Undercut in welding refers to a defect where the base metal’s cross-sectional thickness is diminished by the weld, compromising the joint’s integrity and strength. This detrimental flaw occurs due to improper welding techniques, requiring careful prevention and corrective measures for optimal performance.
An undercut occurs when the weld puddle meets an area of metal that has not melted. This happens more often with non-ferrous metals. The flux we use when welding stainless steel has a bad habit of creeping out before the weld puddle and not melting. That is why, when the puddle meets this unmelted flux, an undercut takes place.
The most important advantage is that undercuts make cracks less likely to form when a weld cools and contracts. They are used on joints subject to severe loads, such as high shear forces.
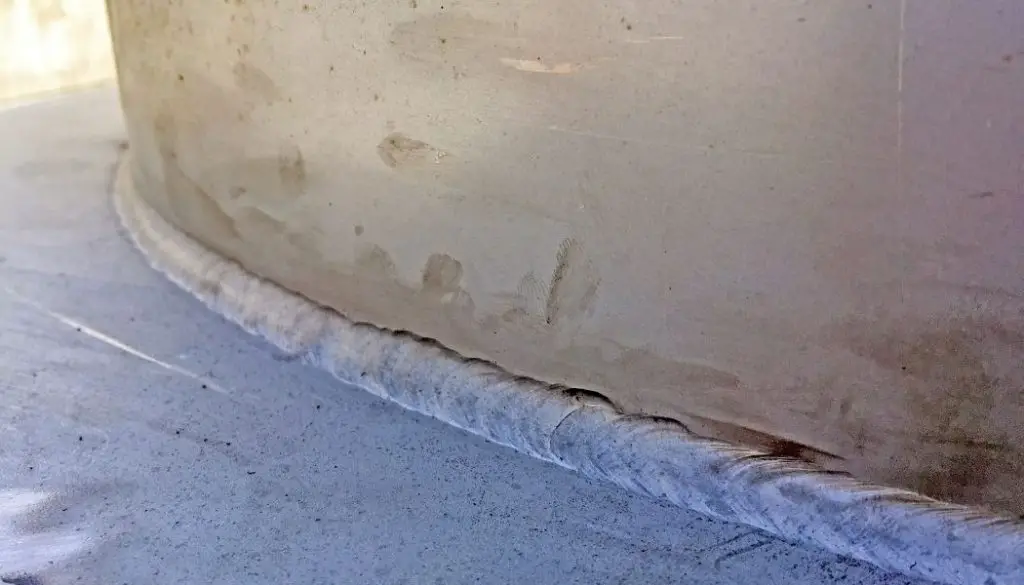
Table of Contents
What is Undercut in Welding?
An undercut is the formation of a depression in the face of weld metal caused by under-filling or lack of fusion in welding. The depression may be visible or invisible to inspection.
It happens when the flux does not melt completely in front of the puddle during one side of a fillet weld. This happens a lot with stainless steel because it takes more heat to melt that type of steel than regular steel, preventing proper fusion between both sides, thus creating an undercut.
Different Types of Undercut
There are many different types of undercuts. The most common types of undercuts are Internal and external.
Internal Undercut
An Internal Undercut happens when the weld metal is not deep enough inside the joint to completely cover the backside of the joint. This creates a concave surface on the backside and can be caused by several factors such as too small of a wire diameter for the welding application, poor joint fit-up, or improper technique.
Poor technique will usually look like the weld is not penetrating at all. Furthermore, sometimes it can be hard to tell if you have an internal undercut just by looking at your weld bead so don’t hesitate to pull it out and check.
External Undercut
An External Undercut is just the opposite of an internal undercut. It occurs when too much weld metal is deposited on the face side of the weld joint, causing a convex surface.
This can be caused by using too large of a wire diameter for the application or allowing too much heat to build up in your puddle and cause “blow-through”.
If you use filler metal that has a larger diameter than the base material (sheet metal thickness), this will usually blow through and create an external undercut, if you are not paying attention.
What Causes Undercut in Welding?
Whether you’re a beginner or an experienced welder, undercut welds are inevitable. Many mistakes can result in an undercut. Below is a list of a few causes of an undercut weld:
1. Using Wrong Size Filler Rode
One cause for an undercut is using too large of a filler rod when welding or making a tack weld. If you are unsure what size filler rod you should use, ASK! A good rule-of-thumb is if there is less than 1/8″ gap between your two pieces of metal, then use .030″ diameter filler rods and larger gaps require .045″ diameter rods.
2. Poor Gas Shielding
An undercut in welding is caused when too much flux and shielding gas (Argon, Helium) in the puddle. Filler rods usually contain a percentage of hydrogen, which reacts with oxygen in the air to create water vapor.
This action helps reduce oxidation of the metal, but if it becomes excessive, it can prevent the fluidity of the weld pool by turning it into a hot, sticky mess that doesn’t flow easily.
3. Poor Fit-Up
Another common cause for an undercut is when there is a gap between your two pieces of metal being welded together. The root of this problem is that you didn’t take the time to properly measure and fit up the two pieces before welding.
When this happens, you usually end up with a large gap between both sides or one side is longer than the other resulting in an undercut.
4. Fast Travel Speed
When you travel too fast with your arc, the metal will begin to melt faster than the rod can melt into it. This causes a poor fusion line and ultimately an undercut in your weld bead. The best way to solve this problem is by slowing down your travel speed and keeping a more consistent arc length.
5. Using High Voltage
High Voltage causes an Undercut in Welding because the arc heats the weld puddle more quickly than it can fill. This leaves a gap between the weld puddle and wire electrode, known as an undercut.
When using higher voltages for welding, you will need to use lower amperage settings.
6. Contaminated Shielding Gas
One of the most common causes of an undercut in welding is using contaminated shielding gas. When you use dirty or contaminated shielding gas it inhibits the flow of your weld puddle causing the arc to burn through on top which leaves a gap between your two pieces being welded together.
7. Inconsistent Shielding Gas Flow
Another cause of an undercut in welding is a lack of shielding gas. This can happen if you’re not using a gas lens to smooth out the flow of your gas, which directs the shielding gas over your weld puddle and keeps it from being blown away by air currents or too much turbulence around the arc.
Another reason could be that your regulator is turned up too high and you’re wasting gas by not having a smooth flow out of the timeline.
8. Inappropriate Filler Metal
An undercut usually occurs when the welding arc melts the base metal too quickly, creating a gap between the melted plate and the filler material. This can be caused by using a filler metal that is too large for the joint being welded, shooting an overly-hot arc, or traveling at an excessively high speed.
9. Welding too Fast
Welding too fast can cause an undercut in welding. When trying to fill a large gap between two pieces of metal, the arc will melt both sides and cool down into two pools before the rod melts into it. This results in an inadequate weld that is weak and has no penetration.
10. Excessive Arc Force
Excessive arc force can cause an undercut in welding by forcing the puddle away from the filler material, ultimately leaving a gap between the two pieces of metal.
11. Welding on Dirty or Rusty Metal
Rusty metal is another cause for an undercut in welding because the arc will burn through the rust quickly and create a hole that leaves no penetration for your filler rod, causing it to pop out.
This often leaves a poor-looking bead with little penetration that is weak and unable to hold up to its load.
12. Not Cleaning the Metal Thoroughly
The final cause for an undercut in welding is not cleaning your metal before starting your weld. This can happen if you are trying to save time by skipping some steps or ignoring some important pre-heating techniques.
Always remember to remove any debris or paint before welding.

How to Prevent Undercut
Undercuts are usually caused by some inaccuracy caused during the welding process. However, undercuts can be prevented or minimized by doing some precautions such as:
1. Slow Down Your Travel Speed
The best way to prevent an undercut in welding is by slowing your travel speed. This ensures the weld puddle and wire electrode have enough time to melt into the metal before moving on, eliminating burn through.
2. Keep a Consistent Arc Length
When you have a consistent arc length that matches your groove or gap being welded, you’ll avoid an undercut and create a clean and beautiful bead every time.
3. Use Lower Voltage with Higher Amperage
Another step to preventing an undercut in welding is using lower voltage with higher amperage values. When using high values for both welder settings, you will need low amperage for the arc to create a properly sized molten puddle, which will prevent burn through.
4. Use Filler Wire That Matches Your Joint Size
Using filler wire that matches your joint size is another way of preventing an undercut in welding because it melts off quickly, ensuring that you have no excess molten metal oozing out onto your piece being welded. This causes no penetration, making your weld weak and unable to hold up to its load.
5. Prevent Contamination of the Shielding Gas
A proven trick to preventing an undercut in welding is always using clean shielding gas. When using dirty or contaminated shielding gas it inhibits the flow of your weld puddle causing the arc to burn through the metal much faster than intended, ultimately leaving you with an undercut.
6. Use the Right Filler Metal
When you are using the right filler metal for your application you’ll avoid an undercut in welding by preventing too big of rod for your joint. Using the correct sized rod ensures that it melts into both sides and gives it a strong weld to add to its strength.
7. Use a Gas Lens
A gas lens is a great way to ensure a smooth steady flow from your timeline. This allows you to have a constant flow with a higher pressure, protecting your weld from falling into an undercut.
8. Use a Gas Shroud
Using a gas shroud is another way to prevent an undercut in welding by having a consistent flow all around your puddle. This ensures that the molten pool flows evenly and doesn’t collapse due to air from above. It also protects the arc from being blown by wind currents or turbulence during the welding process.
How to Fix Undercut in Welding?
To fix an undercut in welding, you have to find where the undercut was made. It might be easy or difficult depending on the circumstances of your weld.
For example, if it’s a large gap that is undercut then finding just one little hole might be enough for filler wire to make it strong again. Similarly, if it is small like a groove on something like aluminum, then there will likely be only two points where the arc burned through instead of multiple spots.
You can fix this by rewelding those areas and putting some more filler wire (make sure it’s not too much) over top of them, causing it to fill in any gaps which will prevent further undercut from happening again. Add extra wire to compensate for the movement to ensure it doesn’t undercut again in the same location.
Related Questions
What Is The Acceptable Amount Of Undercut Allowed?
The acceptable amount of undercut allowed is about 3/16″ of an inch. Anything more than that can affect the overall strength of your weld joint making it weak and more likely to fail under stress.
Does an undercut weaken a weld?
Absolutely! An undercut can decrease the overall strength of a weld by as much as 50% because it creates an imbalance in forces, making this part of your weld joint act like it’s falling.
How Is An Undercut In Welding Fixed On Steel?
Fixing an undercut on steel can be done by rewelding the area where the undercut was made onto your metal piece being welded. Make sure you are using a rod to make the weld about 1/8″ bigger than your piece being welded to ensure there will be enough molten metal for it to hold onto.