A shielding gas mixture of argon and carbon dioxide (CO2) is typically used to weld stainless steel, such as a 98% argon/2% CO2 or 90% argon/10% CO2 mix. This combination offers optimal weld quality, corrosion resistance, and minimal spatter while working with stainless steel in TIG and MIG processes.
Stainless steel is a versatile material widely used in many industries due to its durability and corrosion resistance. Welding this material, however, requires particular gases to ensure optimal results.
In this article, I will explain why argon and argon-based welding gases are the most popular and how to weld stainless steel using the proper gas mixture.
Here is a quick summary of various common stainless steel welding scenarios and recommended shielding gas blends:
Welding Scenario | Recommended Welding Gas |
---|---|
Conventional Welding of Various Stainless Steel Types | 90-98% Argon with 2-10% CO2 |
Fast Welding for Large Projects | 65-70% Argon with 30-35% Helium |
Welding of Austenitic Stainless Steel (GMAW and FCAW methods) | Argon with up to 10% Hydrogen |
Welding of Austenitic Stainless Steel (GTAW method) | Argon with up to 50% Hydrogen |
Enhanced Corrosion Resistance | 90-98% Argon with up to 10% Oxygen |
Welding in Low Temperatures | 100% Argon |
Short Circuiting or Welding in Low Voltage | Argon with up to 85% Helium |
Welding Duplex and Precipitation-hardening Stainless Steel | Argon with Nitrogen |
Table of Contents
Why is Argon The Standard Welding Gas?
Argon is an inert gas with a versatile thermal conductivity range. It also remains very stable even with reactive gases like oxygen or helium.
Most welding gas mixtures use argon as a base, as it regulates reactive additive gases like carbon dioxide and helium to minimize oxidation rates or stabilize combustibility.
Argon can work in both low-temperature welding methods like gas tungsten arc welding (GTAW) and high-temperature settings such as gas metal arc welding (GMAW) and flux-cored arc welding (FCAW).
Due to its inert nature, it serves primarily as a shielding gas to protect your weld pool from contaminants, such as free-ranging oxygen that might induce oxidation that causes rust and weakening of weld joints.

Gas Blend to Weld Stainless Steel
Argon in its pure form can maintain arcs and retain heat even in low temperatures. However, mixed gas blends are preferable when welding stainless steel.
Additive gases like carbon dioxide, oxygen, or helium are usually added to increase heating capacity, increase welding speed, or improve corrosion resistance.
Carbon Dioxide Blend
Argon mixed with 2–5% carbon dioxide is the standard gas blend for conventional welding since it works on narrow and wide-surfaced metals.
This gas ratio can create narrow spray and wider globular transfers and produce consistent arcs. Carbon dioxide also improves welding speed and travel time by up to 25%.
Oxygen Blend
90–98% argon mixed with oxygen improves corrosion resistance, but oxygen should remain below concentrations of 10% to prevent oxidation. It’s also good for keeping the molten weld in its liquid state longer.
Helium Blend
A gas blend of argon with up to 35% helium is a good option to fuse metals quickly. Helium concentrations of up to 85% improve short-circuiting, enabling you to weld more quickly on low voltage.
Hydrogen Blend
Hydrogen (up to 10% maximum) mixed with argon is good for welding austenitic stainless steel using gas metal arc welding (GMAW) and flux-cored arc welding (FCAW) methods.
When using the gas tungsten arc method (GTAW), up to 50% hydrogen can be added, which improves welding speed by up to 50–100%. Hydrogen should only be used on austenitic steel alloys, however.
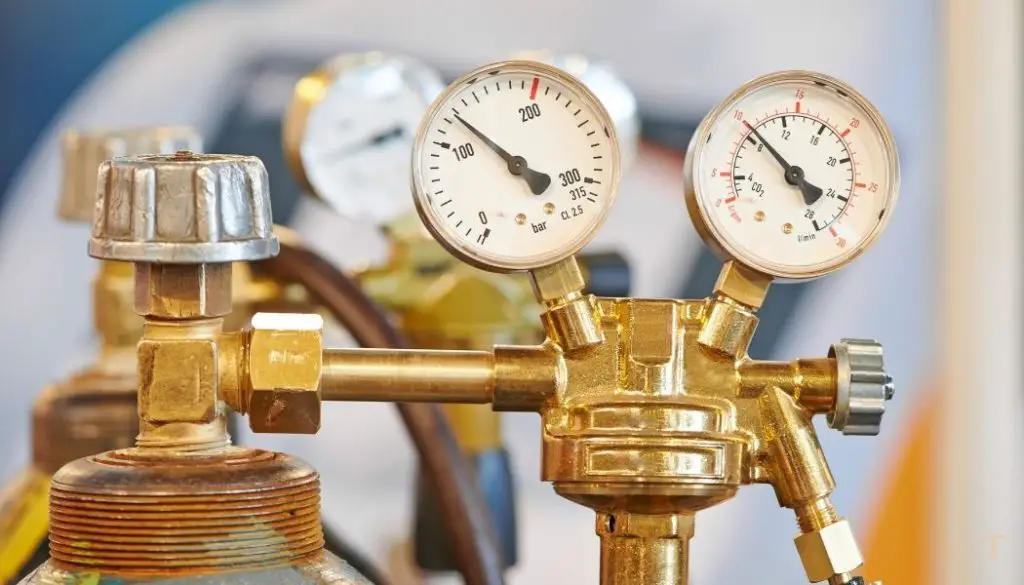
How to Weld Stainless Steel
Here are the steps you should follow to weld stainless steel:
1. Inspect Your Stainless Steel Surfaces
Inspect the surfaces of the stainless steel parts you will weld for any dents, cracks, or bent parts. You may also clean the parts first to eliminate grease or oily surfaces.
Smoothen and clean any disfigured or dirty areas first to improve weld fusion and fitting and avoid accidents.

2. Pick the Correct Filler Wire
You should choose a compatible steel filler wire for the stainless steel you will weld. This can be a difficult task that requires sufficient knowledge about steel alloy mixtures. It becomes more complicated when working with mixed, dissimilar, or unknown metals.
As a rule of thumb, you should choose a stainless filler wire of the same material as your stainless steel parts, or at least in the same grade.
Choose a 316L filler wire to match your 316L austenitic steel (same material), and a 308 filler wire or a stick electrode when welding austenitic stainless steel in the 300 series (similar grade).
3. Choose the Appropriate Welding Gas Mix
You should also know how various gases interact with metal during welding. Choose the right argon-based gas mixture depending on how fast you want to work, and the arc type you want to achieve (spray transfer, globular transfer, short-circuiting).
Remember that certain additive gases might not work well with some stainless steel types. For example, hydrogen and nitrogen should only be used on austenitic and semi-austenitic alloys such as duplex and precipitation-hardening stainless steel.
4. Check Your Welding Machine’s Amperage and Voltage
Finally, select the appropriate amperage and voltage settings. This will depend largely on metal thickness and time constraints.
A thicker material will require a higher welding current and voltage from your welding machine. However, welding gas ratios can affect arc formation and decrease or increase amperage and voltage settings accordingly.
For example, using pure argon might take longer and require higher welding current (amperage) and voltage than with the same settings with an argon-carbon dioxide mix.
Conclusion
Choosing the right welding gas depends on the type of stainless steel you use.
Generally, argon-based gas mixtures enable you to weld stainless steel efficiently with the right settings.