfit might be called in to perform a repair in the field on an earth mover.
This is a situation where time is money and the quickest way to make the repair is by using a welder with an integrated generator on a work truck. Alternatively, TIG welders can be found in nuclear, aerospace, marine, and automotive facilities where machines demand constant, continual use.
TIG Welders
The machines are often water-cooled for TIG welders to withstand the continual use of an industrial application. This is so they do not overheat and become damaged.
In marine applications where aluminum is the preferred material to use for weight and corrosion purposes, TIG welding (or MIG welding with the proper aluminum spool gun) is used to attach railings, deck plates, or hull reinforcements. Since TIG welding aluminum with AC current generates tremendous heat due to aluminum’s higher melting temperature, a water-cooled TIG torch is a must.
The Future of MIG and TIG Welding
According to an American Welding Society article called “Welding Forges into the Future,” the welding industry as a whole will only grow larger and stronger in the future due to the truth that welding is the optimal method of joining materials.
Slow, steady growth in the form of technological improvements will continue to emerge. Especially in aluminum welding category and potentially into the composites category.
Additional growth is believed to come from emerging markets experiencing industrial revolutions. In addition from the domestic market in the form of welding automation. The article further speculates and concludes that friction stir welding and laser beam welding will become more prevalent in the future.
Even though friction stir welding, a type of advanced metal joining being developed by NASA, and laser beam welding, which is typically used for joining sheet metals are undergoing continual advancements, the most widely used technologies will still be MIG and TIG welding.
MIG welding in recent years has seen improvements in automation. Automobile factories have continually been at the forefront of assembly line welding automation. Not only does the push for welding automation have the goal of profit margin improvement, but automation can also improve weld quality due to the fact that welding robots never become fatigued in the same way which human operators do.
The future of welding automation could include arc data monitoring. This is where, traditionally, a human welder could see issues with the weld puddle and make minor modifications to the weld parameters. In theory, robots could eventually do these minor adjustments in the future.
Conclusion
Now that you have more of an understanding of the MIG and TIG welding processes, go weld something! If you are reading this and are now interested in trying your hand at welding with either the MIG or TIG processes or perhaps others, then the next step is to try it out!
Read More
- Beginner tips when starting to weld
- The Best Welding Machine for Beginners
- Beginner Projects for New Welders
- What are the causes of welding spatter?
- 8 Tips for MIG Welding Beginners
- All About Weld on Barrel Hinges
- Do you push or pull flux core wire?
- Why Use a Welding Apron?
- How to select Welding Amperage?
- 7 Vertical Stick Welding Tips to Increase Weld Quality
- Which Metal is Best for welding artists?
- Spot vs MIG Welding
- MIG Welding Advantages And Disadvantages