Gas welding uses a shielding gas to protect the weld from the atmosphere, while flux core welding doesn’t have an external gas but includes flux within the hollow electrode. Gas welding needs surfaces to be extremely clean, while flux core can handle some surface debris. Gas welding is better suited for thin materials, while flux core welding is better suited for outdoor use.
So, you are considering purchasing your first wire welding machine and want to know a bit more about them. The bright-colored little boxes are not all that complicated, but there are a few questions you need to answer before plunking down the cash.
Nothing is worse than an expensive little machine collecting dust in the corner of your garage because it wasn’t really what you needed.
We will step you through several options to help you determine which machine and wire type is most likely the best choice for you today and soon.

Table of Contents
Difference Between GMAW and FCAW
School is still out for me regarding the acronyms applied to the various welding methods designated by the American Welding Society. I’m not convinced they are helpful; some may find them confusing initially.
But, they are inescapable in the welding world. We will only be dealing with the two associated with wire welding for this article.
What is GMAW Welding?
GMAW, which is short for Gas Metal Arc Welding is better known as MIG or Metal Inert Gas welding. To break it down further, it is welding with solid wire using an inert gas to shield the weld from atmospheric contamination.
GMAW is not good for welding outside or in drafty conditions. This is because the shield gas tends to blow away before it can do its job. Compared to FCAW the welds will be more visually appealing and have no slag to chip off. GMAW also welds thin metals with less burn-through compared to FCAW.
What is FCAW Welding?
FCAW which is short for Flux Core Arc Welding is done with the same wire machine as GMAW but doesn’t use gas to shield the weld. The wire is hollow and contains flux powder to shield the weld from atmospheric contamination instead of gas.
FCAW is not as good as GMAW at welding very thin materials as it tends to burn through easier. It also leaves a coating of slag on the finished weld that must be chipped off. However, welding outside is not an issue with FCAW, and penetration rates are typically better.
It can handle a little debris on the surfaces to be welded, whereas GMAW needs the welding surfaces to be very clean.
Selecting a machine that can perform both MIG and Flux Core welding is ideal to give you more versatility for your welding.
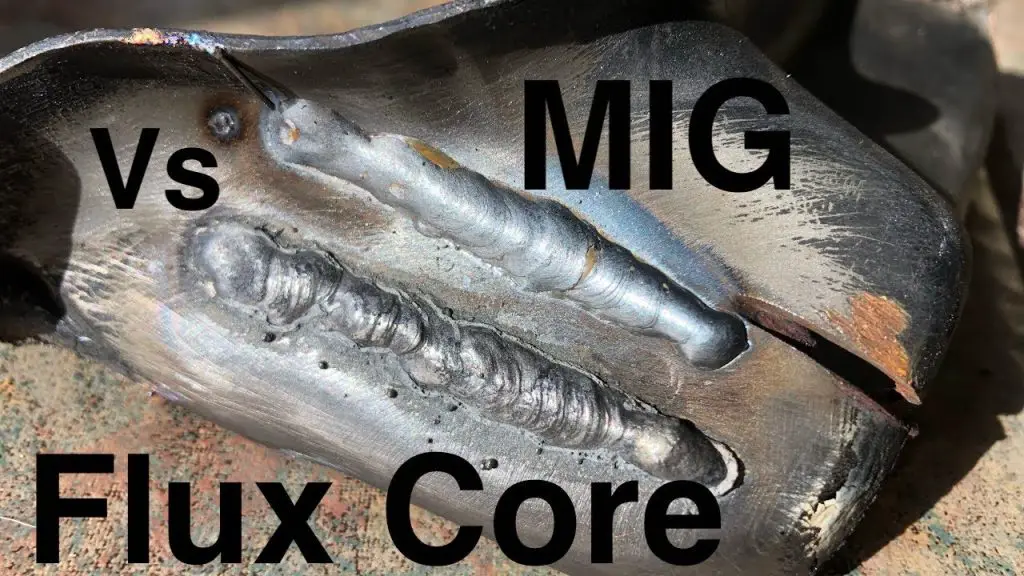
Should I Use Gas or Flux Core when Welding?
You should ask yourself, what is the thickness range of the metals you will be welding? This will help determine if a 115v will be adequate for building your projects and making repairs.
Every home will have several 115v outlets to plug a machine into. Therefore, a portable 115v machine looks attractive and is worth looking into.
Scenario One:
All your welding is expected to take place indoors on clean metals 24 to 12 gauge thick. 12 gauge is slightly less than 1/8″ thick. 24 gauge is less than 1/16″ thick.
If all of your planned projects and repairs fall within the parameters of this scenario, I suggest a 115v MIG welder like Hobart 50059 using gas with .025 diameter wire. The smaller wire will make it easier to weld the 24 gauge material. .030 wire will have a higher deposition rate and could also be used. The 115v will be the best for you in this scenario economically.
Scenario Two:
All your welding is expected to take place indoors on clean metals 1/8″ to 1/4″ thick.
For MIG welding with gas and .035 wire on metals within this thickness range, I suggest you step up to a higher capacity 230v machine. This upgrade in amperage and wire diameter will allow you to make fewer passes. Thus, saving you a lot of welding time in the process.
NOTE: For MIG welding metals in excess of 1/4" thick, a truly industrial machine with higher capacity will be necessary.
Scenario Three:
All of your welding is expected to take place both indoors and outdoors on metals 20 gauge up to 1/4″ thick.
We’ll need to move away from MIG and switch to .035 Flux-Core wire. This will not require a gas bottle, but the positive and negative leads will need to be switched on the machine. What is great is that a 115v machine will be sufficient to do the job.
NOTE: this is more than double the thickness that can be GMAW welded with a 115v machine.
Scenario Four:
All of your welding is expected to take place both indoors and outdoors on metals 1/4″ to 1/2″ thick.
We’ll need to stay with Flux-Core wire and step up to the .045 diameter. This will require a 230v machine. This amperage and wire diameter upgrade will allow you to make fewer passes. This will save you a lot of welding time in the process.
NOTE: this is more than double the thickness that can be FCAW welded with a 115v machine.
In Summary
The main questions that will determine the best machine, welding method and wire size are:
- What is the thickness range of the metals you expect to be welding?
- Where will you be welding, indoors or out?
- How clean will the metal surfaces be?
I hope we have at least provided the answers to these three main questions in a manner that is easy to understand.
For a deeper understanding of the differences between Flux and Shield Gas, please read my post called, “What is the purpose of flux and shield gas in the welding process“.
You may also find, “As a beginner what do I need to start welding“ helpful.
Read More
- Best Welding Machine for Beginners
- Which is Best Footwear for Welding?
- Best Welding Helmets for the Beginner
- 8 MIG Welding Beginner tips
- Do you push or pull flux core wire?
- Are Welding Machines Hard to Use?
- MIG vs TIG Welding
- What gas to use for MIG welding?
- Whats is difference between Spot and MIG Welding
- Differences Between 030 and .035 Flux Core Wire
- Magnetic Welding Clamps pros and cons