A welding position chart is a comprehensive guide outlining the positions in which a welder can operate. These include the flat (1G/1F/PA), horizontal (2G/2F/PC/PB), vertical (3G/5G), and overhead (4G/4F) positions. The chart helps welders understand the correct techniques, tools, and types of welds for each position.
Position | ASME Code | ISO 6947 Code | Description |
---|---|---|---|
Flat | 1G | PA | Welding is performed from the upper side of the joint, and the face of the weld is horizontal. |
Horizontal | 2G | PC | The axis of the weld is horizontal, but the weld face lies in a vertical plane. |
Vertical (Uphill) | 3G | PF | Welding is performed from bottom to top, and the axis of the weld is vertical. |
Vertical (Downhill) | 3G | PG | Welding is performed from top to bottom, and the axis of the weld is vertical. |
Overhead | 4G | PE | Welding is performed from the underside of the joint, and the face of the weld is horizontal. |
Pipe (Vertical) | 5G | PF/PG | The pipe is fixed in position, and the welder moves around it. |
Pipe (Fixed) | 6G | H-L045 | The pipe is fixed at a 45-degree angle, and the welder moves around and along it. |
Restricted (Fixed) | 6GR | H-L045 | Similar to 6G but with a ring restriction to simulate field conditions. |
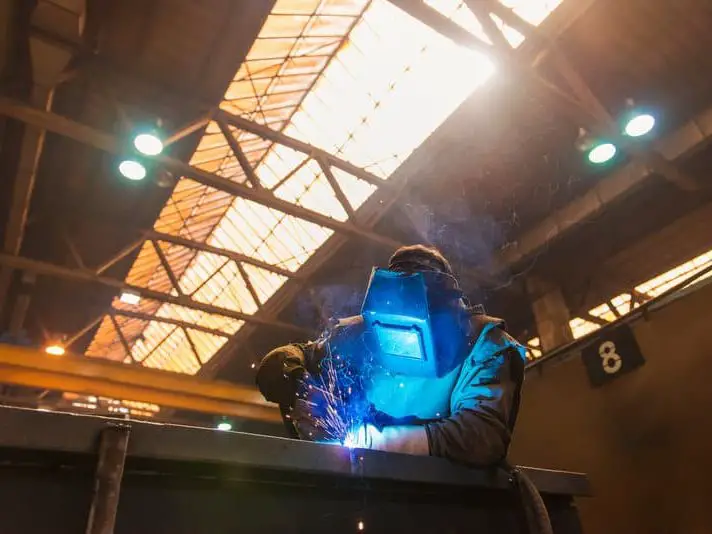
Table of Contents
Groove and Fillet Welding Positions
Regarding groove and fillet welds, the welding positions differentiate between flat, horizontal, vertical, and overhead positions. This helps us understand the appropriate technique, metal arc positioning, and the best welding rod type.
Pipe and Plate Welding Positions
The chart also distinguishes between pipe welding positions and plate welding positions. Pipe welding requires working around a fixed pipe in positions that may include vertical (uphill or downhill) and horizontal. In contrast, plate welding often takes place in a flat or horizontal welding position.
1G/1F/PA Position (Flat)
In my early days of welding, starting with the 1G position was a relief. The workpiece lays flat, and the weld runs along a horizontal axis, offering a comfortable position. But don’t be fooled; mastering the flat position requires keen attention to detail and the right balance of speed and angle.
The 1G or flat position is often the first step in any welder’s journey. The position lets the welder comfortably sit or stand while executing the weld on a horizontal plane. For newbies, it may take a few weeks to master, but patience is essential here.
Focus on consistency in your bead size and watch your travel speed. Going too fast or too slow can result in weak welds.
Regarding equipment, standard personal protective gear and a basic welding machine with suitable welding rods are enough to get started.
2G/PC Position (Horizontal)
The 2G position presents a bit more challenge. Here, the workpiece is vertical, but you weld on the top side of the joint, moving horizontally. It’s a tricky transition from 1G, but you’ll find your rhythm with practice.
The 2G position, where the joint is vertical, and the weld is performed horizontally, introduces a new level of complexity. On average, getting comfortable with this position might take a couple of months of practice.
It’s all about maintaining a steady hand and a consistent pace. Make sure to deposit enough metal at the start of the weld to prevent the formation of undercut.
As for equipment, besides the regular welding gear, some welders prefer to use a pipe stand for support when they start with 2G welding.
2F/PB Position (Horizontal)
The 2F position is a fillet weld where the workpiece is positioned horizontally. When I was apprenticing, this position was my nemesis. It’s easy to start fast and end up with inconsistent welds. But once you master this, the rest feel like a piece of cake!
The 2F position is a fillet weld with the workpiece positioned horizontally. This position can take several weeks to months to master, requiring a unique blend of control and consistency.
Ensure to maintain the correct work angle and hold a short arc length.
No additional equipment is required for this position, but a work clamp might help steady the workpiece.
3G Uphill/PF Position (Vertical)
Now, this is where things get more challenging. The 3G position requires vertical uphill welding, moving the welding rod upwards. The metal’s heat pulls the weld downward, which taught me an important lesson: working against gravity can be tough, but patience is key.
The 3G position is vertical uphill welding, which can take up to several months to master. This position is more challenging as it involves working against gravity.
The key is maintaining a short arc length and using a slight side-to-side or triangular weaving motion.
For this position, welders may want to invest in a welding lens with higher shade numbers since the weld pool tends to be brighter in vertical welding.
3G Downhill/PG Position (Vertical)
The 3G downhill position is the flip side, requiring a vertical downward movement. With gravity on your side, controlling the speed of the weld becomes the real challenge here. It’s an adrenaline rush, fighting to keep the speed in check!
Mastering this position might take as long as mastering uphill due to the challenge of controlling speed.
Maintain a slightly longer arc length and move quickly to prevent overheating and burn-through.
Equipment needs remain the same as with 3G Uphill.
4G/PE Position (Overhead)
Overhead welding or the 4G position can be a bit daunting initially. The workpiece is beneath you, and you weld from the underside. I found it intimidating back in the day, but once you overcome the fear and trust your skills, it becomes a routine affair.
This is a bit more challenging due to the need to deal with falling molten metal, which can take several months to get used to.
It’s all about getting comfortable with the overhead position. Keep your travel speed steady, and remember to clear away slag after each pass.
Regarding equipment, a welding helmet with an auto-darkening feature and a fire-resistant jacket is highly recommended for overhead welding.
4F/PD Position (Overhead)
The 4F position is an overhead fillet weld. I remember the day I first attempted it; weld spatter flying toward me was a real test of my resolve. But now, it’s just another day at the ‘office.’
Mastering this position can take a few months to a year, depending on how often you practice.
Start with a tight, consistent weave pattern and focus on control to prevent sagging or rollover of the weld metal.
Equipment requirements remain the same as with the 4G position.
5G Uphill Position (Vertical)
The 5G position was my first introduction to pipe welding. Here, the pipe is vertical, and the welder moves around it, welding uphill. It’s a game of skill, testing your hand-eye coordination and stamina.
This advanced welding position takes 4-8 months to excel at.
Good positioning of your body and staying steady are crucial. Consistently practice moving around the pipe while maintaining the right welding angle.
In addition to your standard welding kit, you’ll need pipe stands or pipe clamps to hold the pipe in a vertical position securely.
5G Downhill Position (Vertical)
Like 5G uphill, the 5G downhill position involves moving around a vertically fixed pipe, but this time you’re welding downwards. It’s a swift dance around the pipe, simultaneously controlling your speed and battling gravity.
Learn to control your speed. Gravity will tend to speed up your progress since you’re welding downhill. Also, ensure to control the puddle size for even welds.
Your basic welding kit and pipe clamps or stands will serve you well here.
6G Uphill/Downhill Position
The 6G position was my final hurdle in pipe welding. With the pipe fixed at a 45-degree angle, welding involves moving both around and along. It’s a true test of a welder’s skill, testing your ability to adapt and adjust to the different angles and positions.
It’s all about maintaining the right body positioning and movement while adapting to the changing angles. Keep practicing different transitions between welding positions. Along with your standard welding equipment, adjustable pipe stands will be beneficial to achieve and maintain the 45-degree angle.
6GR Test
The 6GR test is a step up from the 6G position. It has an additional ring restriction that simulates field conditions, making the task even more challenging. The day I passed my 6GR test was one of my proudest moments as a welder.
Practice with different pipe diameters and thicknesses to adapt to the varying field conditions you might encounter. Also, practicing under a mentor or experienced welder can provide valuable feedback.
The standard welding kit remains essential. In addition, you’ll need a practice setup that includes a ring for restriction to simulate the field conditions of the 6GR test.
This is an expert-level position skill that will take 6-12 months, plus additional time for test preparation.