To weld a vehicle frame, first clean and prepare the surfaces by removing paint, rust, and contaminants. Use appropriate jigs or fixtures to maintain alignment. Choose a suitable welding process, like MIG or TIG, and ensure proper penetration, heat control, and travel speed. Always follow safety protocols and manufacturer guidelines.
To weld on a vehicle frame is not hard but it brings up a multitude of questions including:
- Whether welding on a frame is legal?
- If welding on a frame can result in a strong product?
- And many more questions regarding best practices.
There are endless questions that can be asked about welding on a vehicle frame, but this article will address the top 5 questions ranging from the legality of welding on a vehicle frame to whether welding on a vehicle frame will harm the vehicle’s onboard computer.
While discussing the top 5 questions we will also provide some “Pro T
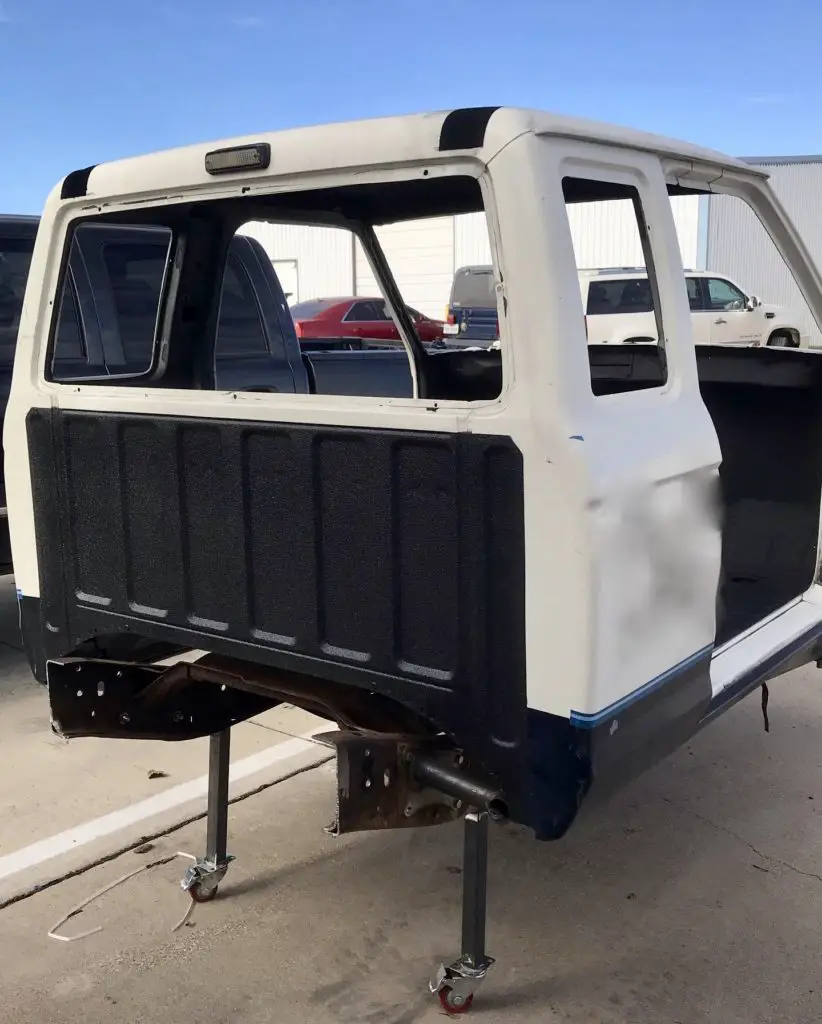
Table of Contents
Is It Illegal to Weld a Vehicle or Car Frame?
To discuss this question, we will break the question down into two subcategories:
- The legality of operating a vehicle on the highway with a welded frame
- The legality of selling a vehicle with a welded frame
First, a disclaimer regarding the answers provided in this “legality” section: This article only provides discussion on the topics of legality and does not provide legal advice in any way, explicitly or implicitly. You should consult a professional legal advisor when needing true legal advice on this subject.
Welding on any vehicle frame should be carefully performed using the proper preparation procedures, equipment and best practices.
Operating a commercial vehicle (bus, large truck, 18-wheeler, etc.) on a highway with a welded frame is not technically allowed per the Federal Motor Carrier Safety Administration Title 49: Subtitle B: Chapter III: Subchapter B: Part 393.201 (d), unless it is in accordance with the vehicle manufacturer’s recommendations (which is uncommon).
This is not surprising considering the strict regulations that are imposed on commercial vehicles – usually due to safety risks.
This same article from the FMCSA states that “no holes shall be drilled in the top or bottom rail flanges, except as specified by the manufacturer,” which is a common thread between commercial and light-duty consumer vehicles.
Once any vehicle’s frame rails have been cut, re-welded, drilled, or otherwise modified or repaired, there is a possibility that that vehicle may no longer allowed to drive on the highway.
Granted, if these vehicles with modified frames are no longer allowed to operate on the highway, a vehicle can be registered as “off-highway only” and restrictions become much more relaxed.
However, the structural integrity will typically be enhanced in the hands of a qualified fabricator.
Suppose you are caught operating a vehicle on the highway that should not be on the highway due to having an unlawfully welded frame. In that case, you can be sent to the state vehicle referee who will examine your vehicle in depth and find anything unlawful about it and impose hefty fines for not following laws and regulations.
The last thing you want to happen is to get into a collision and your vehicle insurance drops your policy after finding poorly done welding repairs to your vehicle frame.
Worse yet your collision causes bodily harm to others.
Is it illegal to sell a vehicle with a welded frame?
It is typically not illegal to sell a vehicle with a frame that has been welded on (please consult your local laws – this article is not to be considered as legal advice), but it is unlawful to sell a vehicle that has a welded frame or with frame damage without informing the buyer first.
The fact that selling a vehicle with a welded frame can be considered unlawful becomes apparent when the vehicle’s safety and/or value are questioned.
For example, if a person has a pickup truck and decides to weld a tubular pre-runner bumper on the front of the truck, then later sells the truck to a buyer, he must fully disclose that the frame has been welded on since there is a risk that the safety of the vehicle has been diminished (non-OEM vehicle parts were added).
Not only this, but there is always the question about the value of the vehicle after a frame has been welded – even if the welded frame is perceived to add value (such as with the pre-runner bumper).
The true deciders of the value of a vehicle are a car dealership (only sometimes), a bank (commonly when the vehicle is still bank-owned), and the auto insurance companies (always).
TIP: If you are selling a vehicle with a frame that has been welded, it is always a good idea to write a statement of vehicle condition, noting the condition of the vehicle’s frame, and possibly adding some photos to that document. If you have the buyer of your vehicle sign that document acknowledging the condition, your bases should be covered in case your buyer gets into an accident or wants to file an auto fraud claim against you.
This signed document, even if it might not truly be legally binding in format, shows the seller’s full disclosure and the buyer’s acknowledgment, which should go a long way in a legal dispute.
Laws regarding the sale of a vehicle can vary depending on the state that you are in, but it is strongly recommended to seek professional legal advice when selling a vehicle with a questionable condition.
Especially if the vehicle’s value is high, such as with large trucks or even 18-wheeler tractors.
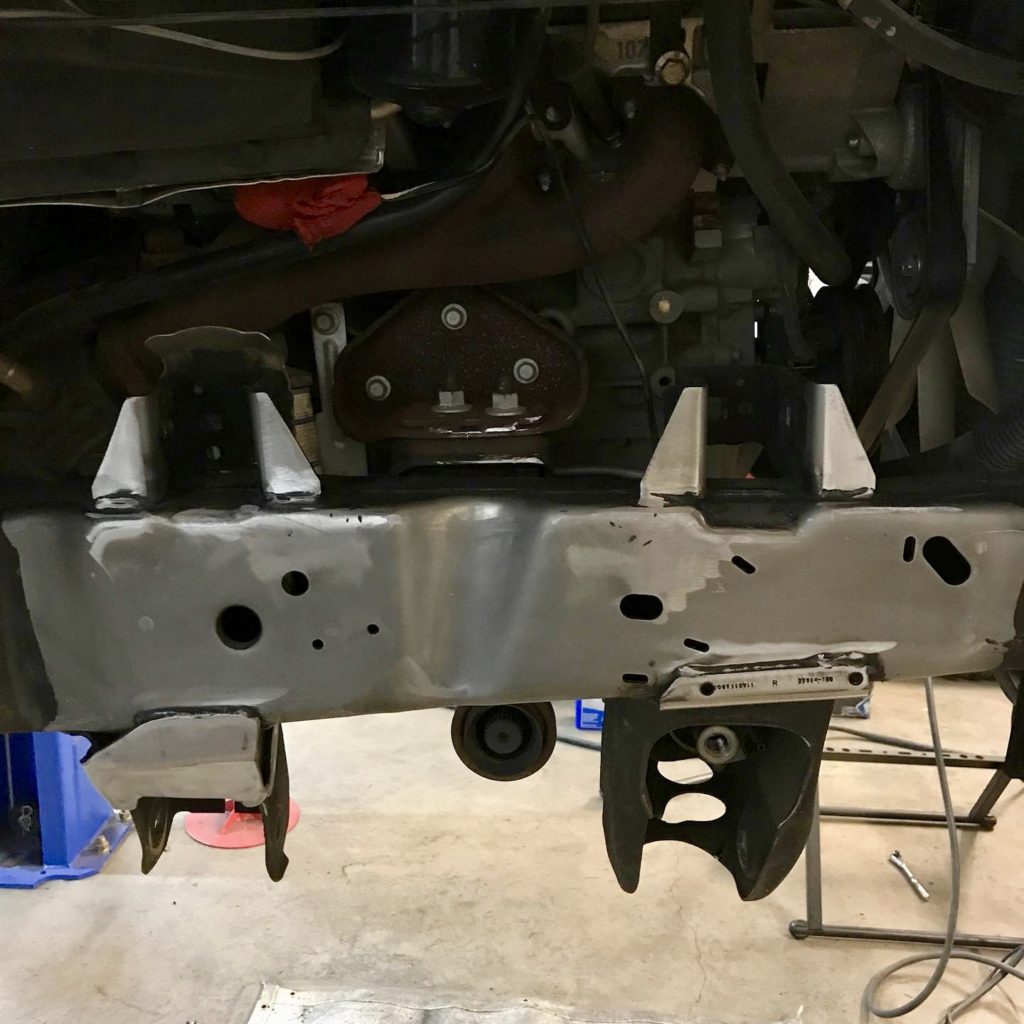
How to Weld Vehicle Frame Pieces Together?
If a vehicle’s frame needs to be welded together either for off-highway use or if performed per the vehicle manufacturer’s recommendations, some general recommendations need to be followed in order to help prevent cracks in your vehicle frame.
The number one rule for the welding technique on a vehicle frame is to avoid a single vertical butt joint where the two halves of a frame are joined together from top to bottom with a single weld.
Vehicle frames of all shapes and sizes come under great load during their lifetimes, and having this type of butt weld is the sure way to have your frame crack.
More suitable techniques for welding frame pieces together make the joint much stronger so as to avoid further breakage.
- Conventional wisdom on welding frame joints is to make sure the joints (sides, top
and bottom) are at an angle close to 45 degrees so that thereis maximum weld bead and surface area to spread the stress load on the weld joint. - Additional strengthening techniques include fish plating over the top of the welded area, and/or adding structural tubes or channels either inside or over the top of the frame rails.
- You cannot over-strengthen/over-engineer your repair area, but you can weaken the metal surrounding the repair area due to welding heat potentially causing other areas to crack – be careful of your heat affected zone.
These frame strengthening techniques are common between smaller and larger vehicles, of
How to Weld Larger Truck Frames?
One concern with larger trucks is that their frame rails are sometimes heat treated to an exact specification to optimize their strength.
Welding on these frame rails carries a high-risk factor since the heat-treated frame rail material right next to the repair plate/channel material might cause cracking due to the dissimilarity between the two metals.
If the repair is truly a “bush-fix” then annealing the heat-treated rail material surrounding the weld repair area with a torch should allow for good weld penetration. Anything other than a “bush-fix” on heat treated frame rails is a bad idea and you should seek professional advice.
NOTE: Large trucks which have heat-treated frame rails, such as semi-truck tractors, are closely regulated by the DOT in the United States and you might end up not being able to pass subsequent DOT inspections with the repairs you perform on your frame.
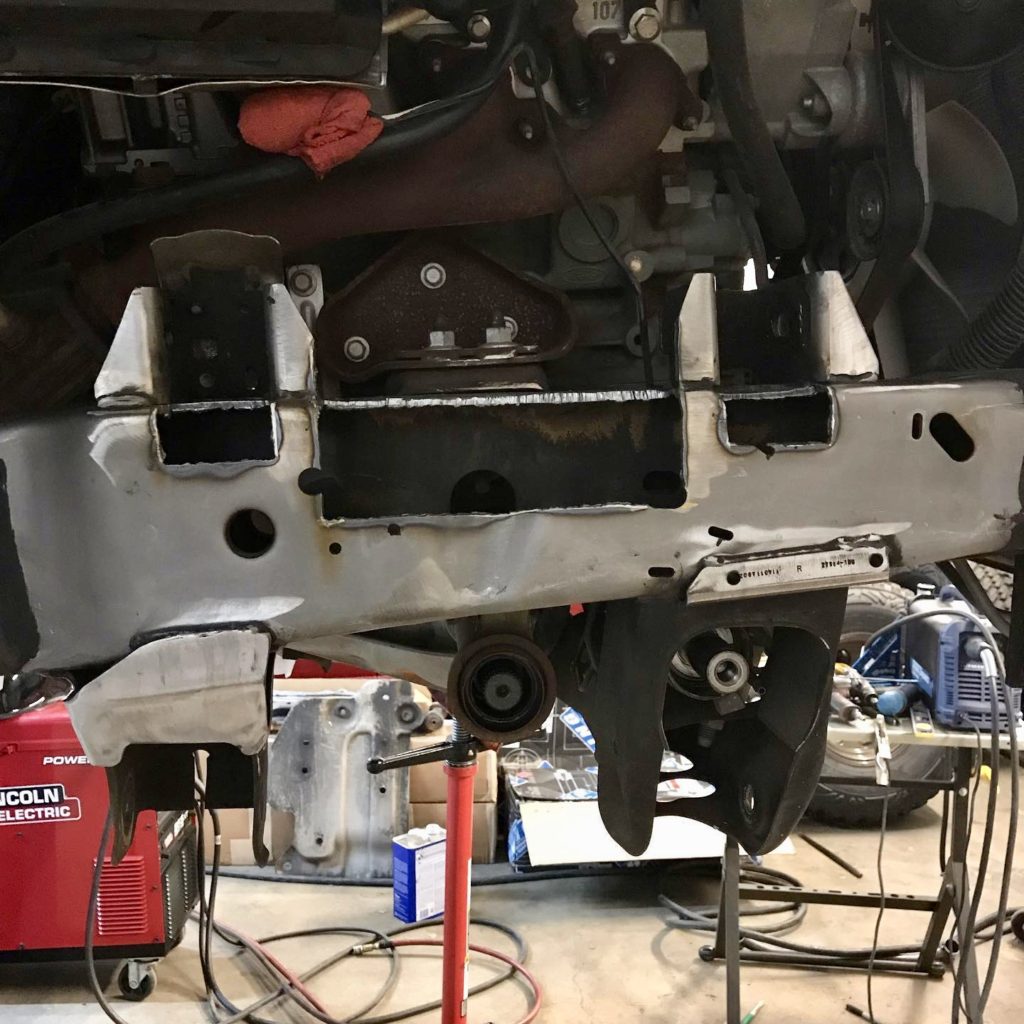
What Special Equipment Do I Need to Weld on a Vehicle Frame?
This heavy-duty welding coat is a good starting point when considering special equipment for welding on cars.
As long as you have your typical welding outfit including: welding PPE, welder, gas, angle grinder, etc., you shouldn’t need any special equipment to achieve a basic weld on a vehicle frame – but there are exceptions.
If you are welding a piece of structural tubing or channel inside or onto the vehicle frame, some special fit-up jigs might be helpful tooling to add to the tools at your disposal and a plasma cutter.
Special fit-up jigs can be especially useful for welding on a vehicle frame when the body of the vehicle is still attached since there can be very limited maneuverability between the frame rail and the vehicle body.
This special tooling can look like vise-grips style clamps or large adjustable C-clamp style in order to temporarily affix the tubing or channel to the vehicle frame rail before and during the weld.
In the case of automotive restoration shops where vehicles are restored from the ground up, a common tool is a car rotisserie. I recommend this brand Titan.
Car rotisseries are used to rotate an entire vehicle while attached from the front and rear ends to a large frame, in a similar way that food rotisseries function.
Being able to rotate the vehicle as a whole makes it easier on the technician working on the vehicle so that operations under the vehicle don’t have to be performed overhead while a vehicle is on a traditional vertical vehicle lift.
PRO TIP: If you are not sure what amperage to use with a certain piece of material, whether thick or thin, aluminum or steel, it is always a good idea to practice a weld bead on a scrap piece of material similar to the final metal workpiece you intend to weld. This small amount of time practicing will save you time grinding out your weld after you find out that your weld does not have a correct amount of penetration for the thickness of material you are welding.

Should I MIG or TIG Weld My Vehicle Frame?
Countless variables determine the quality of a finished weld, therefore, there is no guarantee that by selecting MIG vs TIG welding there will be a preferable outcome.
There are some determining factors inherent with each of the MIG and TIG welding processes that have a strong correlation to the quality of a weld.
The more significant variables include:
- Welder skill
- Filler material selection/interaction with the base material
- Welding process
It’s a fact that welding technicians grow their skills in certain welding processes and might not be as proficient in other processes.
For example, a professional TIG welder who welds on aluminum boat railings for a living doesn’t necessarily have the same learned techniques that an automotive body repair technician might have.
Due to this simple fact, one welding technician can make a high-quality weld with a MIG machine and another welding technician can make a poor-quality weld with a MIG machine.
For the purposes of discussion, we will, therefore, consider welding skill the same when looking at the other variables.
Why TIG Welding on your car frame is better?
- There is a wider filler material selection for TIG welding processes which is an advantage when compared to MIG welding where the user needs to run the wire through the feed tube. More to the point of filler material affecting the vehicle frame, this is application dependent.
- Most stamped steel frames can be welded with either MIG or TIG welding processes, but when a vehicle frame has chrome-moly tubing supports or intricate curvatures such as with racing frames or with motorcycles, TIG welding is your optimal choice.
- TIG welding will provide a far superior product when welding together vehicle frames that contain high allow steels which are heat sensitive and may be susceptible to cracks in the heat affected zone.
- MIG welders (if not set up properly) can create “cold starts” where the penetration of the base material is not complete, which creates a weld situation where the joint might be compromised in a certain area.
If your application appears to be more of a heavy-duty industrial frame or a frame that will only see standard commuting-to-work type use, then MIG welding is most likely your best choice. If your application includes anything more strenuous or extreme, such as racing, off-road, or otherwise, TIG welding is most likely your best choice for welding on a vehicle frame.
PRO TIP: All MIG welders are different, and all welding applications are different. Once you find your optimal weld setting for your MIG welder (for your specific application, write this down on a paper and attach it to the side of your welder. This will save you fromthe headache which happens when another operator uses your machine, or the machine gets bumped and your settings are lost.
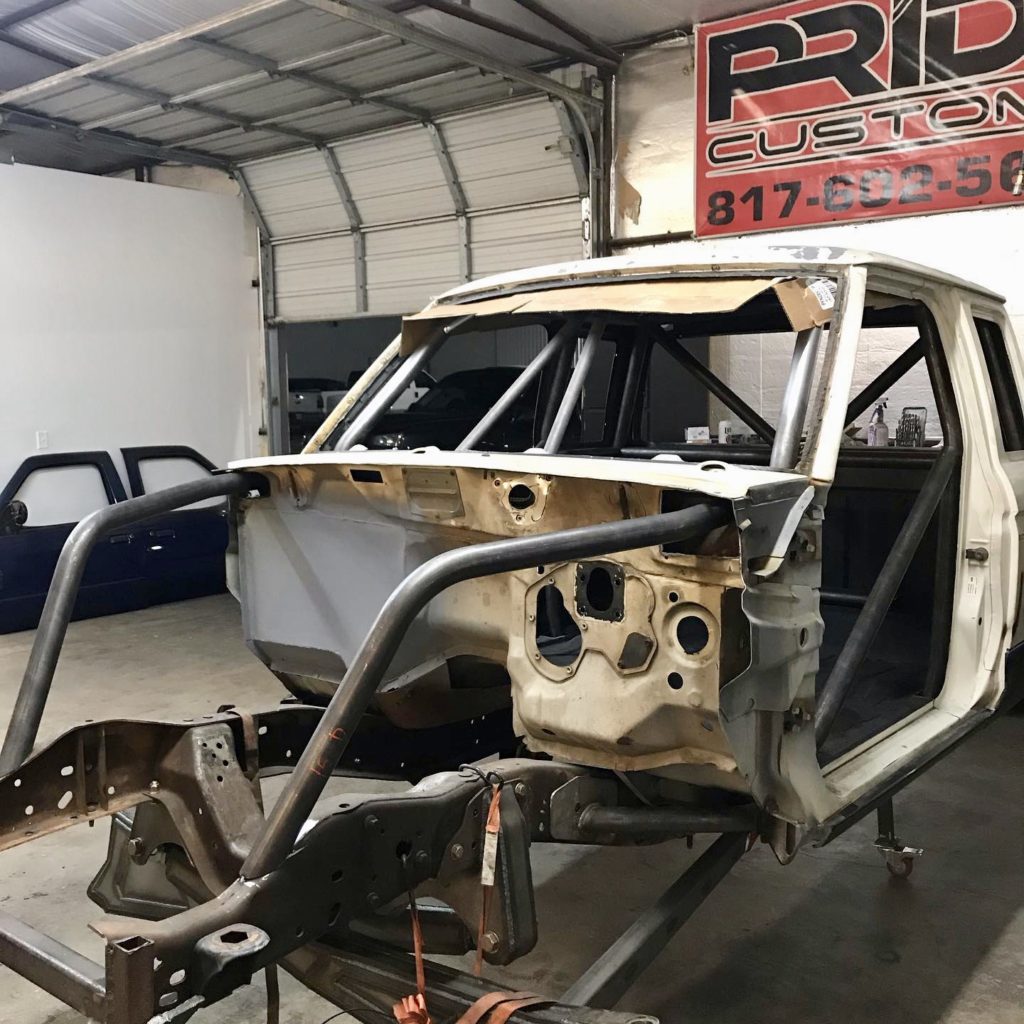
Will Welding on a Vehicle Frame Damage the Vehicle’s Computer?
You can weld on your vehicle’s frame, but you have to take certain precautionary steps. These common-sense steps follow electrical engineering concepts, but as we have all learned with recent vehicle recalls, automotive engineers sometimes make odd design decisions that could potentially change this common-sense methodology.
Therefore, before you start welding on your vehicle frame, or anywhere else on your vehicle, consult your vehicle’s manual and/or your vehicle’s manufacturer for absolute advice.
- Always disconnect the negative battery terminal from the vehicle so that you open the electrical circuits in your vehicle to your battery, thus reducing the risk of
over voltage situations which may damage your vehicle’s onboard computer. - Place the welding ground clamp as close as possible to your welding arc to minimize the electrical path between your arc and your ground, reducing the risk of high voltage reaching your vehicle’s sensitive computer components.
- Disconnect the airbag plugs under the hood of your vehicle. There is a slight chance that some welding voltage reaches your airbags and triggers them to go off. This is the last thing you want since airbags are not only very expensive but once airbags are deployed, your vehicle might be
required to have a “salvage title” from then on.
NOTE: Following these precautionary steps eliminates almost all the risk associated with welding on your vehicle (regarding damaging on-board computer components), but if you want to reduce risk completely, your best option is to completely disconnect your vehicle’s ECU.
Disconnecting your vehicle’s ECU has its own implications such as potentially disrupting the OBD2
If you have ever investigated replacing an ECU, they can sometimes be very expensive. Sometimes ranging in the thousands of dollars!
Therefore, it is always wise to be conservative and careful with your onboard computer system when considering welding on your vehicle frame.