Welding electrodes are an essential component of arc welding. They are made of alloys that melt when weld current is passed through them. Due to the high level of heat involved, welding electrodes must be coated so they do not react with other elements in the air or atmosphere.
The coating of welding electrodes serves a variety of functions. It protects the electrode from deteriorating in the atmosphere and enhances metal deposition. In some types of welding, it is also used to shield molten weld puddles from reacting with chemically unstable gases present in the air around it.

Table of Contents
What are Electrodes?
Before we understand why welding electrodes are coated, we must know what they actually are.
They are the metal rod or stick that a welder uses to strike an arc and remove metals’ impurities during a welding process. There are various types of electrodes depending on the type of metal used as well as the coating material added to it.
Different Types of Electrodes
There are two main types of electrodes: consumable and non-consumable electrodes.
Consumable Electrodes
Consumable electrodes are designed to melt and fuse with the metal being worked on. These electrodes are essential for most electric arc welding processes like MIG (metal inert gas) and stick welding.
Non-Consumable Electrodes
Non-consumable electrodes are not designed to melt and fuse with the metal being worked on. You will often see them used in TIG (tungsten inert gas) welding. These electrodes are semi-consumable, meaning they will burn away slightly after every weld. When the tip breaks off, the tungsten is sharpened and allowed to be used again.
You can repeat this process until the electrode is too small and completely burned away.
Why are Welding Electrodes Coated?
The main reason welding electrodes are coated is to protect them from reacting with the atmosphere. This is important because welding requires extremely high temperatures that could cause metals to react with the oxygen in the air, leading to several different problems.
The coating on welding electrodes is usually made from a mix of chemicals and inert ingredients like carbon and clay. As a result, these coatings may be referred to as fluxes or cored wire depending on the type of electrode being used.
Benefits of Electrode Coatings
The coating of welding electrodes provides several benefits.
Current Control
Firstly, the electrode coating allows the welder to control the current and voltage. This is important because it enables them to strike and maintain a stable arc.
Additionally, the coating makes it easy to adjust the voltage output when increasing or decreasing work thickness. This prevents overheating and ensures optimal welding quality for a number of different metals including carbon steel, stainless steel, and aluminum.
Shielding from the Atmosphere
Secondly, electrodes are coated to shield the weld pool from reacting with oxygen in the atmosphere. This reduces the chance of oxidation occurring, which can affect mental strength and other welding parameters.
In addition, electrodes are coated to prevent slag from being present on the surface of a weld bead after it has been removed from the arc. Slag is normally formed when flux becomes molten during a welding process. It acts as an insulator, protecting the molten metal from oxidizing.
Coating Selection
Lastly, electrodes are coated to suit certain welding processes. For example, stick electrodes are usually coated with flux-containing resin and mild elements like graphite or calcium carbonate.
While these coating types work well for protected metal arc welding (stick welding), they would not be suitable for the flux-cored welding process because they could contaminate the weld pool.
To avoid this, flux-cored electrodes are coated with chemical compounds like potassium ferrate. These components react to heat and oxygen in an arc to eliminate contaminants like carbon dioxide and nitrogen oxide, causing them not to form slag or other gases that can impair quality.
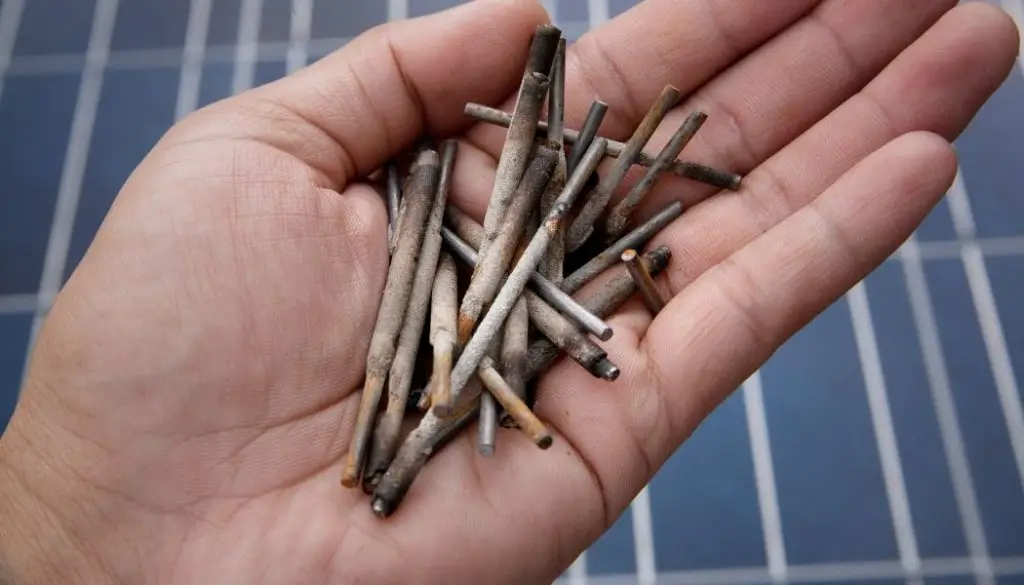
Different Types of Coating Material for Electrodes
Today, welding electrodes can be made from a variety of different materials. Each one is designed to provide the welder with certain benefits that suit specific welding processes. The most common electrode coatings are:
Cellulose Electrodes
Cellulose electrodes are made from inorganic binders like clay and contain inorganic filler materials like silica and alumina or organic fillers like cotton and wood.
These electrodes work well on AC weld joints that contain high levels of moisture, such as those found in electrical circuits or poorly insulated equipment. However, they provide lower welding currents than other types of electrode coatings and can become contaminated more easily so they need to be replaced more often.
Cellulose Electrodes are amazing for vertical welding positions and their slag is very thin and easy to remove.
Iron Powder Electrodes
Iron powder electrodes are formulated with a mixture of inorganic materials like silica, clay, and iron oxide.
These types of welding electrodes provide good welding characteristics and contain elements that would be easy to remove if they contaminated a weld pool.
Iron powder electrodes may be used on AC or DC applications, but should not be used on stainless steel because these components can reduce corrosion resistance.
Rutile Electrodes
Rutile electrodes are coated with synthetic material that contains titanium dioxide.
These components provide strong welding characteristics but may be expensive to use depending on the coating material.
Rutile Electrodes are ideal for welding aluminum because they provide good penetration and high fluidity, causing them not to form slag.
Aluminum Electrodes
Aluminum electrodes contain small quantities of elements like silicon, magnesium, zirconium, and chromium.
These types of welding electrodes work well on AC applications at low or high voltages but perform poorly when used with DC power sources because they create poor wetting action.
The presence of free silica may cause porosity problems if aluminum is welded on steel that does not have protective measures in place. However, adding iron oxide can solve this issue.
Iron Oxide Electrodes
Iron oxide electrodes are made from inorganic materials that contain iron, carbon, or hydrogen.
This electrode coating type provides strong welding characteristics and is the most common type used in general welding because it works well on both AC and DC applications.
Iron oxide electrodes are ideal for all types of ferrous materials, but they should not be used on aluminum.
How to Maintain Electrodes
Even though many electrode types can provide the welder with strong welds, they may become contaminated during the welding process. This means that to maintain good quality, electrodes must be cleaned every few hours or every hour depending upon how much contamination occurs. The following steps can simplify electrode maintenance:
- After you finish welding for the day, clean off any slag or oxidation from your work area around the electrodes. Then place back into their packaging container so they can be stored overnight.
- When you remove the electrodes from their package, inspect them for coating material that has flaked off. If any of it is found, clean off the electrode and replace it with a new one so no contaminated material get into your welding pool.
- If no contamination was found on either electrode, place both back into their container and store in an area where they will not get wet or used again before the next day’s work.
TIP: It is important to note that some welders prefer to use wooden boxes for storage because metal containers may rust over time and produce pockets of moisture that can cause electrodes to corrode during storage.