To weld thin metal, choose an appropriate process (TIG or MIG with low amperage), use a smaller diameter wire or filler rod, and adjust travel speed to prevent burn-through. Employ a pulsing technique, stitch welding, or tack welds to manage heat and allow cooling periods between welds to minimize warping.
When most people think about welding, they think about powerful machines welding massive metal sheets. However, welding is also a useful tool for welding thin, delicate pieces of metal. There are a few reasons why you may want to weld thin metal. Maybe you’re working in a factory that uses thin sheet metal or trying to make welding art at home.
Welding thin metal comes with its own unique challenges. You can get around them by adjusting the welding angle, shielding gas, and other aspects of the welding job.
Whatever the reason you are tackling this challenge, here are the ways to successfully weld thin metal.
Table of Contents
Why Is Welding Thin Metal Different?
If welding is a versatile, universal technique, you may wonder why you need a separate guide just to weld thin metals. These are metals just like any other.
However, there are a few reasons why welding thin metals differs from welding thicker substances.
Thin metal is more sensitive to heat.
Welding works by melting the metal you are working with just enough to create material for a seam. With thin metals, it’s a lot easier to melt the metal all the way through if you’re not careful and don’t have enough control over the heat of your welding machine. That is called burn-through.
Many welders compensate for this by lowering the heat, but the joints will not be supple enough if you don’t use enough heat. Striking a balance between just enough heat and not enough is a delicate task, especially for beginners.
That is why welding thinner metals such as aluminum is much harder than welding thicker materials.

Choose the Best Welding Process for Thin Metals
There are several welding methods out there, including:
- MIG welding
- TIG welding
- Stick welding
Of these methods, the best one for welding thin metals is MIG welding. This is the most common type of welding that people in manufacturing use for welding sheet metals, which are thin pieces of metal. You can also pulse when using MIG welding, lessening your burn-through risk.
Although TIG welding was designed for very thick pieces of metal, it is also a good choice for welding thin metals. TIG welding is more precise and gives you more control over the heat application. However, it is much harder to use for amateurs.
When working with very thin metals, skip stick welding. This method gives you the least control over the heat application and will most likely result in burn-throughs, splattering, and excessive slag formation.
Step-by-Step Guide to MIG Weld Thin Metals
MIG welding is the most common technique welders use for thin metals. Here are the steps you need to take for this process.
1. Choose the Right Shielding Gas
MIG welding works in tandem with the shielding gas, which prevents the weld from oxidizing. The shielding gas also affects the weld bead’s appearance. For thin metals, you want a weld bead that won’t produce a lot of spatter when it appears.
Use shielding gases that have high argon concentrations.

2. Choose the Right Filler Metal
The filler metal is the metal that melts into the weld and fills the gap between the two pieces. MIG welding automates feeding the filler, which makes your life as a welder easier. The material doesn’t matter as much as the form of the filler metal.
Ensure you use very thin wires when working with reedy, thin sheet metal.
Metal Thickness (inches) | Recommended MIG Wire Size (inches) |
---|---|
0.024 | 0.020 |
0.030 | 0.023 |
0.036 | 0.025 |
0.048 | 0.030 |
0.060 | 0.035 |
3. Adjust Your Torch Angle
Changing the torch angle when MIG welding goes a long way to preventing burn-throughs. Make sure you adjust the angle to shorten the distance between the tip and the metal, no matter the welding position you work in. This will make the arc more stable, giving you more control over the weld and lessening the chance of burn-through.
4. Try Pulsing
Besides your regular MIG welding technique, you can also try pulsing when welding thin metals. When you pulse metals, you heat a small portion of the plates you are trying to join, then let the weld pool completely before filling in the joint. Although pulsing requires practice to master, it gives you more control over the energy output.
Step-by-Step Guide to TIG Weld Thin Metals
Although TIG welding was designed for thicker materials, you can use it to weld thin metals thanks to the extra control you get over the energy output. Here are the steps to follow.
1. Adjust to the Correct Amperage Settings
The first thing you need to do when TIG welding thin metals is to adjust the amperage settings. Lower the power setting and switch out the anodes to smaller ones. This lessens the energy output. You don’t need as much energy to melt thin metals anyway, and this way, you prevent burn-through. TIG welding lets you control the heat as you weld with a foot pedal, so take advantage of that.
Metal Thickness (inches) | Recommended TIG Amperage Range (amps) |
---|---|
0.020 | 15-40 |
0.030 | 20-50 |
0.040 | 30-70 |
0.060 | 50-90 |
0.080 | 70-110 |
0.125 | 100-140 |
2. Pick the Right Filler Metal (and Add It Properly)
TIG welding uses tungsten anodes to create the arc. For thin metals, experts recommend 0.020 and 0.040 thoriated anodes. Thoriated tungsten is alloyed with the metal thorium, which gives the anode more current distribution.
Amperage | Tungsten Electrode Diameter (inches) |
---|---|
1-20 | 0.020 |
15-80 | 0.040 |
50-100 | 1/16 |
80-130 | 3/32 |
3. Use an Even, Fast Distribution
When TIG welding thin metals, avoid concentrating the heat in one place for too long. Stitch welding is the best technique, which uses a skip technique to apply a series of welds along a seam. This prevents you from applying too much heat in one place.
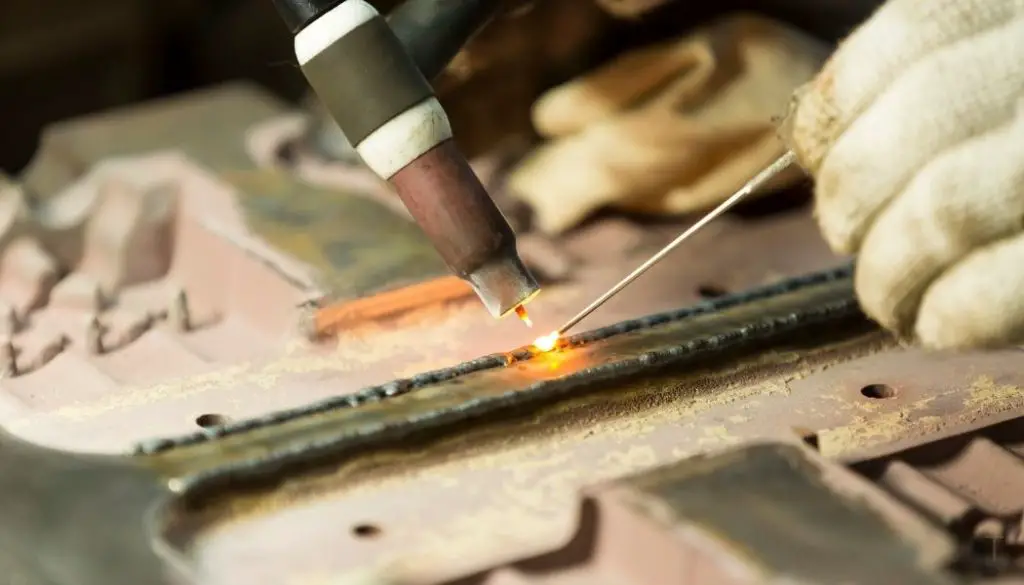
Final Thoughts
Welding thin metal is sometimes harder than welding massive chunks because the likelihood of burning through and damaging the base metal is much higher. For this welding challenge, use a welding method that gives you a lot of control, such as MIG or TIG welding, make sure you have the right electrodes and shielding gas, and adjust your technique.