Spot and MIG welding are two different methods for joining materials using heat. They both use electricity as a source of heat. Each process has its own benefits and uses.
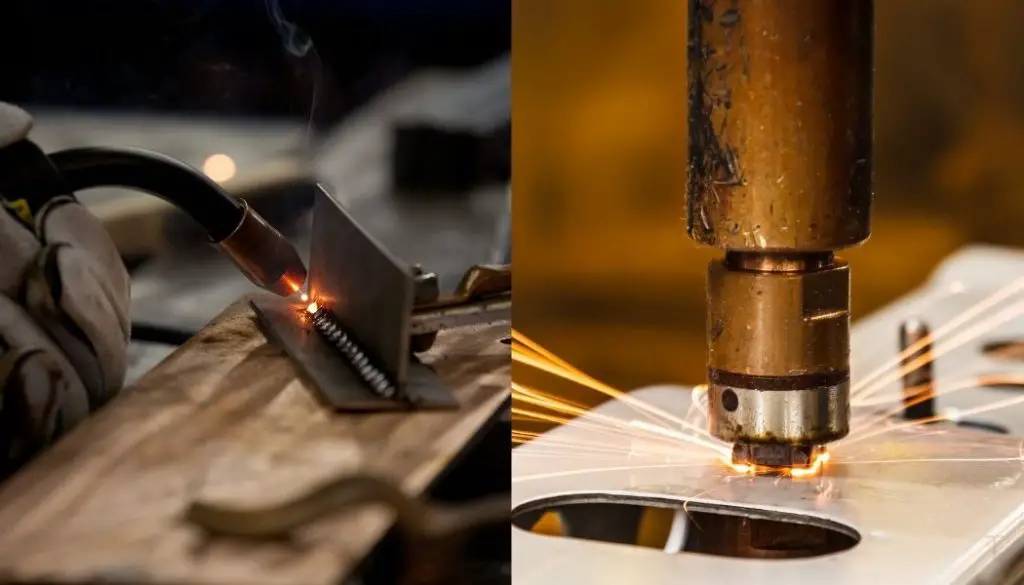
In this post, you will learn more about these two popular and interesting welding techniques in detail and their differences.
Table of Contents
What is MIG Welding
MIG stands for Metal Inert Gas, which means an electric arc is used to create the weld area, but there is no flow of welding gas through the wire electrode holder.
The filler metal is fed from a separate source and has a larger diameter than the wire electrode. This will let the MIG welding machine be able to use thicker wires for welding.
The process is different from the traditional arc and TIG welding because the material does not get melted during welding.
The base metal and filler metals are heated up, but they do not melt together. Instead, a very small area of each metal is melted, and the two are then pressed together. This creates a weld that is very strong and has a smooth finish.
TIP: Read my MIG welding tips.
Where do you use MIG welding technique?
MIG welding is mainly used for welding aluminum, magnesium, and copper alloys. It can also be used on steel, but it is not as strong as the welds created by other methods.
You will also see mass production lines using MIG welding machines because they are easy to operate and can create consistent welds.
What is Spot Welding
Spot welding uses two electrodes to create a weld. The electrodes are placed opposite each other on the material to be welded, and an electric current is passed through them.
This creates an electric arc that heats up the material. The weld is created when the two pieces of metal are pressed together.
Where to use spot welding?
Spot welding is often used to weld thin pieces of metal together. It is a faster and more efficient way to weld than using MIG welding, and it does not require as much equipment.
However, it can only be used on materials that are of similar thickness. If the material is too thick, the electrodes will not be able to create a weld because the heat is too great.
Spot welding is used in several industries such as automotive, packaging, and construction.

Differences Between MIG and Spot Welding?
There are a few main differences between MIG and spot welding.
Wire vs Electrode
When you MIG weld, you will need to continuously feed a wire into a welding gun. These wires can be bought in a range of different diameters, depending on the project you are working on.
On the other hand, spot welding uses an electrode to create the weld. This electrode is generally thicker than a wire, meaning it can create a stronger weld.
Pulse vs Constant Current
MIG welding uses a pulse current, which is applied for a short period of time, and then the machine stops the flow of electricity. The current needs to be re-applied in order to weld another section.
Spot welding, on the other hand, uses a constant current. The current flows continuously through the electrode while you hold it in place against the material to be welded.
DC and AC Current
MIG welding can use either direct current (DC) or alternating current (AC). On the other hand, spot welding uses only direct current.
Welding Gas
MIG welding uses a shielding gas to protect the weld from contamination. The most common type of gas used is carbon dioxide and argon but you can also use helium in addition.
Spot welding does not use any gas during the welding process.
Filler Metal
MIG welding uses a separate piece of filler metal that is fed into the weld. This filler is melted by the electric arc, which then joins with the base metal to create the weld.
Spot welding uses the material itself as the filler metal. The two pieces of metal are heated up and then pressed together to create the weld.
Welding Speed
MIG welding is a lot faster than spot welding. This is because the machine can weld multiple sections at once, whereas you can only weld one section at a time when you spot weld.
Welding Positions
MIG welding can be done in all positions – horizontal, vertical, and overhead, while spot welding can only be done in the flat position.
Cost
MIG welding is more expensive than spot welding because it requires more specialized equipment.
However, it will probably be cheaper to use MIG welding than spot welding if you are undertaking a large project.
Which Welding Process is Best For You?
MIG welding is ideal for projects that require a lot of welding, or where the user needs more control over the weld. When searching for best MIG welder, check Lincoln Electric, which I use and like the most.
However, Spot welding is amazing when you want to quickly and easily weld two pieces of metal together. It’s also great starting point for someone who is interested in welds, and it also covers the basics of welding pretty well. Check Stark spot welder which I really love.
How to Spot Weld
A spot welder is very easy to use!
- Clamp your metal -Start with clamping the two pieces of metal that you want to weld together. Make sure that the surfaces are clean and free of any oils or contaminants.
- Set the electrode – Next, set the electrode on the metal and make sure that it is in contact with both pieces of metal.
- Turn on the machine – Turn on your spot welder and wait until it’s up to temperature.
- Start Welding – Once the unit is up to temperature, simply press the electrode against one of the two pieces of metal and squeeze the trigger on your spot welder. The electricity will create a short circuit between the two pieces of metal and create a weld that will hold them tightly together.
- Remove and inspect the weld – Wait until the spot welder shuts off and then remove the electrode. You should be able to see a bead of metal on your two pieces which will have fused them together…in a way that’s a lot more secure than glue! 🙂
Related Questions
Can you turn a MIG welder into a spot welder?
Turning a MIG welder into a spot welder is possible, but it takes a bit of modification. You can do this by using a special MIG spot welding nozzle.
Can you spot weld aluminum?
Yes, it’s perfectly possible to spot weld aluminum but a lot of currents is needed.
You will need also 3 phase spot welder to get the job done properly.
Can you spot weld stainless steel?
Yes, you can spot weld stainless steel too. Make sure you use Copper-cobalt-beryllium electrodes, as these are the best type for welding this type of metal.
What metals Cannot be spot welded?
Spot welding can be used on a variety of metals, but some cannot be welded using this technique such as Brass, copper, zinc, and lead.
If you try to spot weld these materials, you will end up with a weak weld that is likely to fail.
Which is More popular? (MIG or Spot)
MIG welding is generally more common than spot welding, especially in industrial settings. However, if you are looking for a quick and easy way to weld two metal pieces together, then MIG welding is not the right technique to use.
Instead, try out some spot welding! It will be easier (and cheaper).