There are two main types of flux core wire: self-shielded (FCAW-S) and gas-shielded (FCAW-G). Self-shielded wire requires no external shielding gas, while gas-shielded wire uses shielding gas to protect the weld from atmospheric contaminants. Both types are used for various welding applications and material thicknesses.
Flux-cored arc welding (FCAW) is a popular welding process widely used in constructing, fabricating, and repairing metal structures. One of the key components of this process is the flux core wire, which serves as the filler metal and shielding gas.
Using a flux core wire eliminates the need for a separate shielding gas, making it an ideal choice for outdoor and windy welding applications. However, with the wide range of flux core wires available on the market, choosing the right one for a specific welding job can be challenging.
In this article, I will provide an overview of the different types of flux core wires for MIG welding, their unique characteristics, and their typical applications. Whether a welding professional or a DIY enthusiast, this article will help you understand the options and choose a suitable flux core wire for your next welding project.
If you are looking to purchase a flux core welding machine, please read through our buying guide.
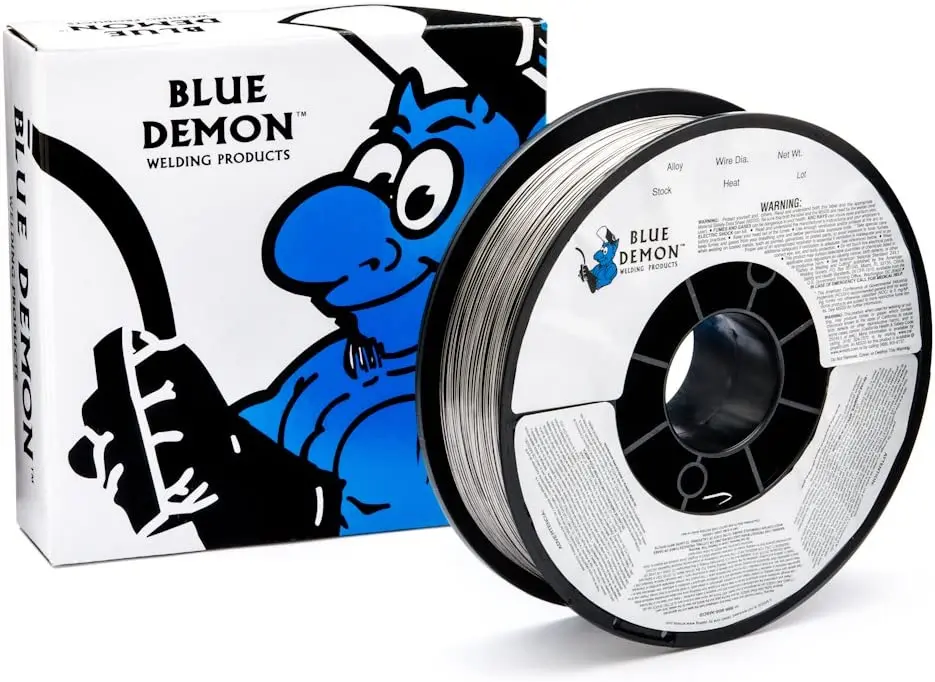
E70T-1C
E70T-1C is a low hydrogen, all-position flux core wire commonly used for welding pressure vessels, pipelines, and storage tanks. This wire provides excellent arc stability and weldability, minimizing the risk of hydrogen-induced cracking.
E70T-5
E70T-5 is a high-strength, low hydrogen flux core wire specifically designed for heavy fabrication, shipbuilding, and offshore structures. Its low hydrogen content makes it suitable for highly demanding applications, ensuring the weld’s integrity and durability.
E70T-1
E70T-1 is another low hydrogen, all-position flux core wire that shares similar applications with E70T-1C, including pressure vessels, pipelines, and storage tanks. This wire ensures excellent weldability and minimal hydrogen content to prevent hydrogen-related issues.
E70T-9
E70T-9 offers a high deposition rate and self-shielding capabilities, making it ideal for pipe welding, heavy fabrication, and shipbuilding. This wire provides excellent weld penetration and deposition efficiency, enabling faster completion of tasks.
E70C-6M
E70C-6M is a high-strength, low-spatter flux core wire for heavy fabrication, offshore structures, pipelines, and shipbuilding. This wire offers exceptional weld quality and minimal spatter, ensuring a clean and efficient welding process.
E71T-1
E71T-1 is a low hydrogen, all-position wire for welding pressure vessels, pipelines, and storage tanks. Like other low hydrogen wires, it minimizes the risk of hydrogen-induced cracking, providing reliable and long-lasting welds.
E71T-11
E71T-11 is a self-shielding, all-position wire suitable for structural steel, sheet metal, agricultural equipment, and pipes. Its self-shielding properties eliminate the need for external shielding gas, allowing for easy use in various applications.
E71T-GS
E71T-GS is a self-shielding, all-position wire designed for light fabrication, home repair, and maintenance. This wire provides a user-friendly welding experience, making it perfect for DIY enthusiasts and professionals.
E71T-1C
E71T-1C, like E70T-1C, is a low hydrogen, all-position wire suitable for pressure vessels, pipelines, and storage tanks. It ensures excellent weldability and reduces the risk of hydrogen-induced cracking, making it an ideal choice for critical applications.
E71T-12
E71T-12 is a self-shielding, all-position wire for welding structural steel, sheet metal, and pipes. Its self-shielding properties make it a versatile and convenient option for various applications, especially in areas where shielding gas is not easily accessible.
E71T-9C
E71T-9C is a self-shielding, all-position wire designed for welding steel plates, pipes, and metal structures. Its self-shielding characteristics provide flexibility and convenience, allowing for efficient welding in various environments.
E71T-7M
E71T-7M is a self-shielding, all-position wire ideal for light fabrication, home repair, and maintenance. It offers a user-friendly welding experience and is perfect for DIY enthusiasts and professional welders.
E71T-5C
E71T-5C is a self-shielding, all-position wire suitable for light fabrication, maintenance, and repair. Its self-shielding capabilities make it a convenient and versatile option for various welding applications.
E71T-8
E71T-8 is a self-shielding, all-position wire for heavy fabrication, shipbuilding, and offshore structures. Its self-shielding properties allow for efficient and reliable welding in demanding environments without external shielding gas.
E71T-9M
E71T-9M is a self-shielding, all-position wire for welding steel plates, pipes, and metal structures. It offers excellent weld quality and self-shielding capabilities, making it a convenient option for various applications.
E71T-1M
E71T-1M is a low hydrogen, all-position wire suitable for pressure vessels, pipelines, and storage tanks. Its low hydrogen content ensures excellent weldability and reduced risk of hydrogen-induced cracking, making it an ideal choice for critical applications where weld integrity is crucial.
E70S-3
E70S-3 is a high-strength, low hydrogen flux core wire for heavy fabrication, shipbuilding, and offshore structures. Its low hydrogen content helps maintain the weld’s durability and integrity in demanding environments, ensuring long-lasting performance.
E70S-6
E70S-6 is a high-strength, low-spatter flux core wire suitable for heavy fabrication, offshore structures, pipelines, and shipbuilding. This wire offers exceptional weld quality and minimal spatter, resulting in a clean and efficient welding process that meets the needs of various industries.
Table of Contents
Types of Flux Core Wire
Flux core wire is an essential component in the MIG welding process and comes in various types to meet different welding requirements.
The most common types of flux core wire used in MIG welding are E71T-1C, E70T-5, E71T-11, E71T-GS, E70T-1, and E70T-9.
It is important to choose the right type of flux core wire based on the specific requirements and conditions of the welding project and to consult a welding professional or the manufacturer’s specifications before deciding.
Gas Shielded
Gas-Shielded Flux-Cored Wire: Gas-shielded flux-cored wire requires an external shielding gas, typically CO2 or Argon, to protect the weld from atmospheric contamination. The shielding gas is supplied to the weld area through a separate hose connected to a gas bottle.
Gas-shielded flux-cored wire is typically used for high-quality, critical welding applications and produces minimal spatter.
Self Shielded
Self-Shielded Flux-Cored Wire: Self-shielded flux-cored wire does not require an external shielding gas. Instead, the flux in the wire generates its own protective gas as it burns, shielding the weld from atmospheric contamination.
Self-shielded flux-cored wire is ideal for outdoor and windy welding conditions and is often used for production welding and welding on dirty or rusty surfaces.
Dual Shielded
Dual-Shielded Flux-Cored Wire: Dual-shielded flux-cored wire combines the benefits of both gas-shielded and self-shielded flux-cored wire. It requires an external shielding gas for added protection but also contains a self-shielding flux for use in outdoor and windy welding conditions.
Dual-shielded flux-cored wire is often used in welding applications that require both high-quality and efficiency.
Selecting the Right Wire and Gas
The right size of flux-cored wire to use depends on several factors, including the following:
Material Thickness
The thickness of the material being welded will affect the wire size needed. Thicker materials will require a larger wire size, while thinner materials will require a smaller size.
The most common sizes and their respective mild steel thickness are:
Flux Core Wire Size (inches) | Mild Steel Thickness (inches) |
---|---|
0.030 | 18 gauge to 1/8″ |
0.035 | 14 gauge to 3/16″ |
0.045 | 1/8″ to 1/4″ |
Welding Current
The welding current will also affect the wire size needed. Higher welding currents typically require a larger wire size, while lower ones require a smaller one.
Welding Position
The position where the welding takes place will also affect the wire size needed. Out-of-position welding may require a larger wire size to prevent sagging, while welding in a flat position may require a smaller one.
Welding Speed
The welding speed must also be considered when selecting the wire size. Faster welding speeds typically require a larger wire size to prevent overheating, while slower welding speeds may require a smaller one.
Conclusion
In conclusion, flux core wire is an essential component in welding and plays a crucial role in ensuring the quality of the final weld. The different types of flux core wire, such as gas-shielded, self-shielded, and dual-shielded, offer varying advantages depending on the application and welding conditions. Choosing the right type of flux core wire is important to ensure the best results and minimize potential problems.
Whether for welding on-site, in a fabrication shop, or heavy industry, a flux core wire can meet the requirements and ensure a successful welding outcome. Understanding the different types of flux core wire and their applications will help you make the best decision for your welding needs.