7018 welding rods are used to weld carbon and low alloy steel, while 6010 rods are used for stainless and nickel-based alloys. The 7018 welding rods typically provide deeper penetration, warmer, more stable arc, and short-circuiting capabilities than the 6010.
7018 and 6010 are both widely used in welding rods. They have different characteristics which make them suitable for different types of welding. In this article, we will describe the differences and some similarities between these two rods and what kind of welders prefer using one over the other.
This article will teach you all you need to know to confidently choose the proper rod for your next welding project. We’ll answer all of your questions and provide helpful tips along the process.
Table of Contents
6010 Welding Rod Uses
The E6010 welding rod excels in versatility, offering deep penetration and fast-freezing cellulose flux for all-position, DC-only welding. Widely employed for root pass welds, this rod is ideal for stove pipe welding, pipeline construction, and maintenance work, ensuring strong, durable, and efficient results.
7018 Welding Rod Uses
The 7018 welding rod is renowned for its low-hydrogen, AC/DC compatibility and smooth, easily controlled welds. Favored for its crack resistance and superior tensile strength, it’s perfect for structural steel, pressure vessels, and heavy equipment repairs, ensuring dependable, high-quality outcomes.
How to Read Welding Rod Numbers
The 7018 and 6010 welding rods each have a number associated with them. These numbers are important and represent different characteristics. Knowing what each letter represents is important so you can determine which rod to use in certain situations.
First Two Numbers
The first two numbers in the name of a rod represents the percentage of alloy elements. In this case, 1 and 8 mean that 01% carbon and 08% manganese are in the alloy mixed to produce the rods.
In case of 6010 welding rod , the carbon in the alloy is 01% and there is no manganese.
NOTE: The higher the carbon content, the less ductile puddle it produces. This means that the weld puddle will not be as fluid when you are welding with 6010 rod compared to 7018 rod.
The Third Number
The third number in the code represents the working position. Therefore, for 6010 rod you can work in all positions and it is considered a multipurpose electrode. 7018 rod on the other hand, works great when you MIG weld in flat or horizontal positions. This means that if you want to use 7018 rods for vertical welding, you may need to increase the amount of heat.
The Last Number
This represents the tensile strength of the material. And again, because 7018 rod requires more heat it will have higher tensile strength compared to 6010 rods which has lower weldability requirements.
NOTE: You always want to use the right rod for your application and if you can get your hands on either one of these materials we recommend doing so because of the differences in performance. If not, don't sweat it! You can still make a great-looking weld with either one.
Differences Between 7018 and 6010 Welding Rods
If you decide to become a welder, you should be aware of the distinctions between 7018 and 6010 electrodes, as they are two of the most commonly used and popular options on the market. Let’s compare them:
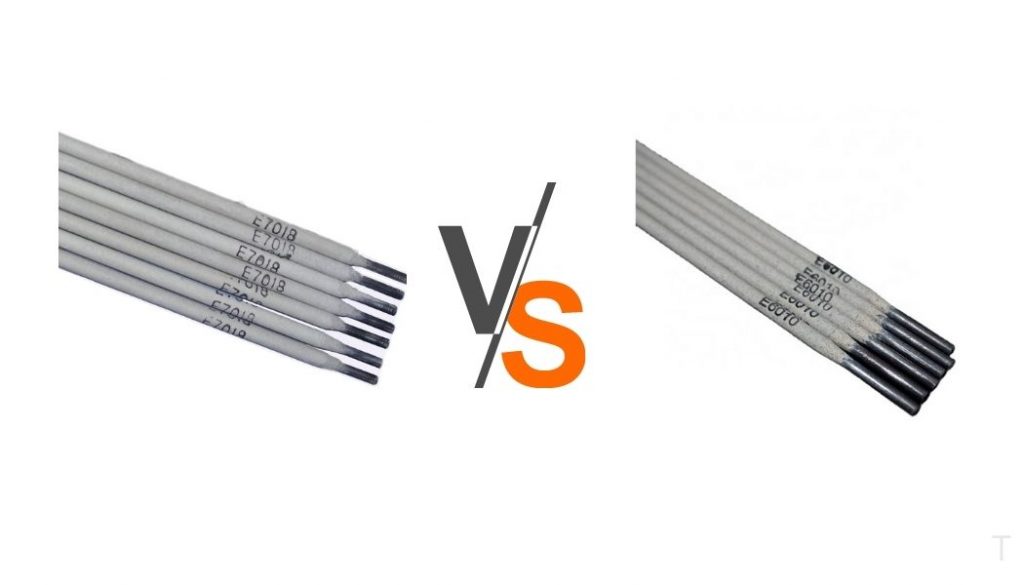
Composition
The 6010 welding rods are composed of 85% Iron and 15% Chromium. The 7018 rods, on the other hand, consist of 95% Iron and 5% Cobalt. This difference in composition is what makes them suitable for different applications because different types of metals needs to be welded.
Pricing
The 6010 electrodes are priced more affordably than 7018 rods. This is because they contain higher amounts of cobalt and iron. The added cobalt makes them suitable for welding stainless steels with high chromium content and the iron increases its tensile strength.
Welding Current
When it comes to welding current, both rods can be used on the same amperage range however, 6010 will require less amperage because it has a high resistance which reduces power loss and requires good welder skills.
TIP: 7018 welding rod is a good option for welding thin materials because it requires less heat.
Wire Coating
7018 rods have a thin nickel coating that makes it easier for welding fume extraction. However, 6010 electrodes are bare which allow the weld fumes to go directly into the air without passing through the wire first.
TIP: 7018 Welding rods have a brown, paper-like coating, while 6010 electrodes have a pale green coating, making it easy for you to distinguish between the two.
Welding Positions
6010 electrodes can be used for all welding positions because it has a good resistance to the elements and weld metals. The 7018 rods on the other hand, should not be used in horizontal position or wall butt joints because they run off quickly due to their low resistance and you will have less chance of producing porosity.
TIP: Welders who prefer using 7018 usually do so when welding thin or small parts because they need to hold them for a short period of time and does not leave much room for error when positioning them during the weld process.
Ferrous or Non-Ferrous Material
7018 welding rod is a good option for welding thin materials because it requires less heat. On the other hand, 6010 electrodes can be used on all types of metal except aluminum because it creates porous welds when used to weld this type of metal and will require extra prep work prior to welding process such as adjusting welder voltage and wire feed speed accordingly.
Porosity and Arc Performance
6010 electrodes do not have porosity problems during welding while 7018 does because it has a higher content of cobalt which is a “noble” metal that is very susceptible to corrosion when it’s exposed to oxygen.
When this happens tiny holes appear in the weld bead as a result of gas shielding issue that causes poor arc starts and unstable arc operation.
TIP: You can prevent this by using argon gas shielding and pre-heating the base material before welding.
Tensile Strength and Yield Strength
You can achieve higher tensile and yield strength in the weld metal if you use 7018 electrodes. This is because it has a lower iron content than 6010 electrodes which means it will need less heat input to melt and deposit filler metals.
TIP: This is important to consider especially when welding metals that require a lot of heat input such as cast iron and stainless steel where excessive heat input can cause the base metal to distort or warp.
Abrasion Resistance
Both types of electrodes have good abrasion resistance, however, 7018 rods produce more spatter because they are thinner and harder to control due to their high shrinkage rate.
TIP: You can reduce the amount of spatter on 7018 welding rod by thoroughly cleaning it before use.
Thermal Stability
6010 electrode has better thermal stability than 7018 rods because it has less cobalt, making it susceptible to cracking.
TIP: This is especially important to consider when welding on thick sections of metal because it requires a lot of heat input, therefore, thermal stability becomes more critical.
Elongation
If you want to achieve higher elongation in the weld metal, use 6010 electrodes because they have a higher nickel content, making them more ductile. This will result in lower strength of the weld metal when compared to 7018 rods that are known for its high strength.
TIP: For welding thin materials, you can still achieve good elongation by using 7018 electrodes with less than 0.040-inch of diameter thickness.
What Type of Rod is Best for Beginner Welders?
If you’re just starting out as a welder, I suggest using 6010 and 7018 electrodes to learn the process. The reason is that they both have high strength which is something you want in your weld beads even if you’re just starting out.
When you want to weld od stainless steel, I suggest you to buy 6010 rods because they require less heat input compared to 7018 electrodes. This means that you will save money from not having to replace melted electrodes as often as possible when doing an underwater weld project.
On the other hand, when it comes to welding cast iron, you need to use 7018 electrodes because it provides good penetration and will prevent the spatter issue that can occur when using 6010 electrodes.
TIP: For getting a smooth finish on your welds you should consider grinding the area surrounding the bead if you used 7018 rods during welding process. This is because there might be porosity and surface contamination after welding. In addition, it is best to use filler metal such as 309L stainless steel for these type of project.
What Are the Similarities between 7018 and 6010 Rods?
We’ve covered some of the differences between 6010 and 7018 electrodes, but there are also some similarities.
- Both contain iron powder to produce grey or solid weld beads.
- You can use them on most metals except for aluminum, titanium and magnesium alloys.
- They are best suited for working in DC electrode positive polarity (reverse polarity) with straight polarity.
- Both usually come in 7/32-inch to 1/4-inch in diameter.
- They have a positive slag which is easy to remove.
- You need to store them in dry and well-ventilated area, away from moisture and open flame.
- Both types of electrodes have excellent strength properties that can give you great welds for your DIY projects or profession.
- They are both good options for welding rusty metal.
I have written a guide to the most common welding rod sizes you may find interesting.
Related Questions
How do I clean 7018 Rod before I start welding?
You can clean the dirtiest or rusty electrodes by soaking them in vinegar overnight! That way they will look like new again and ready for more work! You can also use stainless steel wire brushes and then put them in an acid bath like muriatic acid to clean your electrodes.
Which Welding rod provides a Better penetration?
Both 7018 and 6010 electrodes provide great penetration. However, as you might know, the 7018 rods have more cobalt content which makes them brittle compared to the 6010 electrode which is more ductile. In addition, this will result in lesser elongation of the weld metal when doing a vertical up welding position for 7018 rods.
How long do 7018 Rods last in a Day?
It depends on your individual welders and their skills! However, you will be able to get at least 50-60 feet of electrode if you’re welding on a flat ground position.
Further Reading
- How to Weld Vehicle Frame?
- A Beginners Guide to Welding Chromoly
- Beginner Welding Mistakes
- Differences Between Welding Brazing and Soldering
- A Welding Guide for Beginners
- Vertical Stick Welding Tips to Increase Weld Quality
- The Best Welding Machine for Beginners
- Beginner Projects for New Welders
- Lincoln Electric Pro MIG 180 Product Review