This welding glossary is a comprehensive list of welding-related terminology, covering processes, techniques, equipment, and safety measures. It helps welders understand industry jargon, abbreviations, and concepts, enabling clear communication and facilitating learning within the welding trade.
It is not easy to learn how to weld, especially if you are a beginner. Regardless of whether you are learning to stick weld or trying your hand (and foot) at TIG welding, you will likely hear a word that you don’t understand.
I have been welding for over a decade, and I still find words that I struggle to understand. Whether related to a piece of equipment or a more advanced technique, I have put together this guide of all the confusing welding terms I can think of in this welding glossary.
Let’s jump in.
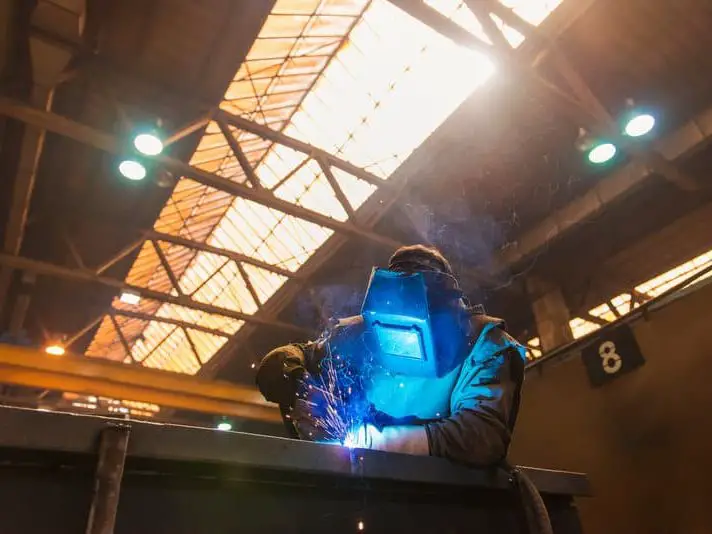
Abrasive – Slag used for cleaning or surface roughening.
Alloying – Adding a metal or alloy to another metal or alloy.
Alternating Current (AC) – Electric current that reverses direction periodically, usually many times per second.
Arc Welding – A group of welding processes that produces coalescence of metals by heating them with an arc, with or without applying pressure and with or without the use of filler metal.
Arc Welding Electrode – A part of the welding system through which current is conducted that ends at the arc.
Backfire – The momentary recession of the flame into the welding or cutting tip followed by reappearance or complete extinction of the flame.
Backhand Welding – A welding technique where the welding torch or gun is directed opposite to the direction of welding.
Backing – A material (base metal, weld metal, or granular material) placed at the root of a weld joint to support molten weld metal.
Base Metal (material) – The metal (material) to be welded, brazed, soldered, or cut. See also substrate.
Bend Radius – Radius of curvature on a bend specimen or bent area of a formed part. Measured on the inside of a bend.
Bevel – An angled edge preparation.
Braze Welding – A method of welding using a filler metal, having a liquidus above 840 °F (450 °C) and below the solidus of the base metals.
Burr – A rough ridge, edge, protuberance, or area left on metal after cutting, drilling, punching, or stamping.
Butt Joint – A joint between two members lying in the same plane.
Cap Pass – The final pass of a weld joint.
Coalescence – The uniting of many materials into one body.
Complete Fusion – Fusion that has occurred over the entire base material surfaces intended for welding, and between all layers and passes.
Complete Joint Penetration – Joint penetration in which the weld metal completely fills the groove and is fused to the base metal throughout its total thickness.
Covered Electrode – A filler metal electrode used in shielded metal arc welding, consisting of a metal-wire core with a flux covering.
Crater – In arc welding, a depression on the surface of a weld bead.
Crater Crack – A crack in the crater of a weld bead.
Cutting Attachment – A device for converting an oxy-fuel gas-welding torch into an oxy-fuel cutting torch.
Cylinder – A portable container used for transportation and storage of a compressed gas.
Deposited Metal – Filler metal added during welding, brazing or soldering.
Deposition Efficiency – In arc welding, the ratio of the weight of deposited metal to the net weight of filler metal consumed, exclusive of stubs.
Deposition Rate – The weight of material deposited in a unit of time.
Depth of Fusion – The distance that fusion extends into the base metal or previous pass from the surface melted during welding.
Direct Current – Electric current that flows in one direction.
Direct Current Electrode Negative (DCEN) – The arrangement of direct current arc welding leads in where the electrode is the negative pole and work-piece is the positive pole of the welding arc.
Direct Current Electrode Positive (DCEP) – The arrangement of direct current arc welding leads in where the electrode is the positive pole and work-piece is the negative pole of the welding arc.
Duty Cycle – The duty cycle describes the percentage of time that a power source can be operated at the rated output without overheating.
Filler Material – The material to be added in making a welded, brazed, or soldered joint.
Fillet Weld – A weld of an approximately triangular cross-section that joins two surfaces at right angles in a lap joint, T-joint, or corner joint.
Filter Plate – A transparent plate tinted in varying darkness for use in goggles, helmets and hand shields to protect workers from harmful ultraviolet, infrared and visible radiation.
Flat Welding Position – A welding position where the weld axis is approximately horizontal and the weld face lies in an approximately horizontal plane.
Flashback – A recession of the flame into or back of the mixing chamber of the torch.
Flux – Welding Flux is material used to prevent, dissolve, or facilitate the removal of oxides and other undesirable surface substances.
Forehand Welding – A welding technique where the welding torches or gun is pointed toward the welding direction.
Fusion – The melting together of filler metal and base metal (substrate), or of base metal only, which results in coalescence.
Gas Welding – Welding with the heat from an oxy-fuel flame, with or without adding filler metal or pressure.
Groove Weld – A weld made in a groove between two members. Examples: single V, single U, single J, double bevel etc.
Hard-Facing – Surfacing applied to a workplace to reduce wear.
Hot Crack – A crack formed at temperatures near the completion of weld solidification.
Hot Pass – In pipe welding, the second pass goes over the root pass.
Inclined Position – In pipe welding, the pipe axis angles 45 degrees to the horizontal position and remains stationary.
Incomplete Fusion – A weld discontinuity where fusion did not occur between weld metal and the joint or adjoining weld beads.
Incomplete Joint Penetration – A condition in a groove weld where weld metal does not extend through the joint thickness.
Inert Gas – A gas that does not combine chemically with the base metal or filler metal.
Joint – The junction of members or the edges of members to be joined or have been joined.
Kerf – The width of the cut produced during a cutting process.
Keyhole – A technique of welding in which a concentrated heat source penetrates completely through a work-piece forming a hole at the leading edge of the molten weld metal. As the heat source progresses, the molten metal fills in behind the hole to form the weld bead.
Lap Joint – A joint between two overlapping members in parallel planes.
Liquidus – The lowest temperature at which a metal or an alloy is completely liquid.
Melting Range – The temperature range between solidus and liquidus.
Melt-Through – Visible reinforcement produced on the opposite side of a welded joint from one side.
Open-Circuit Voltage – The voltage between the output terminals of the welding machine when no current is flowing in the welding circuit.
Peening – The mechanical working of metals using impact blows.
Plug Weld – A plug weld is a circular weld made through a hole in one member of a lap or T joint.
Porosity – A hole-like discontinuity formed by gas entrapment during solidification.
Post-Heating – Heat application to an assembly after welding, brazing, soldering, thermal spraying, or cutting operation.
Post Weld Heat Treatment – Any heat treatment after welding.
Preheating – Applying heat to the base metal immediately before welding, brazing, soldering, thermal spraying, or cutting.
Reinforcement – Weld metal, at the face or root, in excess of the metal necessary to fill the joint.
Residual Stress – Stress remaining in a structure or member as a result of thermal and/or mechanical treatment. Stress arises in fusion welding primarily because the melted material contracts on cooling from the solidus to room temperature.
Reverse Polarity – The arrangement of direct current arc welding leads with the work as the negative pole and the electrode as the positive pole of the welding arc.
Root Opening – A separation at the joint root between the workpieces.
Root Crack – A crack at the root of a weld.
Shielded Metal Arc Welding (SMAW) – A process that welds by heat from an electric arc, between a flux-covered metal electrode and the work. Shielding comes from the decomposition of the electrode covering.
Shielding Gas – The protective gas used to prevent atmospheric contamination.
Soldering – A joining process using a filler metal with a liquidus less than 840 °F and below the solidus of the base metal.
Solidus – The highest temperature at which a metal or alloy is completely solid.
Spatter – Spatter is metal particles expelled during welding that does not form a part of the weld.
Straight Polarity – Direct-current arc welding where the work is the positive pole.
Stress Relief Heat Treatment – Uniform heating of a welded component to a temperature sufficient to relieve a major portion of the residual stresses.
Stress Relief Cracking – Cracking in the weld metal or heat-affected zone during post-weld heat treatment or high-temperature service.
Stringer Bead – A weld bead made without transverse movement of the welding arc.
Tack Weld – A weld made to hold parts of a weldment in proper alignment until the final welds are made.
Tensile Strength – The maximum stress a material subjected to a stretching load can withstand without tearing.
TIG Welding – See Gas Tungsten Arc Welding (GTAW).
Torch Standoff Distance – The dimension from the outer face of the torch nozzle to the workpiece.
Underbead Crack – A crack in the heat-affected zone generally not extending to the surface of the base metal.
Undercut – Undercut is a groove melted into the base plate adjacent to the weld toe or weld root and left unfilled by weld metal.
Weld Bead – The metal deposited in the joint by the process and filler wire used.
Welding Leads – The workpiece and electrode lead of an arc welding circuit.
Welding Wire – A form of welding filler metal, normally packaged as coils or spools, that may or may not conduct electrical current depending upon the welding process used.
Weld Pass – A single progression of welding along a joint. The result of a pass is a weld bead or layer.
Weld Pool – The localized volume of molten metal in a weld before its solidification as weld metal.
Weld Puddle – A non-standard term for weld pool.
Wire Feed Speed – The rate at which wire is consumed in welding.
Work Lead – The electric conductor between the source of arc welding current and the work.