As a beginner, you should start with E6010 and E6011 stick welding electrodes.
Stick welding, or shielded metal arc welding (SMAW), is a versatile and widely-used welding process suitable for various applications and materials. At the heart of stick welding are the electrodes – consumable materials that provide the arc, filler metal, and shielding gas for the welding process.
In this article, I’ll provide an introduction to stick welding rods, including their classification, characteristics, and applications. I’ll also discuss some key factors to consider when selecting the right stick welding rod for your project.
Table of Contents
Different Types of Welding Rods
Many types of stick welding rods, or electrodes, are used for shielded metal arc welding. These electrodes are classified according to the American Welding Society (AWS) classification system, which uses a numbering system to identify the electrode type and its characteristics.
The first two digits of the AWS classification system indicate the tensile strength of the electrode. The third digit indicates the position in which the electrode can be used. The fourth and fifth digits indicate the coating type and current used with the electrode.
Some common types of stick welding electrodes include:
- E6010 electrodes – Deep-penetration electrodes used for welding in horizontal and vertical positions. They have a deep penetrating arc that can penetrate through tough materials and provide a strong, high-quality weld.
- E6011 electrodes – Smooth-running electrodes used for welding in horizontal, vertical, and overhead positions. They have a smooth, stable arc that is easy to control and provides a smooth, even weld bead.
- E6013 electrodes – All-purpose electrodes used for welding in all positions. They have a smooth, stable arc that is easy to control and provides a good balance of penetration and arc stability.
- E7014 electrodes – Low-hydrogen electrodes used for welding in horizontal and vertical positions. They have a deep penetrating arc that provides a robust and high-quality weld and are suitable for welding in demanding conditions, such as high temperatures or high humidity.
There are many different types of stick welding electrodes, and each type has its own unique characteristics and applications. As a beginner, it is best to start with a simple, all-purpose electrode, such as an E6010 or E6011. As you gain experience, you can experiment with different types of electrodes to find the one that works best for your project’s needs.
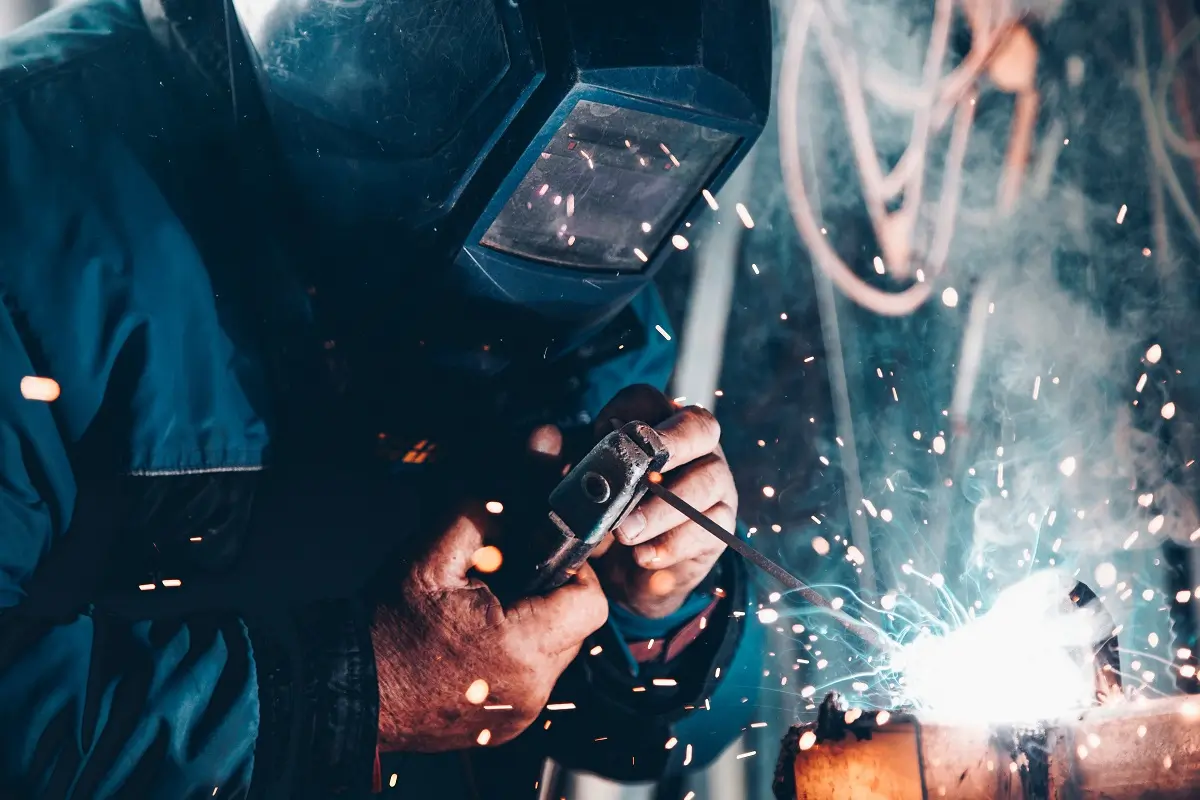
Best Stick Welding Rod for Thin Mild Steel
The best stick welding rod for thin mild steel is an E6011 electrode. This has a smooth, stable arc that is easy to control and provides a smooth, even weld bead. It is alsosuitable for welding in horizontal, vertical, and overhead positions, making it ideal for welding thin or out-of-position materials.
Best Stick Welding Rod for Thick Mild Steel
The best stick welding rod for thick mild steel is an E6010 electrode. This electrode has a deep penetrating arc that can penetrate through tough materials and provide a strong, high-quality weld. It is suitable for welding in horizontal and vertical positions, making it ideal for welding thick, dirty, or rusty materials.
What Amperage for Stick Welding?
The amperage setting on a stick welder will depend on several factors, including the material’s thickness.
As a general rule of thumb, you should use an amperage setting in the range of 70-150 amps for welding mild steel with a stick welding process. For welding mild steel that is 1/8-inch thick, you could use an amperage setting of 70-90 amps with a 1/8-inch electrode or 90-120 amps with a 3/32-inch electrode.
Start with a low amperage setting and gradually increase it until you achieve the desired penetration.
What Thickness Welding Rod Should I Use?
The thickness of the stick welding rod will depend on several factors, including the material thickness and the type of electrode.
Generally speaking, the thicker the base metal, the thicker the welding rod should be. Here’s a rough estimate comparison between the base material and the welding rod:
Rod Size | Amperage Range | Plate Thickness |
1/16 to 5/64 inch | 20 – 45 | < 3/16 inch |
3/32 inch | 40 -125 | 1/4 inch |
1/8 inch | 75 – 190 | 1/8 to 3/8 inch |
5/32 inch | 105 – 250 | 1/4 to 3/4 inch |
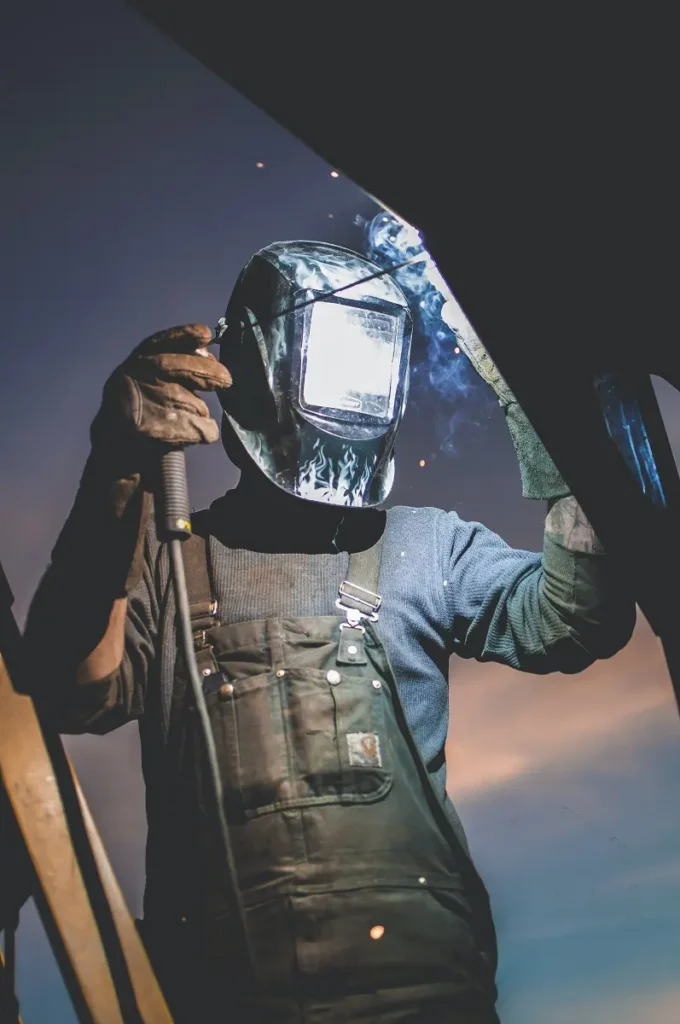
How Do I Stop Welding Rods from Sticking?
You can take several steps to prevent stick welding rods from sticking to the base metal during the welding process, including:
- Maintain the correct distance between your welding rod and the weld pool. I recommend keeping a 1/8 inch gap.
- Use the correct electrode for the application. Using the correct electrode for the application can minimize the risk of sticking and ensure that the electrode provides the right penetration and arc stability.
- Use the correct amperage setting. The amperage setting on a stick welder determines the heat and penetration produced by the welding arc. If the amperage setting is too high, the electrode may stick to the base metal, while if the amperage setting is too low, the electrode may not provide enough penetration and arc stability.
- Use the correct welding technique. Stick welding requires specific skills and techniques to produce high-quality welds. For example, when welding in the vertical position, you should use a “drag” technique, where the electrode is pointed downward and moved along the base metal to prevent the electrode from sticking to the base metal. Similarly, when welding in the overhead position, you should use a “push” technique, where the electrode is pointed upward and moved along the base metal to prevent the electrode from sticking to the base metal.
How to Store Welding Rods
To store stick welding rods, properly, you should follow these steps:
- Keep the electrodes in their original packaging. Stick welding electrodes are typically packaged in moisture-resistant containers, such as cardboard tubes or plastic containers, to protect them from moisture and contamination. Do not open the packaging until you are ready to use the electrodes.
- Store the electrodes in a dry, well-ventilated area. Stick welding electrodes are sensitive to moisture and contamination and can become damaged or unusable if they are exposed to moisture or other contaminants.
- Avoid exposing the electrodes to extreme temperatures. Stick welding electrodes are sensitive to temperature changes and can become damaged or unusable if exposed to extreme temperatures.
- Keep the electrodes away from other welding materials. Stick welding electrodes are sensitive to contamination and can become damaged or unusable if exposed to other welding materials, such as flux or slag.