Porosity is a term used in welding to describe the presence of gas pockets in the weld metal. These gas pockets can cause several problems, including reduced strength and reduced resistance to corrosion. Porosity can be caused by various factors, including poor welding technique, contamination of the welding material, and the use of incorrect welding electrodes.
Welding can be a complicated process with many variables affecting the final product’s quality. Porosity is one such variable worth understanding before you start welding on your next project.
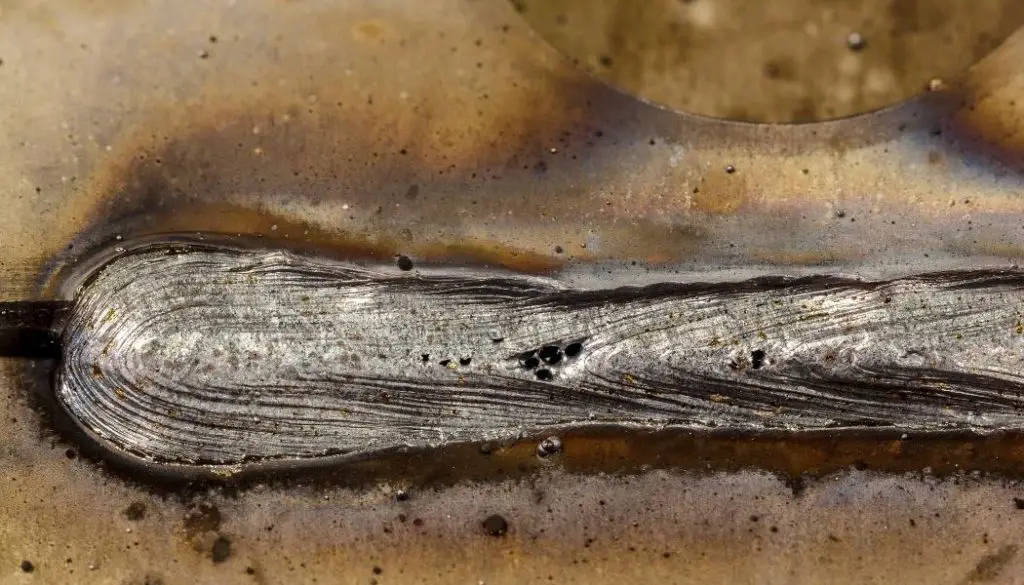
Table of Contents
What is Welding Porosity?
Porosity is generally, a form of metal contamination. It is a defect that can occur in welds. It is caused by the formation of air pockets, gas pockets, or other voids in the weld metal due to hydrogen, oxygen, or nitrogen gases.
Porosity is a common problem and can cause a number of problems such as weakening the structure of the overall weld, injuring people, and can ruin the aesthetics of the workpiece. Additionally, it can also destroy your reputation as a welder.
There are several ways to reduce the risk and remove it properly, which we will explain further in this post. Let’s start by explaining the different types of porosity in welding first.
Different Types of Porosity in Welding?
Several types of porosity can occur in welds, including:
Distributed Porosity
Distributed porosity is porosity that is spread evenly throughout the weld. It is usually caused by contamination of the welding material or by the use of incorrect welding electrodes.
Surface Porosity
Surface porosity is porosity that occurs on the surface of the weld. It is usually caused by poor welding techniques or by the use of incorrect welding electrodes.
Wormholes
Wormholes are a type of porosity that occurs in welds in the form of long, cylindrical holes. The use of incorrect welding electrodes usually causes it.
Crate Pipes
Crate pipes porosity is a type of porosity that occurs in welds in the form of small, square-shaped holes. The use of incorrect welding electrodes usually causes it.
Inclusion Porosity
It is porosity that occurs in isolated pockets within the weld metal. It is usually caused by dirt or foreign objects getting trapped in the weld joint.
Gas Porosity
It is porosity caused by the formation of gas pockets in the weld metal. It is usually caused by a poor welding technique, contamination of the welding material, or the use of incorrect welding electrodes.
Arc Blow Porosity
It can be a serious problem in TIG welding. It is caused by the arc movement across the weld puddle, which creates a draft that sucks gas pockets into the weld.

What Causes Porosity In Welding?
There are several factors that can cause porosity in welding. Some of the most common causes include:
1. Poor Welding Technique
Welders who are not experienced or who do not have the proper skills can cause porosity in their welds by using poor welding techniques. This includes incorrect welding procedures, poor welding posture, and poor use of welding equipment.
2. Contamination of the Welding Material
Contamination of the welding material can cause porosity in welds by introducing dirt or foreign objects into the weld joint. This can weaken the weld and make it susceptible to failure. In addition, it can also cause the weld to be less aesthetically pleasing.
3. Incorrect Welding Electrodes
The use of incorrect welding electrodes can also cause porosity in welds. This is because some welding electrodes are more prone to the formation of porosity than others. In addition, if the welding electrodes are not properly matched to the type of metal being welded, it can also lead to the formation of porosity.
4. Welding in Dirty or Dusty Environments
Welding in dirty or dusty environments can also cause the formation of porosity in welds. This is because the dirt and dust can get trapped in the weld joint and create pockets of air that will later become gas pockets in the weld metal.
5. Poor Welding Posture
Poor welding posture can also lead to the formation of porosity in welds. This is because it can cause the welder to be in a bad position to control the weld puddle, which can lead to the formation of gas pockets. In addition, it can also lead to poor weld quality.
6. Welding in Humid or Wet Environments
Welding in humid or wet environments can also cause the formation of porosity in welds. This is because the humidity can cause the welding material to become damp, leading to gas pockets forming. Additionally, it can also cause the weld joint to rust, which can weaken the weld.
7. Arc Blow
Arc blow is a problem that can occur in TIG welding. It is caused by the arc movement across the weld puddle, which creates a draft that sucks gas pockets into the weld. This can cause serious problems with the weld quality and should be avoided if possible.
8. Slag Inclusions
Inclusions of slag or other foreign objects in the weld joint can cause porosity in welds. This is because the inclusion of these objects can create air pockets in the weld metal. These air pockets can then become gas pockets in the weld and lead to the formation of porosity.
How to Prevent Porosity in Welding?
These are a few most common and effective ways in preventing porosity:
1. Clean Material Before Welding
One of the best ways to prevent porosity in welding is to clean the material before welding it. This means removing all the paint, dirt, dust, and slag from the surface of the metal. In addition, it is also important to use the correct welding electrodes for the type of metal being welded.
2. Weld in a Clean Environment
Another way to prevent porosity in welding is to weld in a clean environment. This means avoiding welding in dirty or dusty environments, and living in a damp environment if possible.
3. Use the Correct Welding Technique
The best way to avoid porosity in welding is to use the correct welding technique. This includes using the correct welding procedures, welding posture, and welding equipment. In addition, it is important to select the correct welding electrodes for the type of metal being welded.
4. Weld in a Vacuum Chamber
One way to completely avoid porosity in welding is to weld in a vacuum chamber. This will ensure that there is no contamination of the welding material and that the weld joint is clean and free of any foreign objects.
5. Use Correct Shielding Gas
Arc Blow can be reduced by using a shielding gas that is compatible with the type of metal being welded. Additionally, TIG welding can be improved by using a tungsten electrode that is ground to a point. This will help to create a more stable arc.
Finally, porosity in welds can also be reduced by using a back purge gas. This will help to keep the weld joint clean and free of any contamination.
How Do You Fix Porosity?
If the porosity is found in a weld, several ways can help to fix it. These include:
- Removing the weld and re-welding it can fix porosity.
- If the porosity is caused by a slag inclusion, the inclusion can be removed and the weld can be repaired.
- Patching the weld with a plate can also fix porosity.
- Retesting the weld to make sure that it is free of porosity.
- Welding over the porosity to fill it in can fix it.
- Paint or seal the weld to hide the affected area.
- Filling the porosity with a weld filler rod can fix it.
- Grinding the weld can remove the porosity as well.
Each of these methods has its own pros and cons, and the best method will depend on the situation. However, all of these methods should be used with caution, as they can all damage the weld joint.
Related Questions
Can you weld over porosity to fill it?
Welding over the porosity to fill it in is a common method of fixing this problem. This involves welding over the affected area and filling in the porosity with the weld metal. This will help to restore the strength and appearance of the weld joint. However, this should be done with caution, as it can damage the weld joint.
How much porosity is acceptable in a weld?
There is no definitive answer to this question, as the amount of porosity that is acceptable will vary depending on the application. However, most welders aim for less than 1% porosity in a weld. Anything more than this can lead to serious problems with the quality of the weld and should be avoided if possible.
Can porosity be prevented permanently?
There is no definitive answer to this question, as porosity can be caused by a variety of factors. However, many of the methods listed above can help reduce the amount of porosity present in a weld. By using these methods, it is possible to achieve a weld that is free of porosity.
Can we paint the weld to hide porosity?
Yes, painting or sealing the weld can help to hide the affected area. This is a common method of fixing porosity in a weld, and it is relatively easy to do. However, this should not be considered a permanent fix, as the paint or sealant will eventually wear off.