The 6010 welding rod offers deep penetration, strong welds, and is great for pipe welding, but requires a DC power source. The 6011 rod provides similar penetration and performance but can be used with both AC and DC power sources, making it more versatile for various welding machines and situations.
In this comparison, I will outline the main differences and similarities between these two welding electrodes to help you make an informed decision for your welding projects.
Table of Contents
Quick Summary
6010
- High cellulose sodium coating
- DC+ only
- Deep penetration, stable arc
- More tenacious slag
6011
- High cellulose potassium coating
- AC, DC+, DC-
- Forceful arc, slightly less penetration, better at burning through contaminants
- Easier slag removal
Composition and classification
The 6010 and 6011 welding rods are mild steel electrodes classified as AWS E6010 and AWS E6011, respectively. The classification system is similar, with the first two digits representing the tensile strength of the deposited weld metal (60,000 psi), the third digit denoting the welding position (1 for all positions), and the last digit indicating the coating type and current compatibility.
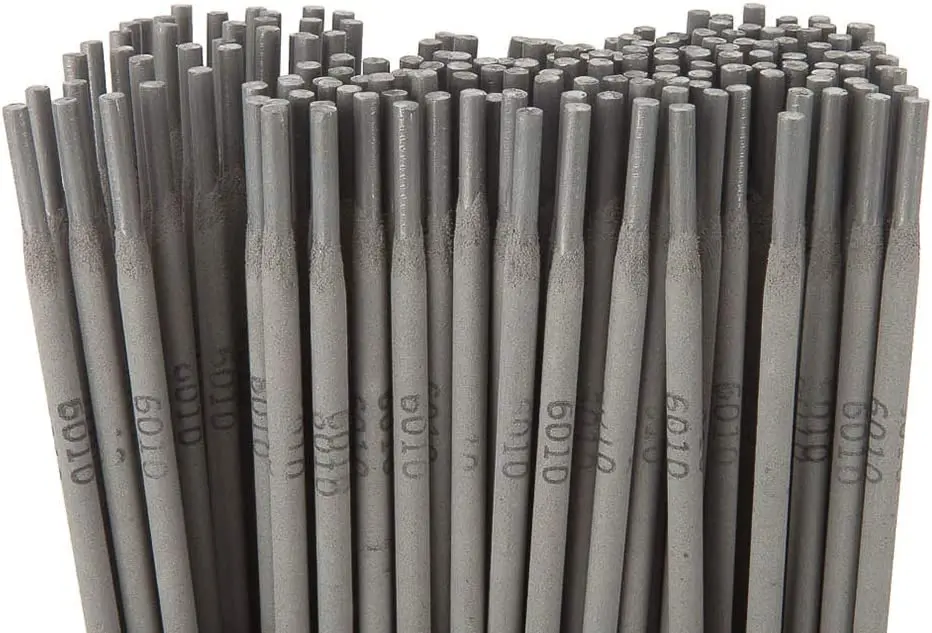
Coating and current compatibility
The primary difference between the 6010 and 6011 electrodes lies in their coatings and current compatibility. The 6010 electrode has a high cellulose sodium coating, making it compatible with direct current electrode positive (DCEP, or DC+) only.
The 6011 electrode features a high cellulose potassium coating, which allows it to be used with alternating current (AC), direct current electrode positive (DCEP, or DC+), and direct current electrode negative (DCEN, or DC-). This makes the 6011 more versatile regarding welding machines and power sources.
Applications
The 6010 and 6011 electrodes are suitable for various applications, such as general fabrication, pipelines, shipbuilding, and maintenance work. However, the 6010 is often preferred in pipeline welding and other applications requiring deep penetration and high-quality welds.
The 6011 electrode is more commonly used in maintenance and repair, especially when AC welding machines are involved.
Welding positions
Both 6010 and 6011 welding rods are designed for use in all positions—flat, horizontal, vertical, and overhead—making them versatile for various welding projects.
Penetration and arc stability
The 6010 electrode typically provides deep penetration and a more stable arc, making it suitable for applications requiring excellent weld quality and strong joint penetration.
The 6011 electrode offers a more forceful arc and slightly less penetration, which can be advantageous for applications involving dirty or rusted materials, as it can help burn through contaminants.
Slag removal
There is a notable difference in the slag removal experience between the 6010 and 6011 electrodes. The slag created by the 6010 electrode tends to be more tenacious and adherent, which means it might require additional effort to clean and remove after the welding is complete. This could need a chipping hammer or a wire brush to eliminate the slag, ensuring a clean and neat weld appearance.
The slag produced by the 6011 electrode is generally less stubborn and easier to remove. This translates to a quicker cleanup process, as the slag can be detached with minimal effort, allowing the welder to move on to the project’s next stage more efficiently.

Amperage
The amperage range for 6010 and 6011 welding electrodes depends on the rod’s diameter. The following are general amperage guidelines for different diameters of these electrodes:
6010 Welding Rod:
- 1/16 inch: 20-50 Amps
- 3/32 inch: 40-85 Amps
- 1/8 inch: 75-125 Amps
- 5/32 inch: 110-165 Amps
- 3/16 inch: 150-220 Amps
6011 Welding Rod:
- 1/16 inch: 20-50 Amps
- 3/32 inch: 40-85 Amps
- 1/8 inch: 75-125 Amps
- 5/32 inch: 110-165 Amps
- 3/16 inch: 150-220 Amps
Moisture Resistance
Both 6010 and 6011 welding rods are cellulose-based electrodes. While they are not as sensitive to moisture as low-hydrogen electrodes like the 7018, proper storage and handling are still essential to maintain their performance.
Moisture resistance between the 6010 and 6011 electrodes is relatively similar, as both are cellulose-based electrodes. However, due to their different coatings (high cellulose sodium for 6010 and high cellulose potassium for 6011), there may be minor variations in their moisture absorption characteristics.
To ensure optimal welding performance, it’s recommended to store 6010 and 6011 electrodes in a cool, dry place, preferably in a sealed container or electrode storage cabinet, to minimize the risk of moisture absorption.
These rods do not typically require a rod oven like low-hydrogen electrodes, exposing them to moisture for prolonged periods can still cause welding issues, such as porosity and reduced mechanical properties.
Abrasion Resistance
Regarding abrasion resistance, the 6010 and 6011 welding rods are not specifically designed for high wear resistance applications, as both are mild steel electrodes used primarily for general fabrication and repairs.
Multiple factors, including the filler metal composition, base material, and welding technique, determine a weld’s abrasion resistance. Neither the 6010 nor the 6011 electrodes contain alloying elements that would significantly improve the abrasion resistance of the weld deposit.
Conclusion
The choice between the 6010 and 6011 welding electrodes largely depends on your welding machine’s power source and the specific requirements of your welding project.
If you have a DC-only welding machine and need deep penetration and high-quality welds, the 6010 electrode may be a better choice.
However, if you need a more versatile electrode compatible with AC and DC welding machines, the 6011 electrode would be more suitable.