6010 vs 6013 welding rods differ mainly in penetration, tensile strength, and coating. 6010 rods are suited for open root welding, offering deep penetration, while 6013 rods are ideal for clean, smooth welds on thin metals.
Table of Contents
What is 6010 Welding Rod Used For?
6010 welding rods are the unsung heroes when dealing with challenging conditions. They’re often my weapon when I face tasks involving rusty, dirty, or painted surfaces, requiring deep penetration.
For instance, in pipeline welding, a sector I’ve worked in extensively, the 6010 welding rod is renowned for its ability to “dig” through almost any material. This ability to produce deep, solid welds makes it highly suitable for high-stress applications, where robustness is paramount.
But it’s not all about tough jobs for the 6010 rods. Their all-position capability allows them to be used in various welding scenarios. You can use them for flat, horizontal, vertical, or even overhead welding – they handle it all.
Despite their strength, it’s important to note that the 6010 welding rods may not always yield the prettiest welds. Their aggressive nature can lead to somewhat rough and irregular weld beads. But, as I’ve learned, aesthetics aren’t everything regarding strong, reliable welds.
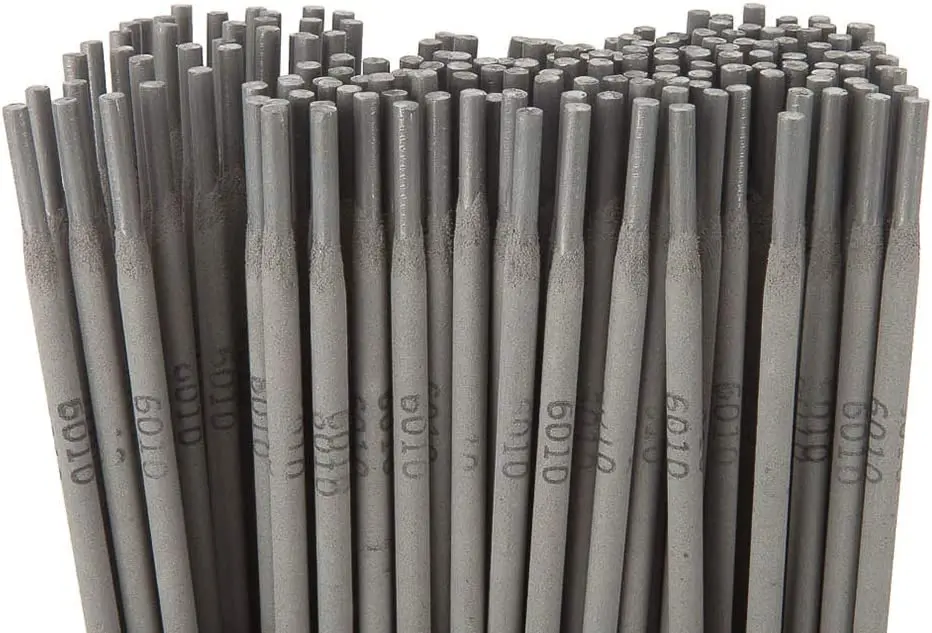
When Not to Use 6010 Welding Rod
Despite their strengths, 6010 welding rods have their limitations. One scenario where I tend to steer clear of them is when dealing with light gauge sheet metals. While beneficial in many circumstances, their deep penetration abilities can be overkill on thin materials, causing undesirable burn-throughs.
Similarly, if the appearance of the weld is a significant factor, 6010 might not be the best choice. Due to their characteristics, achieving a clean, smooth finish with a 6010 rod requires considerable skill and experience.
What is a 6013 Welding Rod Used For?
The 6013 welding rods are often my first choice when looking for a neat, smooth weld. They’re particularly handy when working on thin or medium gauge mild steel, where the goal is to maintain the metal’s integrity without compromising the weld’s quality.
I often lean towards 6013 rods for general repair work or fabrication tasks. Their versatility across all positions, combined with easy slag removal, often results in welds that are not only structurally sound but also aesthetically pleasing. The end product with a 6013 rod often has a fine ripple effect that gives it a professional finish.
The user-friendly nature of 6013 welding rods makes them an excellent choice for beginner welders. They are forgiving and can help newcomers develop their skills while still achieving good quality results.

When Not to Use 6013 Welding Rod
However, 6013 rods are not without their drawbacks. When a situation calls for deep penetration – for instance, when working on rusty, dirty, or heavily painted surfaces – 6013 welding rods may not be up to the task. Their lighter penetration level means they may not adequately penetrate and fuse these more challenging surfaces.
I tend to opt for the 6010 or even 7018 welding rods in such cases. These rods offer deeper penetration and can cut through the contaminants to produce a strong, reliable weld. As with many things in welding, it’s about choosing the right tool for the job.
Different Properties Between 6010 and 6013 Welding Rods
Tensile Strength
Tensile strength, measured in pounds per square inch (PSI), describes how much load a weld can take before it breaks. In this context, 6010 and 6013 welding rods exhibit roughly similar tensile strengths of about 60,000 PSI. This high strength means welds produced with either rods can withstand considerable stress before failure.
But as I’ve learned in my years of welding, it’s not just the tensile strength number that counts. The specific type of metal being welded and the project’s requirements also significantly influence rod choice. For instance, for more rugged welding applications like pipe welding, you might prioritize rods like the 6010 that can produce welds with deep penetration and high tensile strength.
If you’re dealing with thinner, more delicate materials that require less penetration and more visual appeal, a 6013 welding rod, despite having a similar tensile strength, might be more appropriate due to its ease of use and medium to light penetration characteristics.
Polarity
The term polarity in welding refers to the electrical property of the welding arc, and it’s a critical factor in welding. DCEP (Direct Current Electrode Positive), DCEN (Direct Current Electrode Negative), and AC (Alternating Current) are all types of welding currents, each with their unique applications.
6010 welding rods typically use DCEP, where the electrode is the positively charged component in the electrical circuit. DCEP offers deep penetration, making it perfect for situations where you must weld through contaminants like rust or paint.
The 6013 welding rods are more adaptable and can work with AC, DCEP, and DCEN. Their versatility makes them an excellent choice for home and professional applications. The flexibility in polarity choice with 6013 rods also means they can be adjusted for different penetration and cleaning action levels, allowing for smoother and more visually appealing welds.
Penetration
When we talk about penetration in welding, we’re referring to how deeply the welding arc’s heat penetrates the base metals. As with the 6010 welding rods, deep penetration means the weld fuses more of the base metal, making it ideal for thicker materials and high-stress applications.
I’ve used 6010 rods in scenarios where deep penetration was needed, like on rusty or dirty surfaces, or in out-of-position welds. The aggressive nature of 6010 rod allows it to cut through these contaminants and deliver a solid, reliable weld, albeit not always the most visually pleasing.
On the flip side, 6013 rods offer medium to light penetration. This trait makes them a good choice when welding thin metals, where too much penetration could lead to burn-through. Their lighter penetration level also allows for a smoother, more aesthetically pleasing weld bead, which I’ve found valuable when working on visible welds or in situations where clean, neat welds are preferred.
Conclusion
Choosing between 6010 vs 6013 welding rods depends on your specific welding needs. If you’re looking for a welding rod that provides deep penetration, then 6010 is your go-to rod.
However, if you’re working with thin metal or seeking a smooth, visually pleasing weld, then 6013 is more suitable. But remember, the right choice also depends on the welder’s skill.